Summary:
Maximizing Productivity in Mining with Quality Conveyor Belt Accessories
Importance of High-Quality Conveyor Belt Accessories for Mining Operations
Key Conveyor Belt Accessories for Mining: Boosting Efficiency and Safety
How to Select the Right Conveyor Belt Accessories for Your Mining Project
Maintenance Best Practices for Conveyor Belt Accessories in Mining
Importance of High-Quality Conveyor Belt Accessories for Mining Operations
In mining operations, conveyor belt systems are the backbone of material transportation, ensuring that minerals, ores, and other materials are moved efficiently across long distances within the mine. To maximize productivity and reduce downtime, selecting high-quality conveyor belt accessories is crucial. While the conveyor belt itself plays a central role in material handling, the accessories that complement it — such as rollers, tensioning systems, and drive components — are equally important in ensuring optimal performance and longevity of the entire system. Choosing the right accessories can significantly improve operational efficiency, reduce maintenance costs, and extend the lifespan of the conveyor system.
Ensuring Continuous Production with Reliable Conveyor Belt Accessories
Mining operations often run 24/7, meaning uninterrupted performance is essential. Conveyor belt systems are required to operate continuously under heavy loads and demanding conditions, and high-quality accessories help ensure that these systems remain reliable and efficient. Accessories such as rollers, pulleys, and tensioning devices play a vital role in maintaining smooth, uninterrupted operation.
For example, conveyor rollers, which support the belt and help distribute the load, are critical to preventing belt misalignment, wear, and tear. Poor-quality rollers can lead to belt tracking issues, excessive friction, and premature failure, resulting in costly downtime and repairs. By investing in high-quality, durable rollers, mining operations can reduce the risk of system malfunctions and ensure a steady flow of materials, which ultimately leads to higher productivity.
Reducing Downtime Through Proper Conveyor Belt Maintenance
One of the most significant challenges in mining operations is minimizing equipment downtime. Downtime can result in significant production losses and increase maintenance costs. Conveyor belt accessories that are well-designed and high-quality help minimize wear and tear, reducing the frequency of repairs and ensuring the system remains operational for longer periods.
Belt cleaners, for example, are essential accessories that prevent material buildup on the conveyor belt. Accumulated debris can cause belt slippage, increase friction, and damage the belt surface, leading to inefficiencies and increased maintenance needs. High-performance belt cleaners help maintain the belt surface, keeping it free from build-up and ensuring smooth operation. Additionally, components like tensioning systems and drive pulleys, when properly maintained, keep the belt properly aligned and running efficiently, reducing the chances of belt failure and minimizing unexpected downtime.
The Impact of Quality Accessories on Mining Efficiency
The efficiency of a mining operation depends not only on the size of the equipment and the volume of material being processed but also on how well the entire conveyor system is functioning. High-quality conveyor belt accessories contribute directly to improving the overall efficiency of the material handling process. Well-designed accessories reduce friction, optimize material flow, and ensure that the conveyor belt operates at its maximum potential.
For instance, high-quality conveyor belt rollers can reduce the amount of energy required to move material by minimizing resistance. Similarly, advanced tracking systems (guides) help prevent belt misalignment, which reduces material spillage, belt wear, and the need for frequent adjustments. By choosing durable, efficient accessories, mining operations can reduce energy consumption, prevent material losses, and streamline the transportation of materials from one point to another.
In addition to reducing energy consumption, high-quality accessories also reduce the overall strain on the conveyor system. For instance, high-quality drive pulleys that are well-maintained distribute power efficiently across the system, reducing unnecessary stress on the belt and other components. By improving the efficiency of the entire conveyor system, mining operations can enhance overall production rates and lower operational costs.
In conclusion, high-quality conveyor belt accessories are essential for the success of mining operations. These accessories play a pivotal role in ensuring continuous operation, reducing maintenance costs, and enhancing the overall efficiency of the material handling process. By selecting reliable, durable accessories, mining companies can not only improve productivity but also minimize unexpected downtime and extend the lifespan of their conveyor systems. Investing in quality conveyor belt accessories is a long-term investment that boosts both operational performance and bottom-line profitability.
Key Conveyor Belt Accessories for Mining: Boosting Efficiency and Safety
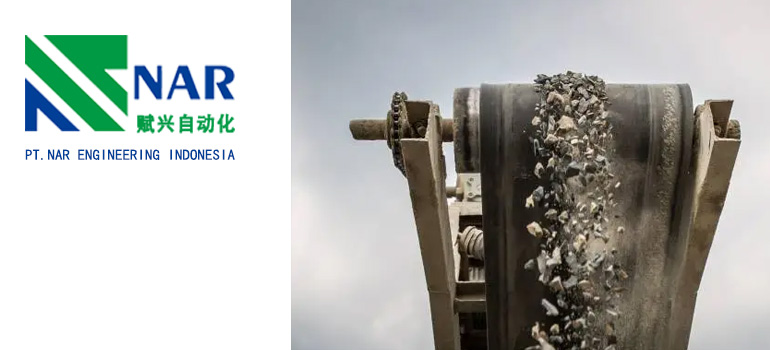
In mining operations, conveyor belt systems are integral to the transportation of materials over long distances, from the mine face to processing plants or stockpiles. To ensure that these systems run smoothly, safely, and efficiently, high-quality conveyor belt accessories are essential. These accessories not only enhance the operational efficiency of conveyor systems but also play a crucial role in preventing accidents, reducing wear, and ensuring optimal performance. Let’s dive into the key conveyor belt accessories for mining and how they contribute to safety and efficiency.
Conveyor Rollers: Enhancing Load Distribution and Reducing Wear
Conveyor rollers are among the most important accessories in any conveyor system. These cylindrical components are designed to support the weight of the conveyor belt and the material being transported. Rollers ensure smooth movement of the belt, reduce friction, and help maintain the alignment of the entire conveyor system.
- Efficient Load Distribution: Conveyor rollers help evenly distribute the load across the length of the belt, preventing excessive stress on any single part of the system. This leads to a more balanced operation and reduces the risk of premature wear or damage to the conveyor components.
- Reducing Belt Wear: High-quality rollers, especially those designed with advanced materials like polyurethane or stainless steel, can significantly reduce friction between the belt and roller, which in turn minimizes the wear and tear on the belt. This helps extend the lifespan of the conveyor system and lowers maintenance costs.
Without well-maintained or high-quality rollers, the belt can become misaligned, resulting in uneven wear and the potential for system failure, causing costly downtime and safety hazards.
Belt Cleaners: Maintaining Optimal Performance and Preventing Build-Up
Belt cleaners are vital accessories in any mining conveyor system. These devices are designed to remove material build-up that can accumulate on the belt surface, preventing the material from sticking to the belt and causing inefficiency. This accumulation can be particularly problematic when transporting sticky or wet materials such as ores or coal.
- Preventing Material Build-Up: Cleaners ensure that the belt remains free of debris, reducing the chances of material spillage and improving the overall efficiency of the conveyor system. Belt cleaners are typically installed on the return side of the conveyor belt and use either brushes or scraper blades to remove excess material.
- Enhancing Safety: A clean belt is less likely to cause accidents related to material spillage, especially in high-traffic or hazardous areas. Belt cleaners help keep the working environment safer by reducing the risk of slip-and-fall incidents and minimizing the chance of equipment malfunctions caused by material buildup.
Using belt cleaners that are suited to the specific materials being transported can make a significant difference in reducing maintenance time, improving system performance, and preventing safety hazards.
Skirtboards and Chutes: Improving Material Flow and Reducing Spillage
Skirtboards and chutes are additional accessories that ensure material is efficiently conveyed through the system without unnecessary loss or spillage. Skirtboards are flexible seals placed along the edges of the conveyor belt to prevent material from escaping during transport, while chutes guide the material from one conveyor to another or into a pile.
- Minimizing Spillage: Skirtboards help prevent spillage by maintaining a tight seal along the belt edges, ensuring that no material escapes. This is especially important in mining, where material loss can significantly affect productivity and increase operational costs.
- Optimizing Material Flow: Chutes ensure that the material is efficiently transferred from one conveyor system to the next, reducing the risk of blockages or bottlenecks in the material handling process. Properly designed chutes allow for smoother transitions, helping to maintain continuous flow and prevent jams.
Both skirtboards and chutes play a critical role in maintaining an efficient and tidy operation, reducing the environmental impact of material loss, and enhancing overall safety by keeping the work environment cleaner and less hazardous.
Tensioning Systems: Ensuring Proper Belt Tension and System Stability
Tensioning systems are designed to ensure that the conveyor belt is kept at the correct tension for optimal performance. A properly tensioned belt reduces the risk of slippage, premature wear, and system instability.
- Preventing Belt Slippage: Belt tensioning systems maintain the necessary force to keep the belt tightly in place, preventing slippage. When a belt is too loose, it may slip, causing inefficiency, excess wear, and potential system damage. On the other hand, if the belt is too tight, it can cause unnecessary strain on the motor and other components.
- Increasing System Longevity: A properly tensioned belt reduces wear and tear on the rollers, pulleys, and other critical components, which can extend the life of the entire conveyor system. Tensioning systems that are easily adjustable also make maintenance quicker and easier, saving time and money.
Conveyor Belt Guards and Safety Devices: Protecting Workers and Equipment
Safety is paramount in any mining operation, and conveyor belt accessories designed to protect workers from injury are essential. Conveyor belt guards, emergency stop devices, and safety pull cords are just a few of the accessories designed to enhance safety on the job site.
- Emergency Stop Systems: Emergency stop buttons or pull cords are critical safety devices that allow operators to quickly shut down the conveyor system in case of an emergency. These systems help minimize the risk of injury in the event of a malfunction or hazard.
- Conveyor Guards: Guards are used to enclose moving parts, such as pulleys, rollers, and gears, reducing the risk of workers coming into contact with dangerous moving components. By preventing accidental contact with these parts, conveyor guards significantly improve safety.
Implementing these safety accessories ensures that operators and workers are protected, reducing the likelihood of workplace injuries and ensuring compliance with health and safety regulations.
In mining operations, the role of conveyor belt accessories cannot be overstated. Key accessories such as rollers, belt cleaners, skirtboards, chutes, tensioning systems, and safety devices directly impact the efficiency, safety, and reliability of the entire conveyor system. By investing in high-quality accessories and ensuring proper installation and maintenance, mining operations can minimize downtime, prevent material loss, enhance system performance, and create a safer working environment for employees. Ultimately, these accessories contribute to smoother operations, higher productivity, and lower long-term costs — all essential elements for success in the competitive mining industry.
How to Select the Right Conveyor Belt Accessories for Your Mining Project
Selecting the right conveyor belt accessories is essential for optimizing the performance and safety of mining operations. Conveyor systems in the mining industry operate in challenging environments, often handling heavy loads, abrasive materials, and extreme weather conditions. As a result, choosing the appropriate accessories — such as rollers, cleaners, skirting, and tensioning systems — can have a significant impact on both the efficiency of the system and the longevity of the equipment. Here’s a guide to help you select the right conveyor belt accessories for your mining project.
Matching Accessories with Conveyor Belt Types and Specifications
The first step in selecting the right conveyor belt accessories is understanding the specifications of the conveyor belt itself. Different types of belts are designed to handle different materials, operating conditions, and loads. The accessories you choose must complement the type and size of your conveyor belt to ensure maximum efficiency.
- Belt Type and Load Capacity: The weight and type of material being transported affect the accessories required. For heavy materials like coal, ore, or gravel, you’ll need more robust rollers, tensioning systems, and belt cleaners to handle the increased load and wear.
- Belt Width and Speed: Larger, wider belts may require more rollers or extra tensioning components to support the belt’s width and prevent sagging. Similarly, belts running at high speeds need accessories that can handle higher friction and stress, such as specially designed rollers and higher-quality cleaners.
- Material Compatibility: Certain accessories are designed for specific materials. For instance, abrasive materials like sand and gravel may require heavy-duty rollers and higher-grade cleaners, while sticky materials like coal slurry may need specialized cleaning devices to prevent build-up on the belt.
By carefully matching your accessories to the belt type and operating conditions, you ensure that each component functions optimally, helping to maximize the performance of the entire system.
Considering Environmental Conditions When Choosing Accessories
Mining operations often take place in harsh environmental conditions, such as extreme temperatures, high humidity, or dusty, corrosive environments. The durability and functionality of the accessories you select should be based on the environmental challenges your system will face.
- Temperature and Humidity: If your mining project is located in a region with extreme temperatures, it’s important to select conveyor belt accessories that are resistant to both high and low temperatures. For example, corrosion-resistant rollers and belts are crucial in wet or humid conditions where rusting can be a concern. Similarly, accessories made from high-temperature-resistant materials are necessary in hot environments to prevent premature wear and failure.
- Corrosive Environments: For mining operations in areas with high levels of corrosive elements (such as salt or acid), it’s essential to use accessories made from corrosion-resistant materials like stainless steel or specially coated parts. This will prolong the life of the accessories and prevent breakdowns.
- Dusty and Abrasive Conditions: Dusty mining environments require accessories that can withstand abrasive materials. Rollers, pulleys, and cleaners made from wear-resistant materials will help minimize damage and reduce the need for frequent maintenance.
Choosing the right accessories based on environmental conditions ensures that your conveyor system operates smoothly, even in the harshest of mining environments, and that accessories last longer, reducing replacement costs.
Evaluating the Durability and Longevity of Conveyor Belt Accessories
Durability is a critical factor when selecting conveyor belt accessories, especially in mining applications where equipment is subjected to constant wear and tear. Choosing accessories with a longer lifespan reduces maintenance costs and minimizes the risk of unexpected downtime.
- Material Strength: Accessories should be made from high-quality, durable materials that can withstand the heavy loads and abrasive conditions common in mining operations. For instance, choosing high-strength steel for rollers, impact-resistant materials for skirting, and tough rubber for belt cleaners can help ensure longevity.
- Resistance to Wear and Tear: Accessories like rollers and pulleys must be able to handle continuous friction and contact with the belt. Look for accessories designed with advanced wear-resistant coatings or those made from materials that can handle abrasive materials without degrading quickly.
- Maintenance Needs: Consider accessories that are easy to maintain and repair. For example, modular rollers and tensioning systems that can be quickly replaced or adjusted can reduce the maintenance time and effort required during the system’s operation. Accessories that require minimal maintenance, like self-cleaning belt systems or automated tensioning mechanisms, can significantly improve operational efficiency.
When selecting durable accessories, consider the total cost of ownership, which includes maintenance, repairs, and replacements. High-quality, long-lasting accessories may have a higher initial cost, but they can provide substantial savings over the life of the system by reducing downtime and maintenance costs.
Cost-Effectiveness vs. Quality: Striking the Right Balance
While it may be tempting to choose the least expensive conveyor belt accessories to reduce upfront costs, it’s important to balance cost with quality. In mining operations, cheap accessories can lead to increased maintenance costs, shorter lifespans, and more frequent breakdowns, which may end up costing more in the long run.
- Long-Term Investment: High-quality accessories, while potentially more expensive initially, are a better investment for the future. They help reduce maintenance downtime, increase efficiency, and ultimately lead to cost savings by extending the lifespan of the entire conveyor system.
- Total Cost of Ownership: Consider the long-term costs associated with lower-quality accessories. These might include more frequent repairs, replacements, and increased labor costs for maintenance. On the other hand, investing in higher-quality, durable accessories can lead to reduced downtime and fewer repairs, making them more cost-effective in the long term.
By striking a balance between cost and quality, you can make an informed decision that ensures both budget control and optimal performance.
Consultation with Experts: Ensuring the Best Fit for Your Project
Selecting the right conveyor belt accessories can be complex, especially when considering the many different factors that can affect performance. Consulting with industry experts or accessory suppliers can help guide you through the selection process. They can provide insight into the best products for your specific mining project, taking into account factors like material type, operating environment, and performance expectations.
Working with suppliers who specialize in mining conveyor systems will ensure that you choose the best components for your project’s unique needs. They can offer advice on the latest advancements in conveyor belt accessories, helping you stay ahead of potential issues and ensuring optimal system performance.
Selecting the right conveyor belt accessories for your mining project is essential for maximizing operational efficiency, minimizing downtime, and ensuring long-term durability. By carefully matching accessories to your belt type, environmental conditions, and the specific needs of your operation, you can enhance the performance of your conveyor system and reduce costs over time. Always prioritize durability and quality, and don’t hesitate to consult with industry experts to make the most informed decisions for your project. By taking these steps, you ensure that your conveyor system will operate efficiently, safely, and cost-effectively for years to come.
Maintenance Best Practices for Conveyor Belt Accessories in Mining
In mining operations, conveyor belt systems are subject to continuous wear and tear, often under heavy loads and harsh environmental conditions. To maintain optimal performance and reduce downtime, regular maintenance of conveyor belt accessories is crucial. Accessories such as rollers, belt cleaners, skirting, and tensioning systems are critical components of the system, and keeping them in good condition ensures smooth material flow and improved safety. Below are best practices to help you effectively maintain these essential accessories in mining applications.
Regular Inspection: Preventing Equipment Failure and Reducing Costs
Regular inspection of conveyor belt accessories is the foundation of an effective maintenance program. Routine checks help identify early signs of wear, misalignment, or potential failure before they result in costly breakdowns or safety issues. Inspections should be done at intervals based on the level of system use, environmental factors, and accessory type.
- Check Rollers and Pulleys: Inspect rollers for wear, damage, or misalignment. Ensure that they are rotating freely and that they are not overloaded or showing signs of uneven wear. Misaligned or damaged rollers can cause the belt to mistrack, leading to more serious damage.
- Examine Belt Cleaners: Check for signs of wear or build-up on belt cleaners, especially in areas where sticky or abrasive materials are being transported. Ensure that the blades or brushes are intact and making contact with the belt. Ineffective cleaners can cause material accumulation, leading to inefficiencies and additional maintenance.
- Skirting and Chutes: Inspect skirtboards and chutes for wear or damage, as worn-out components can lead to spillage or inefficient material flow. Ensure that skirtboards are properly sealed to prevent material from escaping and causing environmental issues or operational delays.
By implementing a regular inspection schedule, you can catch small issues before they escalate, reducing the likelihood of unexpected downtime and costly repairs.
Lubrication and Cleaning: Reducing Friction and Preventing Build-up
Proper lubrication and cleaning are essential to keep conveyor belt accessories functioning smoothly and efficiently. Lubrication helps reduce friction between moving parts, such as rollers, pulleys, and tensioning systems, preventing premature wear. Regular cleaning removes debris and materials that may cause damage or inefficiencies.
- Lubricate Rollers and Bearings: Apply the appropriate lubricant to the rollers and bearings at regular intervals. Lubrication reduces friction, lowers the risk of wear, and ensures that the rollers rotate smoothly. Make sure to use the correct type of lubricant based on the operating conditions and temperature.
- Clean Belt Cleaners and Scrapers: Periodically clean belt cleaners to remove any build-up of material that can cause inefficiency. Use appropriate cleaning agents that are safe for the materials being transported and for the conveyor components. Be sure that scrapers and brushes are clear of obstructions to maintain their performance.
- Avoid Material Build-Up: Excessive build-up on accessories such as rollers, pulleys, and belt cleaners can increase friction and reduce their lifespan. Regularly clean these components to prevent the accumulation of material, particularly in environments where sticky substances are being transported.
Well-maintained lubrication and cleaning routines reduce the load on accessories and extend their service life, helping maintain the overall efficiency of the conveyor system.
Troubleshooting Common Issues with Conveyor Belt Accessories
Despite regular maintenance, certain issues may arise with conveyor belt accessories that require prompt attention. Identifying and troubleshooting common problems can prevent larger issues from developing and avoid unnecessary downtime.
- Roller Misalignment: Misaligned rollers can cause the belt to run off-track, leading to increased wear and potential system failure. If misalignment is detected, adjust the rollers or replace damaged ones. Ensure that all rollers are properly aligned and centered to avoid further issues.
- Excessive Vibration or Noise: Excessive vibration or unusual noise from the conveyor system often signals a problem with the rollers, pulleys, or bearings. Inspect these components for wear or damage and replace them if necessary. Vibration can also be a sign of an improperly tensioned belt, so check the tensioning system to ensure that the belt is correctly tensioned.
- Belt Slippage: If the belt is slipping or not operating at optimal efficiency, it may be due to inadequate tension or problems with the drive pulley. Check the tensioning system to ensure the belt is tight enough, and inspect the pulleys for wear or damage.
- Belt Cleaner Inefficiency: If the belt cleaner is not effectively removing material, it could be due to a worn-out scraper or a misadjusted cleaner. Inspect the cleaner’s blades or brushes and adjust their positioning. Ensure that they are properly aligned and in good working condition.
Identifying and addressing these issues promptly can help maintain the conveyor system’s efficiency and reduce long-term maintenance costs.
Replacing Worn or Damaged Components: Timely Replacement for Optimal Performance
Even with proper maintenance, certain conveyor belt accessories will eventually wear out and need to be replaced. Timely replacement of worn or damaged components prevents more serious problems and helps maintain system efficiency.
- Monitor Roller and Pulley Wear: Regularly monitor the condition of rollers and pulleys. If you notice significant wear, cracks, or other signs of damage, replace them before they cause further issues. A worn roller can lead to increased friction and potential damage to the belt, reducing the overall lifespan of the conveyor system.
- Belt Cleaner Blade Replacement: Belt cleaner blades wear out over time due to the continuous contact with the belt and materials. Replacing the blades when they become ineffective ensures that the belt remains clean, reducing the risk of material build-up and improving system efficiency.
- Tensioning System Checks: Ensure that the tensioning system is regularly adjusted and maintained. If components such as springs or tensioning bolts show signs of wear, replace them immediately to maintain proper belt tension and avoid operational issues.
By replacing components at the right time, you can prevent unexpected breakdowns and extend the overall lifespan of the conveyor belt system.
Keeping a Maintenance Log: Tracking Performance and Scheduling Maintenance
A well-maintained log of inspections, maintenance tasks, and component replacements is essential for tracking the health of your conveyor system. This log can help identify patterns of wear or issues, ensuring that maintenance is scheduled appropriately and that no component is overlooked.
- Documenting Inspections and Repairs: Record the dates of inspections, the condition of components, and any repairs made. This log helps track the performance of accessories and can be useful for identifying recurring issues that may need more focused attention.
- Scheduling Preventative Maintenance: Based on the log, create a preventative maintenance schedule that outlines when specific components need to be inspected, lubricated, or replaced. Having a clear plan in place ensures that maintenance tasks are completed on time, reducing the likelihood of unexpected failures.
A maintenance log helps ensure that your team remains proactive in caring for conveyor belt accessories, improving long-term efficiency and reducing the chances of operational disruptions.
Effective maintenance of conveyor belt accessories is essential for maintaining the smooth operation of mining systems. By performing regular inspections, keeping components clean and lubricated, troubleshooting common issues, and replacing worn parts in a timely manner, mining operations can maximize the efficiency and lifespan of their conveyor systems. Proper maintenance reduces downtime, lowers repair costs, and ensures a safer working environment for employees. Adopting a structured maintenance approach is key to optimizing conveyor system performance and boosting overall productivity in mining operations.