Summary:
Maximizing Performance: Essential Belt Conveyor Components Explained
Exploring the Role of Belt Conveyor Components
Importance of Each Component in Conveyor Performance
Critical Functions and Interactions of Belt Conveyor Components
Essential Components for Optimal Belt Conveyor Performance
Maximizing Efficiency Through Proper Maintenance and Upkeep
Innovations in Belt Conveyor Components and Technology
Selecting the Right Belt Conveyor Components for Your Application
Exploring the Role of Belt Conveyor Components
Let’s embark on a journey to explore the pivotal role played by each component within belt conveyor systems, illuminating their significance in ensuring seamless operation and optimal performance.
Rollers and Pulleys: The Silent Forces
Picture the rollers and pulleys as the unsung heroes quietly driving the conveyor forward. These components bear the weight of the conveyor belt and its cargo, ensuring smooth movement and proper alignment. From idler rollers supporting the belt’s weight to drive pulleys propelling it forward, each plays a vital role in maintaining momentum and minimizing frictional resistance.
Belts and Chains: The Conveyors’ Lifeline
Visualize belts and chains as the lifelines of conveyor systems, faithfully ferrying goods from one point to another. Whether it’s a sturdy rubber belt or a robust steel chain, selecting the appropriate conveyor medium is critical for reliable performance. Factors such as material type, load capacity, and environmental conditions dictate the choice, ensuring seamless operation and longevity.
Bearings and Bushings: Guardians of Smoothness
Behind every smooth rotation and seamless pivot lies the humble bearing and bushing, providing essential support and reducing friction within the conveyor system. These components enable the effortless movement of rollers, pulleys, and shafts, ensuring efficient power transmission and minimal wear and tear. Regular lubrication and maintenance are paramount to prolonging their lifespan and preventing downtime due to component failure.
As we delve deeper into the intricate workings of belt conveyor systems, we uncover the indispensable roles played by each component. Just as a symphony relies on each instrument to create harmony, so too does the conveyor system depend on the synergy of its components to achieve seamless operation and unparalleled performance.
Importance of Each Component in Conveyor Performance
Let’s delve into the significance of each component in driving the performance of a conveyor system, highlighting their unique roles in ensuring efficiency, reliability, and safety.
Rollers and Pulleys: Distributing Weight and Momentum
Rollers and pulleys are the workhorses of a conveyor system, responsible for supporting the weight of the conveyor belt and facilitating its movement. Idler rollers distribute the weight evenly across the belt, reducing friction and preventing misalignment, while drive pulleys provide the necessary traction to propel the belt forward. The smooth rotation of these components ensures consistent momentum and minimizes energy consumption, contributing to the overall efficiency of the system.
Belts and Chains: Transporting Goods with Precision
Belts and chains act as the carriers of the conveyor system, transporting goods from one point to another with precision and reliability. Belts made of rubber or synthetic materials offer flexibility and durability, making them ideal for conveying a wide range of products. Chains, on the other hand, provide strength and stability, making them suitable for heavy-duty applications. The selection of the appropriate conveyor medium depends on factors such as load capacity, speed, and environmental conditions, ensuring smooth and efficient material handling.
Bearings and Bushings: Reducing Friction and Wear
Bearings and bushings play a crucial role in minimizing friction and wear within the conveyor system, ensuring smooth operation and prolonging the lifespan of moving parts. Bearings support the rotating shafts of rollers and pulleys, allowing them to move freely with minimal resistance. Bushings provide a low-friction interface between stationary and moving components, reducing wear and preventing metal-to-metal contact. Proper lubrication and maintenance of these components are essential to prevent downtime and costly repairs, maintaining the performance and reliability of the conveyor system.
Frames and Supports: Providing Stability and Structural Integrity
Frames and supports form the backbone of the conveyor system, providing stability and structural integrity to withstand the forces exerted during operation. The frame supports the conveyor bed and provides a stable platform for mounting rollers, pulleys, and other components. Supports such as legs and brackets distribute the weight evenly and ensure proper alignment, preventing sagging or misalignment of the conveyor belt. The design and construction of these components are critical to the overall performance and safety of the conveyor system, providing a sturdy foundation for efficient material handling.
In summary, each component of a conveyor system plays a vital role in driving its performance and efficiency. From distributing weight and momentum to transporting goods with precision, reducing friction and wear, and providing stability and structural integrity, every element contributes to the smooth and reliable operation of the system. By understanding the importance of each component and ensuring proper maintenance and care, operators can maximize the performance and longevity of their conveyor systems, improving productivity and reducing downtime.
Critical Functions and Interactions of Belt Conveyor Components
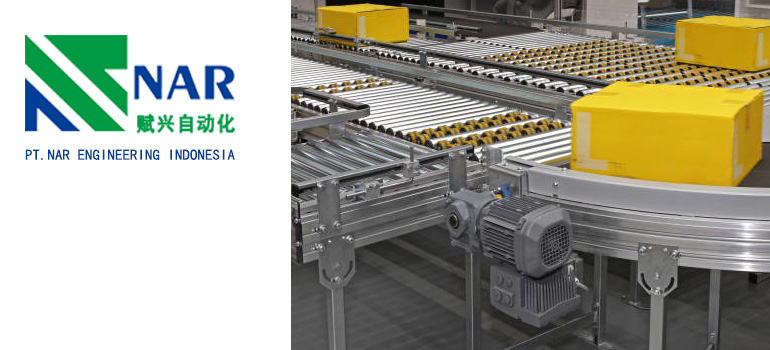
Let’s explore the critical functions and interactions of belt conveyor components, unveiling the intricate web of relationships that drive seamless operation and optimal performance.
Rollers and Pulleys: Foundation of Movement
Rollers and pulleys serve as the cornerstone of conveyor movement, orchestrating the smooth transition of goods along the conveyor path. Idler rollers distribute weight evenly across the belt, ensuring uniform tension and alignment, while drive pulleys provide the driving force necessary to propel the belt forward. This symbiotic relationship ensures continuous motion, minimizing frictional resistance and maximizing energy efficiency throughout the system.
Belts and Chains: The Conveyors of Material
Belts and chains act as the conveyors’ lifelines, faithfully transporting goods from one point to another with precision and reliability. Belts made of rubber or synthetic materials offer flexibility and durability, ideal for conveying a wide range of products. Chains, on the other hand, provide strength and stability, making them suitable for heavy-duty applications. This dynamic duo interacts seamlessly, ensuring efficient material handling while adapting to the specific requirements of each conveyor system.
Bearings and Bushings: The Guardians of Smooth Operation
Bearings and bushings form the backbone of smooth operation, providing essential support and reducing friction within the conveyor system. Bearings support the rotating shafts of rollers and pulleys, allowing them to move freely with minimal resistance. Bushings provide a low-friction interface between stationary and moving components, minimizing wear and preventing metal-to-metal contact. Together, they ensure reliable performance and longevity, enabling uninterrupted operation even under the most demanding conditions.
Frames and Supports: Stability and Structural Integrity
Frames and supports provide the foundation for stability and structural integrity, anchoring the conveyor system in place and supporting the weight of its components. The frame forms the skeleton of the conveyor, providing a stable platform for mounting rollers, pulleys, and other critical elements. Supports such as legs and brackets distribute weight evenly and maintain proper alignment, preventing sagging or misalignment of the conveyor belt. This robust framework ensures the smooth and efficient operation of the conveyor system, enhancing productivity and minimizing downtime.
Interactions and Synergies: The Key to Efficiency
The interactions between belt conveyor components are akin to a well-choreographed dance, where each element plays a critical role in ensuring seamless operation and optimal performance. Rollers and pulleys provide the foundation for movement, while belts and chains transport goods with precision. Bearings and bushings ensure smooth operation, while frames and supports provide stability and structural integrity. Together, they form a cohesive unit that maximizes efficiency, reliability, and safety, driving productivity and profitability across industries.
In summary, the critical functions and interactions of belt conveyor components underscore the importance of a holistic approach to system design and maintenance. By understanding the roles and relationships between each element, operators can optimize performance, minimize downtime, and ensure the smooth and efficient operation of their conveyor systems, enabling them to meet the ever-evolving demands of modern industry.
Essential Components for Optimal Belt Conveyor Performance
Rollers and Pulleys: Driving Momentum
Rollers and pulleys form the backbone of conveyor movement, bearing the weight of the conveyor belt and facilitating its motion. Idler rollers distribute the weight evenly, maintaining tension and alignment, while drive pulleys provide the driving force necessary to propel the belt forward. Together, they ensure continuous movement, minimizing frictional resistance and maximizing energy efficiency throughout the system.
Belts and Chains: Carriers of Material
Belts and chains act as the carriers of the conveyor system, transporting goods from one point to another with precision and reliability. Belts, made from rubber or synthetic materials, offer flexibility and durability, ideal for conveying a wide range of products. Chains provide strength and stability, making them suitable for heavy-duty applications. Their proper selection ensures efficient material handling, adapting to the specific requirements of each conveyor system.
Bearings and Bushings: Supporting Smooth Operation
Bearings and bushings play a crucial role in reducing friction and supporting smooth operation within the conveyor system. Bearings support the rotating shafts of rollers and pulleys, allowing them to move freely with minimal resistance. Bushings provide a low-friction interface between stationary and moving components, minimizing wear and ensuring longevity. Their proper lubrication and maintenance are essential to prevent downtime and maintain reliable performance.
Frames and Supports: Providing Stability
Frames and supports provide the structural foundation for stability and integrity within the conveyor system. The frame acts as the framework, supporting the conveyor bed and providing a stable platform for mounting rollers, pulleys, and other critical components. Supports such as legs and brackets distribute weight evenly, maintaining proper alignment and preventing sagging or misalignment of the conveyor belt. Their robust design ensures the smooth and efficient operation of the system, enhancing productivity and minimizing downtime.
Interplay and Optimization: Maximizing Efficiency
The interplay between these essential components is crucial for achieving optimal conveyor performance. Rollers and pulleys drive momentum, belts and chains carry the load, bearings and bushings support smooth operation, and frames and supports provide stability. Together, they form a cohesive system that maximizes efficiency, reliability, and safety, enabling the conveyor to meet the demands of modern industry.
In summary, the essential components of a belt conveyor system work in harmony to ensure optimal performance, efficiency, and reliability. By understanding their roles and interactions, operators can optimize system design, maintenance, and operation, ensuring smooth material handling and maximizing productivity across industries.
Maximizing Efficiency Through Proper Maintenance and Upkeep
Regular Inspection and Monitoring: Keeping a Watchful Eye
Regular inspection and monitoring are the cornerstones of effective maintenance practices for belt conveyor systems. Conducting routine checks on components such as rollers, pulleys, belts, and bearings help identify potential issues before they escalate into costly failures. Utilizing advanced monitoring technologies, such as vibration analysis and thermal imaging, allows for early detection of abnormalities, enabling timely intervention and minimizing downtime.
Lubrication and Cleaning: Preserving Smooth Operation
Proper lubrication and cleaning are essential for preserving the smooth operation of conveyor components and extending their service life. Applying the appropriate lubricants to bearings, bushings, and moving parts reduces friction and wear, preventing premature failure and ensuring optimal performance. Regular cleaning of belts and pulleys removes debris and buildup, preventing slippage and reducing the risk of damage to the system.
Alignment and Tensioning: Maintaining Optimal Conditions
Ensuring proper alignment and tensioning of belts is critical for maintaining optimal conveyor performance. Misalignment and improper tension can lead to uneven wear, increased friction, and premature failure of components. Regularly checking and adjusting belt alignment and tensioning mechanisms helps prevent tracking issues and ensures consistent operation throughout the system.
Replacement of Worn Components: Preventing Catastrophic Failures
Timely replacement of worn or damaged components is essential for preventing catastrophic failures and minimizing downtime. Monitoring wear indicators, such as belt thickness and roller diameter, helps identify components that are approaching the end of their service life. Proactively replacing these components before they fail prevents costly unplanned shutdowns and ensures the continued reliability of the conveyor system.
Training and Education: Empowering Maintenance Personnel
Investing in training and education for maintenance personnel is crucial for empowering them with the knowledge and skills needed to perform effective maintenance tasks. Providing comprehensive training on inspection techniques, troubleshooting methods, and safety protocols ensures that maintenance teams are equipped to identify and address issues promptly, minimizing downtime and maximizing efficiency.
In summary, maximizing efficiency through proper maintenance and upkeep involves a proactive approach to monitoring, lubrication, alignment, replacement, and training. By implementing a robust maintenance strategy and adhering to best practices, operators can prolong the lifespan of their belt conveyor systems, optimize performance, and ensure the smooth and reliable operation of their facilities.
Innovations in Belt Conveyor Components and Technology
Advanced Materials and Coatings: Enhancing Durability and Performance
Innovations in materials science have led to the development of advanced materials and coatings that enhance the durability and performance of belt conveyor components. High-performance polymers, such as polyurethane and composite materials, offer superior wear resistance and reduce maintenance requirements. Innovative coatings, such as ceramic and nano-coatings, provide enhanced protection against abrasion, corrosion, and chemical damage, prolonging the lifespan of conveyor components and reducing downtime.
Smart Sensors and Monitoring Systems: Enabling Predictive Maintenance
The integration of smart sensors and monitoring systems into belt conveyor components enables predictive maintenance, allowing operators to detect issues before they escalate into costly failures. Sensors embedded in rollers, bearings, and belts continuously monitor parameters such as temperature, vibration, and alignment, providing real-time data on component health and performance. Advanced analytics and predictive algorithms analyze this data to predict potential failures and recommend proactive maintenance actions, minimizing downtime and optimizing system reliability.
Energy-Efficient Drive Systems: Minimizing Environmental Impact
Energy-efficient drive systems are transforming belt conveyor technology, minimizing environmental impact and reducing operating costs. Variable frequency drives (VFDs), regenerative braking systems, and intelligent control algorithms optimize motor speed and power consumption based on load demand, reducing energy consumption and carbon emissions. Innovative energy recovery systems capture and store excess kinetic energy during braking, which can be reused to power other conveyor components, further enhancing efficiency and sustainability.
Modular Design and Customization: Tailoring Solutions to Specific Needs
Modular design and customization options are empowering operators to tailor belt conveyor systems to their specific needs and applications. Modular components, such as interchangeable rollers, pulleys, and belts, enable quick and easy reconfiguration of conveyor layouts to accommodate changing production requirements. Customization options, such as adjustable frames, variable speed drives, and automated sorting systems, allow operators to optimize system performance and throughput, maximizing productivity and flexibility.
Integration with Industry 4.0 Technologies: Driving Automation and Connectivity
Integration with Industry 4.0 technologies, such as Internet of Things (IoT), cloud computing, and artificial intelligence (AI), is driving automation and connectivity in belt conveyor systems. Connected conveyor components communicate seamlessly with other equipment and systems, enabling real-time data exchange and centralized control. AI-driven predictive maintenance algorithms analyze vast amounts of data to optimize system performance, predict failures, and schedule maintenance activities, maximizing uptime and efficiency.
In summary, innovations in belt conveyor components and technology are reshaping the landscape of material handling systems, driving efficiency, reliability, and sustainability. By leveraging advanced materials, smart sensors, energy-efficient drive systems, modular design, and Industry 4.0 technologies, operators can optimize performance, minimize downtime, and adapt to evolving production requirements, ensuring the continued competitiveness and success of their operations.
Selecting the Right Belt Conveyor Components for Your Application
Selecting the right belt conveyor components for your application is crucial for ensuring optimal performance, reliability, and efficiency. Let’s explore key considerations and guidelines to help you make informed decisions:
Define Your Application Requirements
Begin by clearly defining your application requirements, including throughput capacity, material characteristics, operating environment, and safety regulations. Understanding these factors will guide your selection of components that best meet your specific needs.
Identify Critical Components
Identify the critical components of your belt conveyor system, such as rollers, pulleys, belts, bearings, and drives, that directly impact performance and reliability. Prioritize the selection and maintenance of these components to ensure the overall efficiency and longevity of the system.
Evaluate Material Compatibility
Consider the material compatibility of conveyor components with the materials being transported. Select belts, rollers, and coatings that are resistant to abrasion, corrosion, and chemical exposure to ensure longevity and prevent material contamination.
Assess Load Capacity and Operating Conditions
Evaluate the load capacity and operating conditions of your application, including factors such as load weight, speed, temperature, and moisture levels. Choose components that can handle the expected loads and environmental conditions without compromising performance or safety.
Consider Maintenance Requirements
Take into account the maintenance requirements of different conveyor components, including lubrication, cleaning, and replacement intervals. Opt for components that are easy to maintain and service to minimize downtime and reduce overall operating costs.
Optimize Energy Efficiency
Select energy-efficient drive systems and components, such as variable frequency drives (VFDs) and regenerative braking systems, to minimize energy consumption and reduce operating costs. Choose components with adjustable speed and power settings to optimize energy usage based on load demand.
Ensure Compatibility and Interoperability
Ensure compatibility and interoperability between different conveyor components and systems to facilitate seamless integration and operation. Choose components from reputable manufacturers that adhere to industry standards and specifications to avoid compatibility issues and ensure system reliability.
Seek Expert Advice and Support
Seek expert advice and support from conveyor system manufacturers, engineers, and suppliers to help you navigate the selection process. They can provide valuable insights, recommendations, and technical assistance to ensure you choose the right components for your application.
By following these guidelines and considerations, you can effectively select the right belt conveyor components for your application, optimizing performance, reliability, and efficiency while minimizing downtime and operating costs.