Summary:
The Ultimate Guide to Conveyor Belt Cleaners: Enhance Efficiency and Reduce Downtime
What Are Conveyor Belt Cleaners and How Do They Work?
Key Benefits of Using Conveyor Belt Cleaners in Your Facility
Choosing the Right Conveyor Belt Cleaner for Your Needs
Common Conveyor Belt Cleaning Problems and How to Solve Them
Best Practices for Maintaining Conveyor Belt Cleaners
What Are Conveyor Belt Cleaners and How Do They Work?
Conveyor belts are the backbone of many industrial processes, moving goods and materials efficiently across factories, warehouses, and production lines. But, as with any piece of machinery that operates continuously, conveyor belts are prone to accumulating debris, dust, and other contaminants. This is where conveyor belt cleaners come into play. They are designed to keep the belts clean and running smoothly, which ultimately ensures the productivity of your operations.
The Importance of Conveyor Belt Cleaners in Industrial Settings
In industrial environments, conveyor belts are constantly exposed to various materials—whether it’s raw materials, finished products, or waste. Over time, this exposure can lead to the build-up of sticky substances, dust, oil, or even hazardous materials that could compromise the belt’s performance. Conveyor belt cleaners help prevent these issues by removing unwanted material, reducing the risk of equipment failure, and maintaining a safe working environment.
When conveyor belts are clean, they run more efficiently, reducing downtime and the likelihood of unexpected maintenance issues. Without these cleaners, the conveyor system may face frequent breakdowns, increased wear and tear, and even contamination of products, which could lead to costly recalls or quality control issues.
Types of Conveyor Belt Cleaners and Their Functions
There are several types of conveyor belt cleaners available, each designed to address specific cleaning needs. These can be broadly classified into two categories: primary and secondary cleaners.
Primary Conveyor Belt Cleaners: These are typically installed at the discharge point of the conveyor and are responsible for removing the majority of material from the belt. They usually come in the form of rotating blades or scrapers that physically remove debris as the belt moves.
Secondary Conveyor Belt Cleaners: These are installed further down the line, usually after the primary cleaner, to tackle any remaining material. They are often designed with more advanced features, such as adjustable pressure or oscillating blades, to ensure a thorough clean.
Additionally, there are specialized cleaners for specific industries—such as food-grade or heavy-duty models—that are designed to meet the unique demands of certain environments.
How Conveyor Belt Cleaners Improve Conveyor Efficiency
The efficiency of a conveyor system heavily depends on its cleanliness. When debris accumulates on the conveyor belt, it can cause several operational issues. Slippage, misalignment, and even mechanical failure are common problems that can arise from a dirty belt. Conveyor belt cleaners eliminate these risks by ensuring the belt remains clear of any material that could interfere with its movement.
By maintaining a cleaner surface, the system operates with greater consistency and less friction, which ultimately improves its speed and reliability. Cleaner belts also reduce the risk of damage to other components, such as motors, pulleys, and bearings, further contributing to the longevity of the entire system.
Moreover, cleaner belts are more energy-efficient. When dirt and debris build up, the system has to work harder to move materials, requiring more power and increasing energy consumption. Conveyor belt cleaners help to mitigate this issue by reducing friction and enabling the system to run more efficiently, potentially saving you on energy costs over time.
Key Benefits of Using Conveyor Belt Cleaners in Your Facility
Conveyor belts are essential for moving goods and materials in various industries. However, without proper cleaning, the accumulation of debris and contaminants can drastically affect performance. Conveyor belt cleaners play a crucial role in maintaining belt hygiene and efficiency. In this section, we’ll explore the key benefits of using conveyor belt cleaners in your facility.
Reducing Maintenance Costs with Conveyor Belt Cleaners
One of the most significant advantages of using conveyor belt cleaners is the reduction in maintenance costs. Conveyor systems are expensive to repair, and downtime due to a dirty belt can quickly add up. Without a cleaning system in place, debris buildup can lead to frequent repairs, replacement of belt components, and even system failure. Over time, this increases your operational costs.
By investing in conveyor belt cleaners, you’re proactively reducing the wear and tear on critical components, such as bearings, rollers, and motors. Cleaner belts also reduce friction, which means less strain on the entire system, extending its lifespan and lowering the frequency of costly repairs.
Regular cleaning also reduces the need for labor-intensive manual cleaning, which can be both time-consuming and inefficient. A good conveyor belt cleaner can automatically remove debris, saving time and ensuring your workers can focus on other important tasks.
Enhancing Safety with Cleaner Conveyor Systems
A clean conveyor belt isn’t just about improving performance—it’s also about ensuring safety in the workplace. In industries like food processing, pharmaceuticals, or mining, contaminants on the conveyor belt can pose significant health and safety risks. For example, materials like dust, grease, and food particles can create slip hazards for workers and lead to contamination of products.
Conveyor belt cleaners help mitigate these risks by keeping belts free from dangerous substances. By removing residue and preventing material build-up, cleaners help maintain a safer working environment, reduce slip-and-fall incidents, and comply with safety standards.
Additionally, certain industries require specific hygiene standards (e.g., food-grade conveyor systems), and using the right cleaner helps meet those standards. A hygienic conveyor system also prevents cross-contamination between products, which is vital for ensuring quality control and consumer safety.
Extending the Life of Your Conveyor Belt with Proper Cleaning
Conveyor belts are not cheap to replace, and the longer you can extend the life of your existing belts, the more cost-effective your operations will be. Conveyor belt cleaners help maintain the integrity of the belt by removing materials that could otherwise cause abrasion or wear. This is especially important for industries that deal with abrasive substances or heavy loads, such as mining or recycling.
When debris like sticky substances, dust, or sharp objects are left on the belt, they can cause undue friction and abrasion, leading to belt damage and premature wear. Conveyor belt cleaners help to reduce this risk by removing these materials before they cause any harm. Regular use of these cleaners can extend the service life of your belts, ultimately saving you money on replacements.
Moreover, cleaning your belts regularly helps maintain proper tension and alignment, which are critical factors for preventing early belt wear and maintaining optimal conveyor performance.
Improving Productivity with a Clean Conveyor System
A clean conveyor system operates more efficiently, which means more productive operations. When debris accumulates, it can lead to belt misalignment, reduced speed, or even jamming, all of which contribute to downtime and decreased productivity. Conveyor belt cleaners help prevent these issues by ensuring that the belt stays clear of any material that could interfere with its movement.
By keeping your conveyor belts clean, you reduce friction, improve the speed of material handling, and keep the system running at optimal capacity. This ultimately leads to fewer interruptions in your production process, higher throughput, and better overall productivity.
Cleaner systems also lead to better product quality. For example, in food processing, a cleaner belt reduces the risk of contamination, ensuring that the products that come off the conveyor are of the highest quality and meet industry standards.
Enhancing Environmental Sustainability
Conveyor belt cleaners not only improve the efficiency of your system but also contribute to a greener, more sustainable operation. By ensuring that your belt system runs smoothly, you can reduce energy consumption. Dirty belts can cause the system to work harder, using more energy and creating unnecessary waste. Cleaner belts reduce friction, which in turn reduces the amount of power needed to move goods.
Furthermore, conveyor belt cleaners can help reduce material loss. For example, in industries like mining or recycling, materials that accumulate on the belt can often be recovered and reused when they are properly cleaned. This not only reduces waste but also helps in cutting down on the need for new raw materials, aligning with more sustainable practices.
Choosing the Right Conveyor Belt Cleaner for Your Needs
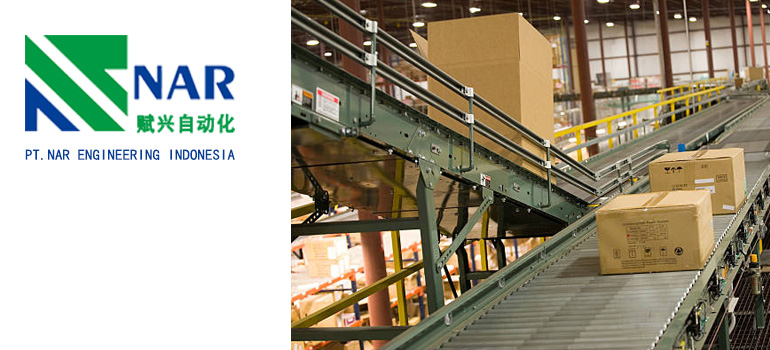
Selecting the right conveyor belt cleaner for your facility is essential to ensure optimal performance, reduce downtime, and maintain a safe working environment. With a wide variety of cleaners available, each designed for different needs and environments, it can be challenging to determine which one is best suited for your conveyor system. In this section, we’ll explore the key factors to consider when choosing the right conveyor belt cleaner for your specific needs.
Factors to Consider When Selecting Conveyor Belt Cleaners
Type of Material Being Conveyed
The type of material your conveyor system handles plays a significant role in determining the right cleaner. For example, if you’re transporting sticky materials, like wet coal or heavy oils, you’ll need a cleaner that is designed to deal with these tough substances. On the other hand, if you’re moving dry, non-abrasive materials like grains or powders, you may not need as heavy-duty a cleaner.
When selecting a cleaner, make sure it’s compatible with the type of material being conveyed to ensure it can effectively remove debris without causing damage to the belt or the cleaner itself.
Belt Type and Size
Not all belts are created equal. Different conveyor systems use varying types of belts, ranging from light-duty rubber belts to heavy-duty steel belts. The size of the belt also matters—wider or longer belts may require larger or more powerful cleaning systems.
Be sure to choose a cleaner that fits the specific dimensions of your belt. If the cleaner is too small or doesn’t cover enough surface area, it may not be effective in removing debris. Conversely, a cleaner that’s too large for the belt could lead to excessive wear or damage.
Environmental Conditions
The operating environment is another critical consideration. Conveyor systems in food processing plants, for instance, require hygienic and food-safe cleaners to prevent contamination, while those in heavy industries, such as mining or recycling, may need more rugged and durable cleaners to handle abrasive materials.
Consider factors such as:
- Temperature extremes: Some cleaners are designed to withstand high or low temperatures.
- Moisture and chemical exposure: For wet or corrosive environments, cleaners made from stainless steel or resistant materials may be necessary.
- Sanitation requirements: Food-grade conveyor cleaners need to meet specific industry standards to prevent contamination.
Choosing a cleaner that can perform well in your environment will extend the cleaner’s life and ensure it operates effectively.
Frequency of Cleaning
How often do you need to clean your conveyor system? If your conveyor operates continuously or handles large volumes of material, you’ll need a cleaner that can handle frequent use. For less demanding environments or systems that operate in shorter intervals, you might opt for a simpler, manual cleaner.
Some conveyor belt cleaners are designed to be more robust and durable, allowing them to work continuously without needing frequent replacement or maintenance. Others might be more specialized, such as models with adjustable pressure or advanced scrapers for heavy-duty cleaning.
Maintenance and Cost Considerations
While more advanced conveyor belt cleaners can offer better performance, they may also come with a higher upfront cost. Consider not just the initial investment but also long-term maintenance costs, including repairs, spare parts, and labor for maintenance. Ideally, you’ll want a solution that balances upfront cost with long-term efficiency and durability.
Some models require more frequent maintenance or adjustment, while others are more “set it and forget it.” Be sure to choose a cleaner that aligns with your facility’s maintenance capabilities.
Comparing Manual vs. Automated Conveyor Belt Cleaners
When choosing the right cleaner, you’ll likely need to decide between manual and automated cleaners. Here’s a quick breakdown of both options:
Manual Conveyor Belt Cleaners: These are typically simple, hand-operated devices, such as scrapers or brushes, that require human intervention to remove debris from the conveyor belt. While manual cleaners are often more affordable upfront, they can be time-consuming and less efficient, particularly for large-scale operations. They also pose a higher risk for human error and inconsistent results.
Automated Conveyor Belt Cleaners: These systems are more advanced and designed to clean the conveyor belt automatically. They often consist of rotating brushes, blades, or scrapers that remove debris without human intervention. Automated cleaners tend to be more efficient and reliable, offering consistent results and reducing downtime. However, they come with a higher initial investment and require proper installation and occasional calibration to ensure optimal performance.
How to Evaluate Conveyor Belt Cleaner Efficiency
To ensure that you’re choosing the most effective conveyor belt cleaner for your system, consider these efficiency factors:
Cleaning Effectiveness: Does the cleaner remove most of the debris in one pass, or does it require multiple passes to achieve satisfactory results? The cleaner should be able to remove all types of materials (dust, oils, slurries, etc.) effectively without leaving residue behind.
Energy Consumption: Automated cleaners may consume more energy than manual cleaners. Evaluate the cleaner’s energy efficiency to determine whether the benefits of reduced labor and increased uptime outweigh the increased energy costs.
Durability: A good conveyor belt cleaner should be built to last, especially if your system runs 24/7 or handles tough materials. Look for cleaners that are designed for long-term use with minimal maintenance.
Adjustability: A cleaner with adjustable pressure or customizable features can be more versatile and suited to a range of materials and operational conditions. This flexibility ensures that your conveyor belt cleaner continues to work effectively as your needs evolve.
Common Conveyor Belt Cleaning Problems and How to Solve Them
Even with the best conveyor belt cleaners, issues can arise over time. Whether it’s due to incorrect maintenance, harsh operating conditions, or the nature of the materials being transported, understanding common conveyor belt cleaning problems can help you address them quickly and prevent costly downtime. In this section, we’ll discuss some of the most frequent conveyor belt cleaning problems and offer practical solutions to solve them.
Persistent Material Build-up on Conveyor Belts
Problem: One of the most common issues faced by conveyor systems is the persistent build-up of materials on the belt. Whether it’s dust, grease, mud, or sticky substances, accumulation can result in decreased efficiency, belt misalignment, and even damage to other components of the conveyor system.
Solution: To combat persistent material build-up, it’s essential to choose a conveyor belt cleaner with the appropriate cleaning mechanism for the type of material you’re dealing with. For example:
- Scrapers: For dry materials like dirt, powder, or sand, a high-quality scraper can effectively remove residue without damaging the belt.
- Brushes: For sticky or greasy substances, rotating brushes or air knives might be necessary to break up and remove these materials.
- Chemical Cleaners: In some cases, using specialized chemical cleaning agents can help loosen stubborn residues and make them easier to remove. These should be carefully selected based on your industry standards, especially in food or pharmaceutical sectors.
It’s also important to ensure that the cleaning system is correctly positioned and maintained, as poor placement or wear can reduce its effectiveness in dealing with material build-up.
Ineffective Conveyor Belt Cleaner Performance
Problem: Another issue arises when a conveyor belt cleaner fails to do its job effectively, leaving debris or build-up behind despite frequent cleaning. This could happen for several reasons, including improper cleaner selection, insufficient pressure, or worn-out components.
Solution: To fix ineffective cleaning, start by evaluating the type of conveyor belt cleaner you’re using. The cleaner should be suited for the material being transported and should cover the full width of the belt. If the cleaner isn’t making sufficient contact with the belt surface, the debris will remain, so proper pressure and alignment are key.
- Adjust the Cleaner’s Tension or Pressure: Many conveyor belt cleaners have adjustable settings that allow you to fine-tune the pressure or tension applied to the belt. Make sure the pressure is sufficient to remove materials without causing excessive wear on the belt or cleaner.
- Upgrade the Cleaner: If the current cleaner isn’t getting the job done, it might be time to upgrade to a more effective model. For instance, a primary cleaner combined with a secondary cleaner might provide a more thorough clean, especially for heavily contaminated belts.
Conveyor Belt Cleaner Damage or Wear
Problem: Over time, conveyor belt cleaners can experience wear and tear due to the constant friction against the belt surface, particularly in high-volume, high-speed applications. If left unchecked, worn-out cleaners can cause damage to the belt, resulting in costly repairs and downtime.
Solution: To prevent conveyor belt cleaner damage:
- Regular Inspections: Conduct frequent checks on the cleaner’s condition, especially the blades or scrapers. Replace worn parts promptly to avoid further damage to the cleaner or conveyor belt.
- Proper Tension and Alignment: Ensure that the cleaner is properly tensioned and aligned with the belt. Misalignment can cause uneven wear and may result in insufficient cleaning, leading to premature damage to both the cleaner and the belt.
Additionally, investing in durable, high-quality materials for your cleaner can help reduce the frequency of replacements. For example, ceramic-coated or steel-edged cleaners can last longer in abrasive environments compared to plastic or rubber components.
Slippage or Jamming of the Conveyor Belt
Problem: Slippage or jamming of the conveyor belt can occur when debris accumulates on the cleaner or the belt itself, increasing friction and disrupting the system’s smooth operation. This often leads to inefficient material transport, delays, or even belt damage.
Solution:
- Choose the Right Cleaner for Material Types: If your system is prone to slippage due to sticky or wet materials, consider upgrading to a brush-type cleaner or vibrating cleaner, which can better deal with such substances and prevent them from sticking to the belt.
- Regularly Clean the Cleaner: Sometimes, the problem isn’t just the belt but the cleaner itself. Clean the cleaner periodically to ensure it’s free of build-up and debris that could lead to slippage. For example, certain materials can get stuck on the cleaner’s blades, causing it to lose its cleaning effectiveness.
- Increase Belt Tension: If slippage persists, check the belt tension. Too little tension can cause slippage, especially under heavy loads. Adjusting the tension to ensure optimal contact between the belt and cleaner may help alleviate the issue.
Damage to the Conveyor Belt During Cleaning
Problem: While conveyor belt cleaners are designed to remove debris without damaging the belt, improper use or incorrect selection can sometimes result in damage to the belt itself. This can include cuts, tears, or excessive abrasion, leading to reduced belt life.
Solution: To prevent damage to the belt during cleaning:
- Choose the Right Type of Cleaner: Select a cleaner with a blade material that won’t cause excessive abrasion to the belt. For example, softer materials such as polyurethane or rubber may be better suited for delicate or non-abrasive belts.
- Adjust the Cleaning Pressure: Too much pressure from the cleaner can lead to belt damage. Ensure that the cleaning mechanism applies just enough pressure to clean effectively without scraping or gouging the belt surface.
- Proper Maintenance: Regularly inspect the condition of both the cleaner and the conveyor belt. Check for signs of excessive wear or damage, and replace any worn parts before they cause more serious damage.
Inconsistent Cleaning Results
Problem: Inconsistent cleaning results can occur if the cleaner isn’t performing at its full potential due to improper adjustments or wear. This may leave some areas of the conveyor belt clean while others remain dirty, reducing the overall effectiveness of your cleaning process.
Solution: To achieve consistent cleaning:
- Ensure Full Coverage: Make sure that the cleaner covers the full width of the conveyor belt. A cleaner that’s too narrow or incorrectly positioned won’t be able to clean the entire belt efficiently.
- Check for Proper Alignment: Misalignment can lead to uneven cleaning, so adjust the cleaner so that it applies even pressure across the belt surface.
- Use Multiple Cleaners: In some cases, using both primary and secondary cleaners in tandem can help achieve a more thorough, consistent clean, especially if you’re dealing with challenging materials or conditions.
Best Practices for Maintaining Conveyor Belt Cleaners
Proper maintenance of your conveyor belt cleaners is essential to ensure their longevity, reliability, and effectiveness in keeping your conveyor systems clean and running smoothly. Regular care not only extends the life of the cleaner but also improves the overall efficiency of your conveyor system, reduces downtime, and lowers maintenance costs. In this section, we’ll discuss the best practices for maintaining your conveyor belt cleaners.
Regular Inspection of Conveyor Belt Cleaners
Problem: Conveyor belt cleaners are constantly in contact with the belt surface, which means they experience wear and tear over time. If not properly inspected and maintained, worn-out components can affect cleaning performance and even damage the belt.
Best Practice:
- Scheduled Inspections: Establish a regular inspection schedule to check the condition of your conveyor belt cleaner. Look for signs of wear on blades, brushes, and other moving parts. Inspections should be done at least monthly or more frequently, depending on the type of materials your system handles and the operating environment.
- Check for Build-up: Ensure that no debris is collecting on the cleaner itself, as this can impair its ability to remove material from the belt.
- Look for Alignment Issues: Misalignment of the cleaner can lead to uneven cleaning or damage to both the cleaner and the conveyor belt. Ensure the cleaner is positioned correctly across the entire width of the belt.
Clean the Cleaner Regularly
Problem: Just as conveyor belts accumulate dirt and debris, conveyor belt cleaners themselves can collect residue, especially in environments where sticky or greasy materials are being transported. A dirty cleaner won’t perform efficiently.
Best Practice:
- Frequent Cleaning: Clean your conveyor belt cleaner regularly to prevent the build-up of material that could clog or degrade its cleaning effectiveness. Depending on your application, this could be done weekly, or more often in high-traffic or high-volume environments.
- Use Appropriate Cleaning Tools: Use soft brushes or air blowers to clear debris from the cleaner’s components. Avoid using harsh tools that could damage delicate parts like rubber blades or bristles.
- Monitor for Clogging: Regularly check for material build-up in the cleaner’s moving parts or between blades, especially in wet or sticky material applications. Clogging can reduce the effectiveness of the cleaner and cause unnecessary wear.
Adjust Tension and Pressure Regularly
Problem: The tension and pressure applied by conveyor belt cleaners are crucial for effective cleaning. Too much pressure can damage both the belt and the cleaner, while too little pressure won’t clean thoroughly, leading to material build-up.
Best Practice:
- Check Tension Regularly: Ensure the cleaner is properly tensioned. Over-tightening the cleaner can cause excessive friction on the belt, leading to wear and tear, while too little tension can result in ineffective cleaning.
- Adjust Pressure Based on Material Type: The type of material being transported can affect how much pressure the cleaner needs to apply. For example, sticky or heavy materials may require more pressure, while delicate or fragile materials may require gentler cleaning.
- Use Adjustable Cleaners: If your cleaner has adjustable pressure settings, fine-tune them regularly to optimize cleaning based on the material type, belt speed, and operating conditions.
Replace Worn or Damaged Parts Promptly
Problem: Over time, the components of a conveyor belt cleaner, such as scraper blades, brushes, and other moving parts, can become worn or damaged. This can significantly reduce the cleaner’s effectiveness and even lead to damage to the conveyor belt.
Best Practice:
- Monitor Wear and Tear: Keep a close eye on high-wear components like scraper blades, rubber seals, or brushes. These parts typically show signs of wear through cracking, tearing, or reduced cleaning efficiency.
- Replace Worn Parts: Replace damaged or worn-out components promptly. Delaying this could result in poor cleaning performance or even damage to the conveyor belt. Make sure you use the manufacturer’s recommended replacement parts for optimal performance.
- Use Durable Materials: For cleaner longevity, opt for high-quality, durable materials for the blades, brushes, and other components, especially in heavy-duty applications. Components like ceramic-edged scrapers or stainless steel brushes tend to last longer in abrasive environments.
Lubricate Moving Parts
Problem: Conveyor belt cleaners have moving parts that require lubrication to reduce friction and prevent wear. Without proper lubrication, these parts can become stiff, cause excessive friction, and lead to premature failure.
Best Practice:
- Lubricate Regularly: Use the correct lubricant for your cleaner’s components, such as bearings, pivot points, and rotating shafts. Be sure to follow the manufacturer’s guidelines for the proper lubricant to use, as incorrect lubricants can attract dirt and damage the parts.
- Monitor Lubrication Levels: Regularly check lubrication levels to ensure that parts are well-maintained. Some systems may require periodic re-lubrication, while others may feature sealed components that don’t need as much attention.
- Clean Before Lubricating: Always clean the parts before reapplying lubrication to avoid trapping debris inside the mechanisms.
Properly Train Personnel on Cleaner Maintenance
Problem: Lack of proper training can lead to improper maintenance or neglect of important cleaning tasks. Operators who aren’t familiar with the proper care procedures may overlook critical maintenance steps, resulting in poor performance or equipment damage.
Best Practice:
- Provide Training: Ensure that all personnel responsible for maintaining conveyor belt cleaners are properly trained on best practices. This includes understanding how to inspect, clean, adjust, and replace parts on the cleaner.
- Create a Maintenance Schedule: Develop a maintenance schedule that clearly outlines who is responsible for each task and when it should be performed. Make sure maintenance is conducted according to the schedule to avoid unexpected issues.
Consider Upgrading Cleaners Based on Evolving Needs
Problem: As your conveyor system evolves, so too should the cleaner system. Changes in the type of materials handled, increased production volumes, or more demanding operating conditions may require an upgraded or different cleaner.
Best Practice:
- Assess System Needs Regularly: Regularly evaluate whether your current conveyor belt cleaner is meeting your needs. If your materials change (e.g., from dry to wet, or from light to heavy), you may need to upgrade to a more powerful or specialized cleaner.
- Upgrade for Efficiency: In high-volume operations, consider upgrading to automated or high-efficiency cleaners. These models can handle larger volumes, higher speeds, and more challenging materials, improving overall system performance and reducing maintenance needs.
- Consult Experts: If you’re unsure whether your cleaner is the right fit for your system, consult with a conveyor belt cleaning expert who can assess your needs and recommend the most appropriate solution.
Maintaining your conveyor belt cleaners through regular inspections, cleaning, and proper adjustments is essential to keeping your conveyor system running smoothly. By following these best practices, you can extend the lifespan of your cleaner, reduce downtime, and ensure optimal performance of your conveyor system. Proper maintenance not only saves you money in the long run but also improves operational efficiency, reduces safety risks, and helps maintain product quality.