Summary:
Types of Idlers in Belt Conveyors: How They Impact Load Handling and Durability
What Are Idlers and Why Are They Important?
The Different Types of Idlers in Belt Conveyor
How Different Types of Idlers in Belt Conveyors Impact Load Handling?
Durability Considerations for Types of Idlers in Belt Conveyors
Choosing the Right Types of Idlers in Belt Conveyors for Your System
Idlers are crucial components of belt conveyors, playing a key role in ensuring that the system operates smoothly, efficiently, and reliably. They support the conveyor belt, maintain its alignment, and help in load distribution, ultimately affecting the overall performance of the entire system. Understanding the different types of idlers and how they function is essential for selecting the right ones for your specific needs, as they directly impact the efficiency, durability, and safety of the conveyor.
What Are Idlers and Why Are They Important?
Idlers are the rollers that support the belt of a conveyor system. Positioned along the length of the conveyor, they prevent the belt from sagging under the load it carries. They maintain tension, ensure proper tracking, and minimize the wear and tear that could occur from friction. Without the proper idlers, a conveyor belt could lose its alignment, reduce its efficiency, or even cause a complete system breakdown. Essentially, idlers are like the backbone of the conveyor, supporting the entire operation.
The importance of idlers can’t be overstated because they help to maintain proper belt tension, distribute the load, and prevent unnecessary wear. Choosing the right type of idlers ensures smoother operation, reduces maintenance costs, and improves the conveyor’s lifespan.
Basic Functionality of Idlers in Conveyor Systems
The primary function of idlers is to provide support to the conveyor belt as it moves materials. There are three main types of idlers typically used in a belt conveyor system: carrier idlers, return idlers, and impact idlers. Each one serves a specific purpose in the conveyor system’s overall performance.
Carrier Idlers: These are positioned along the carrying side of the belt and are designed to support the weight of the materials being transported. They keep the belt level and in place, ensuring it moves smoothly without any undue sagging or misalignment.
Return Idlers: Positioned on the return side of the conveyor, return idlers help the belt return to its starting point without excessive wear. They are crucial for tracking the belt, ensuring it moves back to the head pulley properly.
Impact Idlers: These are typically used where the belt is subject to heavy material loads, like at the loading point. They absorb shock and prevent damage to the belt caused by large or sharp objects.
Each type of idler plays a role in optimizing the movement of the belt and reducing the stress it experiences during use. The placement, alignment, and type of idlers chosen for a conveyor system can make a significant difference in how the system performs over time.
How the Types of Idlers Affect Conveyor Performance
The types of idlers used in a conveyor system are directly related to the overall efficiency and longevity of the system. Choosing the wrong type of idler, or neglecting to maintain them properly, can result in numerous issues, including belt misalignment, increased wear and tear, and potential conveyor failure.
For instance, if the wrong idler spacing is used, the belt could sag too much, leading to greater friction and energy consumption. On the other hand, properly selected idlers with the right load distribution capabilities can ensure the conveyor runs efficiently with minimal maintenance.
Additionally, idlers affect the belt’s tracking ability. Without the correct return and carrier idlers, the belt may veer off course, causing uneven material flow and potentially damaging the system. A well-maintained and correctly chosen set of idlers ensures that the conveyor remains aligned, the load is evenly distributed, and the system operates at peak efficiency.
Understanding the nuances between the different types of idlers in belt conveyors is key to making informed decisions that will improve the reliability and performance of your material handling system.
The Different Types of Idlers in Belt Conveyors
Belt conveyors are essential systems used in industries ranging from manufacturing to mining. To keep these systems running smoothly, idlers are installed at various points along the conveyor belt. Idlers play a vital role in supporting the belt, maintaining its alignment, and ensuring efficient material transport. There are several types of idlers in belt conveyors, each serving a specific function designed to optimize the system’s performance. Understanding these types is crucial for ensuring that your conveyor system operates smoothly and efficiently.
Carrier Idlers: Support and Stability for the Belt
Carrier idlers are the most commonly used type in conveyor systems. These idlers support the carrying side of the belt, which holds the materials being transported. They are placed along the length of the conveyor and are positioned underneath the belt to maintain its stability and help distribute the weight of the materials evenly.
How They Work: Carrier idlers work by keeping the belt level and aligned. They prevent the belt from sagging or deflecting under heavy loads, which can cause excessive wear and reduce the efficiency of the conveyor. Carrier idlers are typically spaced at regular intervals and come in various designs, including flat, trough, or vee-shaped idlers, depending on the material being moved and the design of the system.
Applications:
- Ideal for conveying bulk materials like coal, grain, and aggregates.
- Suitable for applications where the load needs to be evenly distributed across the conveyor belt.
Return Idlers: Ensuring Proper Belt Tracking
Return idlers are placed on the underside of the conveyor belt, on the return side (the section where the belt travels back to the head pulley). These idlers are essential for tracking the belt and maintaining its alignment as it returns after completing its load-carrying cycle. They help keep the belt in place and reduce the friction between the belt and the conveyor structure.
How They Work: Return idlers prevent the conveyor belt from drifting off track during its return journey. By supporting the belt evenly and ensuring smooth movement, these idlers also help reduce the risk of the belt becoming misaligned, which can cause inefficient operation or even system failure. Return idlers are often flat and have a simple, straightforward design, but some can have specially engineered features for specific applications.
Applications:
- Used in any conveyor system to maintain belt tracking.
- Essential for longer conveyor belts where belt movement needs careful control.
Impact Idlers: Protecting the Belt from Heavy Loads
Impact idlers are placed at critical points along the conveyor, particularly where heavy materials are loaded onto the belt, such as at the loading zone or discharge points. These idlers are designed to absorb the shock and impact of large, heavy, or sharp materials that could potentially damage the conveyor belt. Impact idlers prevent excessive stress on the belt by cushioning the load and distributing the impact forces more evenly.
How They Work: Impact idlers are typically designed with a stronger, shock-absorbing material, such as rubber or a special polymer, which acts as a buffer. They are often used in combination with other idlers to ensure the smooth handling of materials. The cushioning effect of impact idlers reduces wear and tear on both the belt and the other idlers, increasing the lifespan of the conveyor system.
Applications:
- Used in mining, cement, and quarrying industries, where materials like rocks, gravel, or ore are loaded onto the conveyor belt.
- Essential for conveyors that handle large or heavy items, preventing damage to both the materials and the belt.
Trough Idlers: For Bulk Material Conveying
Trough idlers are a special variation of carrier idlers. These idlers are shaped like a trough (or a V-shape) and are designed to help contain bulk materials more effectively as they move along the conveyor. The trough design helps keep materials from spilling off the edges of the belt during transport, making them ideal for bulk handling applications.
How They Work: Trough idlers guide the belt into a V-shape, which keeps the materials centered and helps prevent spillage. The troughing action provides additional support for the conveyor belt and helps distribute the material load evenly, even in high-capacity applications. They are often used in combination with flat idlers in different parts of the conveyor system.
Applications:
- Commonly used in industries where bulk materials like coal, ore, and sand are being transported.
- Ideal for applications where the belt needs to hold large, loose materials securely.
Self-Cleaning Idlers: Minimizing Maintenance
Self-cleaning idlers are designed to reduce the need for regular maintenance by preventing the build-up of dirt, debris, or materials that may become lodged in the idler rollers. These idlers have special features, such as rotating brushes or scraper systems, that actively clean the rollers during operation.
How They Work: Self-cleaning idlers are often used in environments where sticky or wet materials are transported, as these materials tend to accumulate on the idler rollers. The self-cleaning mechanism helps ensure that the idlers continue to operate efficiently without obstruction, reducing the risk of belt misalignment or other operational issues.
Applications:
- Used in environments where sticky materials like clay, mud, or wet sand are being moved.
- Suitable for industries that require low-maintenance conveyor systems to keep downtime to a minimum.
In summary, the types of idlers in belt conveyors are specialized components designed to serve different roles, ensuring that the system operates efficiently and effectively. From supporting the belt with carrier idlers to protecting it with impact idlers, each type of idler contributes to the overall performance and longevity of the conveyor system. Understanding these different types of idlers and their functions is key to selecting the right components for your specific material handling needs.
How Different Types of Idlers in Belt Conveyors Impact Load Handling?
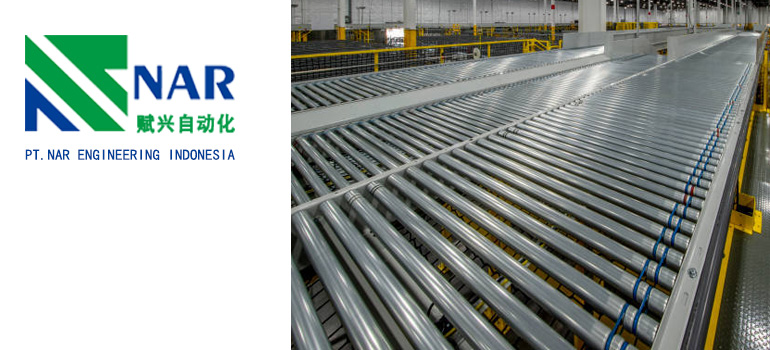
Idlers are crucial components in the operation of belt conveyors, especially when it comes to load handling. Whether you’re transporting bulk materials, heavy goods, or even fragile items, idlers play a significant role in ensuring the smooth movement of materials along the conveyor system. Different types of idlers—each designed for specific tasks—directly affect how the load is distributed, how the belt performs, and the overall efficiency of the conveyor.
Understanding how each type of idler impacts load handling is essential for choosing the right idlers for your system, which in turn ensures optimal performance, reduced maintenance, and longer system life. Let’s dive into how the various types of idlers affect the handling of loads in a belt conveyor system.
The Role of Idlers in Weight Distribution
The types of idlers used in a conveyor system play a crucial role in how weight is distributed across the belt. Proper weight distribution ensures that the conveyor operates efficiently, reducing wear on the belt and minimizing the risk of damage to both the conveyor components and the transported material.
Carrier Idlers are responsible for supporting the belt and the load it carries. The number and spacing of carrier idlers directly affect how evenly the load is distributed. If carrier idlers are spaced too far apart, the belt could sag in between, resulting in uneven load distribution. This could cause additional stress on the belt, leading to higher friction and reduced efficiency. On the other hand, when carrier idlers are spaced correctly, they help evenly distribute the weight across the belt, reducing strain and wear.
Trough Idlers are especially beneficial for bulk material handling. Their V-shaped design helps contain the material, ensuring that it stays centered on the belt and preventing spillage. Troughing idlers not only support the belt but also help evenly distribute the load of bulk materials, which is essential for handling larger quantities of material at once. When used correctly, they prevent uneven load distribution, which can lead to belt misalignment or material loss.
Idler Spacing and Load Efficiency
Proper spacing between idlers is vital for the overall efficiency of a conveyor system, particularly when handling heavy or bulky loads. Spacing that’s too wide can lead to a poorly supported belt, resulting in sagging and excessive wear. Spacing that’s too tight can cause unnecessary friction and reduce the conveyor’s throughput.
Carrier Idlers should be spaced in a way that supports the weight of the load without compromising the belt’s stability. For example, when transporting heavy or large items, the carrier idlers need to be placed closer together to provide adequate support and avoid sagging. This helps the conveyor belt maintain its tension and prevents it from losing alignment under the weight of the material.
Return Idlers are crucial for ensuring that the belt moves smoothly along the return section of the conveyor. Proper spacing of return idlers is important for minimizing friction and ensuring that the belt remains in its proper alignment. If return idlers are too far apart, the belt could drift or misalign, causing inefficiencies during material transport and potentially causing damage to both the belt and the materials.
How Idler Design Affects Material Flow
The design of idlers has a direct impact on how materials flow through the conveyor system. Some types of idlers are designed to ensure that the belt remains properly aligned and that the load is carried without excessive friction, while others are specifically designed to protect the belt and absorb shock when materials are loaded onto the belt.
Impact Idlers play an essential role in absorbing the shock and impact when heavy or abrasive materials are loaded onto the belt. Without impact idlers, the force of the load can cause unnecessary strain on the belt, leading to premature wear and potential belt failure. By cushioning the impact, these idlers ensure that the material flows smoothly onto the conveyor, preventing belt damage and improving the overall system’s efficiency.
Self-Cleaning Idlers also impact material flow, particularly in environments where sticky or wet materials are transported. These idlers prevent the build-up of debris on the rollers, ensuring that the belt remains clear and the material can flow without obstruction. Self-cleaning idlers are essential when dealing with materials that could clog the system, ensuring that the flow remains consistent and preventing blockages that could halt the system or cause damage to the belt.
Reducing Wear and Tear on the Conveyor System
Proper load handling by idlers can significantly reduce the wear and tear on the conveyor system, extending the life of both the conveyor belt and the idlers themselves. When the load is evenly distributed and the belt remains properly aligned, the stress placed on the system is minimized, preventing premature failure of key components.
Carrier and Return Idlers help reduce excessive friction and wear by ensuring the belt stays properly tensioned and aligned. When the belt moves smoothly and doesn’t sag or shift under the weight of the material, it experiences less stress, leading to fewer maintenance requirements and a longer lifespan for the entire conveyor system.
Impact Idlers, by absorbing shock and minimizing stress at the loading points, also reduce wear on the belt and surrounding components. They protect the belt from large or heavy loads that might otherwise cause tears or abrasions, leading to expensive repairs and downtime.
Durability Considerations for Types of Idlers in Belt Conveyors
When it comes to belt conveyors, durability is a critical factor to consider for both the idlers and the system as a whole. Idlers are subjected to constant wear and tear from the weight of materials, shock loads, friction, and environmental conditions. The right selection and maintenance of idlers can ensure longer service life, fewer breakdowns, and reduced maintenance costs. Understanding the key durability considerations for different types of idlers can help in making informed decisions about their use, ultimately leading to improved system performance and reduced downtime.
Material Choices for Idlers and Their Longevity
One of the most significant factors that affect the durability of idlers is the material from which they are made. Idlers are available in a variety of materials, each offering specific benefits and drawbacks in terms of wear resistance, load-bearing capacity, and environmental adaptability.
Steel Idlers: Steel is a common material choice for idlers due to its strength and durability. Steel idlers are often used in environments where they will bear heavy loads or experience high levels of stress. They are resistant to wear and deformation, making them ideal for applications in mining, bulk handling, and other industrial processes. However, steel idlers can be vulnerable to corrosion, especially in wet or humid conditions.
Rubber-Coated Idlers: To address the potential issue of corrosion in steel, some idlers are coated with rubber or other corrosion-resistant materials. This provides additional protection against moisture, acids, and other corrosive substances commonly found in certain environments. Rubber-coated idlers are also quieter and can reduce vibration, which is beneficial for conveyor systems where noise reduction is important.
Plastic Idlers: In certain specialized applications, such as food processing or where low friction is critical, plastic idlers are used. These idlers tend to be more resistant to chemicals, moisture, and temperature fluctuations than their steel counterparts. However, they may not be as strong as steel and are often used in lighter-duty applications.
The material choice affects not only the idlers’ durability but also their resistance to external factors like moisture, heat, and chemical exposure. Selecting the right material based on the operating environment is crucial to prolonging the lifespan of the idlers.
Impact of Environmental Factors on Idler Durability
Environmental conditions are one of the most important considerations when it comes to the durability of idlers in a belt conveyor system. Temperature extremes, moisture levels, dust, and corrosive substances can all play a role in determining how long your idlers will last.
Temperature Extremes: Conveyor systems in extreme temperature environments—whether high or low—can cause wear on the idlers. For example, in high-temperature settings (such as those found in cement plants), the metal components of idlers may expand and contract, leading to potential failure or reduced efficiency. In cold environments, materials may become brittle, increasing the risk of cracks and damage. To address this, idlers must be made from materials that can withstand the temperature range of the environment in which they will be used.
Moisture and Corrosion: Idlers exposed to moisture, whether from rain, humidity, or wet materials, are at risk of corrosion and rust, which can significantly shorten their lifespan. This is especially true for steel idlers without proper coating. To combat this, corrosion-resistant materials or coatings, such as rubber, stainless steel, or specialized paint, are often used. Additionally, regular maintenance and inspection are required to ensure that the idlers remain in good condition.
Dust and Debris: In dusty environments—such as mining operations—idlers may accumulate dirt and debris, which can impair their function and lead to excessive wear. Self-cleaning idlers can help mitigate this issue by preventing the build-up of materials around the rollers. Proper sealing of idlers is also essential to keep dust and other particulates from causing friction or damage.
Maintenance Tips to Extend the Life of Idlers
The durability of idlers is not solely determined by the material they are made of or the environment in which they operate. Proper maintenance is essential to ensure their longevity and prevent unnecessary breakdowns or failures. Regular maintenance checks and proactive care can go a long way in extending the life of idlers.
Regular Inspections: Performing routine inspections of idlers helps identify potential issues before they escalate. This includes checking for signs of wear, corrosion, misalignment, and any other visible damage. Pay special attention to the condition of the bearings and seals, as these are critical components that can fail due to improper lubrication or prolonged use.
Lubrication: Bearings within idlers require proper lubrication to function efficiently and reduce friction. Lack of lubrication can lead to overheating, premature wear, and even complete failure of the idlers. Regularly lubricating the bearings and moving parts of the idlers will help minimize friction, prevent wear, and extend their lifespan.
Cleaning: Dust, dirt, and debris can accumulate around idlers, especially in environments where bulk materials are being transported. This accumulation can cause friction, increase wear, and even clog the system. Regular cleaning of idlers—particularly self-cleaning types—ensures that they function properly and do not become obstructed.
Replacement of Worn Parts: Over time, components such as bearings, seals, and rollers may begin to wear down. Timely replacement of these parts prevents further damage to the idlers and ensures continued smooth operation. It’s important to replace any damaged or worn-out components before they cause system failure or disrupt conveyor performance.
Idler Alignment and Load Handling
Proper alignment of idlers is another key factor in ensuring their durability. Misalignment of the idlers can result in uneven loading, causing excessive wear on the idlers and the belt itself. It can also lead to belt tracking problems, which could cause the conveyor to fail.
Regularly checking and adjusting the alignment of the idlers helps distribute the load evenly across the belt and reduces unnecessary strain on both the idlers and the conveyor belt. Proper alignment ensures that the idlers perform their intended function and enhances the overall efficiency of the conveyor system.
Choosing the Right Types of Idlers in Belt Conveyors for Your System
Selecting the right types of idlers for your belt conveyor system is crucial to ensure smooth, efficient operation and long-term reliability. Idlers are not one-size-fits-all; they vary in design, material, and functionality, each suited for specific tasks. The proper idler selection can enhance load handling, reduce maintenance costs, extend the life of the conveyor system, and improve overall performance. Let’s dive into the key factors that influence the choice of idlers for your belt conveyor system.
Consider the Type of Materials You’re Handling
The type of materials you need to transport is one of the most important considerations when selecting idlers. Different materials, such as bulk items, heavy goods, or fragile products, place varying demands on the conveyor system.
Bulk Materials: For handling materials like coal, ore, sand, or gravel, trough idlers are ideal. Their V-shaped design helps contain the material, preventing spillage while ensuring the load is evenly distributed across the belt. Trough idlers are essential in high-capacity systems that deal with large volumes of bulk goods.
Heavy Loads: If you’re handling heavy or dense items, carrier idlers with higher load-bearing capacity are crucial. Carrier idlers support the weight of the load while maintaining belt stability. In some cases, using impact idlers at loading points will help cushion heavy materials as they land on the belt, protecting both the conveyor system and the belt itself from damage caused by shock loads.
Fragile or Sensitive Materials: For industries such as food processing, pharmaceuticals, or packaging, where the materials are often delicate, plastic or rubber-coated idlers may be a better choice. These idlers reduce friction and provide a smoother surface, which helps in handling fragile materials without causing damage.
Evaluate the Operating Environment
The environmental conditions where your belt conveyor system operates can significantly impact the durability and effectiveness of the idlers. Temperature, moisture, dust, and exposure to chemicals all play a role in determining which idlers are best suited for the job.
High-Temperature Environments: In industries such as cement manufacturing or steel production, where extreme heat is common, it’s important to choose idlers made of materials that can withstand these conditions. Steel idlers are often the best option in such environments, though they may require rubber or ceramic coatings to prevent degradation from high temperatures.
Wet or Humid Conditions: For systems that operate in humid or wet environments (such as food production or mining), corrosion can become a significant concern. To prevent rust and corrosion, opt for corrosion-resistant idlers made from stainless steel, rubber, or specialized coatings that can protect the components from moisture damage.
Dusty Environments: If your conveyor system operates in dusty conditions—common in mining, quarrying, or cement manufacturing—selecting self-cleaning idlers can reduce the accumulation of dust and debris on the rollers. These idlers are designed to automatically clean themselves, preventing material buildup that could cause friction and reduce the efficiency of the system.
Factor in Conveyor Length and Belt Load
The length of your conveyor system and the weight of the material being carried will influence the number and type of idlers needed to ensure proper support and load distribution.
Longer Conveyors: In long conveyor systems, idlers should be spaced more closely to avoid sagging and ensure proper belt alignment. For extended conveyors, you might need to use multiple sets of carrier idlers and possibly additional return idlers to keep the belt in alignment as it moves back to the head pulley.
Heavy or Uneven Loads: If your system needs to handle heavy, uneven, or bulky materials, it’s crucial to choose idlers that offer additional support, such as heavy-duty carrier idlers or impact-resistant idlers at loading zones. Idlers with a higher load-bearing capacity can distribute the weight more evenly across the belt, preventing excessive wear and tear.
Choose Based on Maintenance and Longevity Needs
Maintenance costs can add up quickly if your idlers aren’t chosen correctly. To reduce downtime and costly repairs, consider how the type of idlers you choose will impact the maintenance requirements and the overall lifespan of the conveyor system.
Self-Cleaning Idlers: If the materials you’re transporting tend to accumulate on the rollers, leading to excessive friction and wear, self-cleaning idlers can be an excellent choice. These idlers prevent material buildup, reducing the need for frequent maintenance. This is particularly beneficial in environments where the material is sticky or tends to clog the system.
Low-Maintenance Options: If your system demands minimal downtime, opt for sealed idlers that are designed to keep dust and moisture out, preventing premature wear and tear. Additionally, rubber-coated or plastic idlers tend to require less maintenance in some environments due to their smooth surfaces and resistance to corrosion.
Understand Cost vs. Performance Balance
While it’s tempting to choose the most cost-effective idlers, it’s essential to consider the trade-off between cost and performance. Choosing cheaper idlers might save money upfront, but they could result in more frequent repairs, shorter lifespans, and higher overall operating costs in the long run.
Long-Term Investment: Investing in high-quality, durable idlers—especially for high-load or high-capacity systems—can provide a better return on investment. For example, heavy-duty steel idlers might cost more initially, but they are built to last and can handle larger loads, which reduces the frequency of repairs and replacements.
Economical Options for Light-Duty Applications: If your system handles lighter loads and operates in less demanding environments, opting for plastic or rubber-coated idlers may provide a more economical solution without compromising performance.
Consider the Idler’s Role in Belt Alignment and Tracking
Belt alignment and tracking are critical for ensuring that the conveyor operates smoothly and efficiently. Misaligned belts can lead to increased wear, material spillage, and even belt failure. Certain idlers are specifically designed to improve belt tracking and alignment.
Tracking Idlers: Idlers designed specifically for tracking are essential when maintaining proper belt alignment. These idlers are often placed at strategic locations to ensure that the belt stays centered and moves smoothly along the conveyor path. When choosing idlers for your system, ensure that they include a combination of idler rollers and tracking devices to help maintain the proper belt position.