Summary:
Enhancing Workplace Safety: Top 10 Conveyor Belt Safety Measures
Routine Maintenance and Inspection
Training and Education for Personnel
Hazard Identification and Risk Mitigation
Emergency Preparedness and Response
Continuous Improvement and Feedback Mechanisms
Routine Maintenance and Inspection
Regular maintenance and inspection routines are critical for the safe and efficient operation of conveyor belts. By proactively addressing potential issues and ensuring that all components are in good working condition, organizations can minimize the risk of accidents, extend equipment lifespan, and maintain productivity levels.
Importance of Regular Inspections: Ensuring Conveyor Belt Safety
Regular inspections serve as proactive measures to identify and address potential hazards or malfunctions before they escalate into safety incidents or equipment failures. By conducting thorough inspections at scheduled intervals, maintenance personnel can detect signs of wear, damage, or misalignment and take corrective actions promptly.
Key Components to Check: Rollers, Idlers, and Belt Alignment
During routine inspections, special attention should be given to critical components such as rollers, idlers, and belt alignment. Rollers and idlers play a crucial role in supporting the conveyor belt and facilitating smooth material transport. Any signs of wear, corrosion, or misalignment should be promptly addressed to prevent premature failure and ensure safe operation.
Implementing a Maintenance Schedule: Preventive Measures for Conveyor Safety
Establishing a structured maintenance schedule is essential for ensuring that routine inspections are conducted consistently and efficiently. Maintenance tasks should be scheduled based on manufacturer recommendations, industry best practices, and operational demands. By adhering to a predefined maintenance schedule, organizations can prevent unexpected downtime, optimize equipment performance, and promote workplace safety.
Incorporating routine maintenance and inspection practices into operational workflows is key to fostering a culture of safety and reliability in conveyor belt systems. By investing time and resources in proactive maintenance measures, organizations can minimize risks, enhance productivity, and create a safer working environment for all employees involved in conveyor operations.
Training and Education for Personnel
Proper training and education ensure that personnel are equipped with the knowledge and skills necessary to operate and maintain conveyor belts safely. By providing comprehensive training programs, organizations can empower their employees to identify potential hazards, adhere to safety protocols, and respond effectively to emergencies.
Conveyor Safety Training: Essential Knowledge and Skills
Conveyor safety training should cover a range of topics, including equipment operation, hazard recognition, emergency procedures, and personal protective equipment (PPE) usage. Employees should be educated on the safe operation of conveyor belts, including startup/shutdown procedures, material handling techniques, and safe work practices around moving machinery.
Safety Procedures and Protocols: Handling Conveyor Equipment Safely
Training programs should emphasize the importance of following established safety procedures and protocols when working with conveyor equipment. This includes procedures for lockout/tagout (LOTO), confined space entry, and emergency stops. Employees should be trained to identify potential hazards, such as pinch points, entanglement risks, and falling objects, and to take appropriate precautions to mitigate these risks.
Continuous Education: Keeping Workers Informed about Conveyor Safety Standards
Safety training should be an ongoing process, with regular updates and refresher courses to reinforce learning and address evolving safety standards. Employees should be kept informed about changes in safety regulations, equipment upgrades, and best practices through regular safety meetings, toolbox talks, and training sessions. This ensures that workers remain vigilant and proactive in maintaining a safe work environment.
By investing in comprehensive training and education programs for personnel, organizations can mitigate risks, reduce accidents, and promote a culture of safety in the workplace. Empowering employees with the knowledge and skills to identify and address potential hazards ensures that conveyor belt operations are conducted safely and efficiently, ultimately contributing to the overall success of the organization.
Hazard Identification and Risk Mitigation
Conveyor belt systems pose various hazards in the workplace, ranging from entanglement risks to material spillage. Identifying these hazards and implementing appropriate risk mitigation measures are essential for preventing accidents, minimizing injuries, and ensuring a safe working environment for all personnel.
Conducting Risk Assessments: Identifying Potential Hazards
Conducting comprehensive risk assessments is the first step in hazard identification and risk mitigation. Risk assessments involve systematically evaluating conveyor belt operations to identify potential hazards, such as pinch points, entanglement risks, falling objects, and material spillage. By understanding the inherent risks associated with conveyor belt systems, organizations can develop targeted risk mitigation strategies to minimize potential harm.
Addressing Common Risks: Pinch Points, Entanglement, and Falling Objects
Once hazards have been identified, organizations must implement measures to mitigate these risks effectively. Common risk mitigation strategies include installing guards and barriers to prevent access to pinch points, implementing safe work procedures to minimize the risk of entanglement, and securing loads to prevent falling objects. By addressing these common risks proactively, organizations can significantly reduce the likelihood of accidents and injuries in the workplace.
Implementing Control Measures: Minimizing Risks for Enhanced Conveyor Safety
In addition to physical safeguards, organizations should implement administrative controls and safe work practices to further minimize risks associated with conveyor belt operations. This may include establishing clear signage and warning systems, providing adequate training and supervision for personnel, and implementing regular inspections and maintenance routines to ensure equipment integrity. By integrating multiple layers of control measures, organizations can create a comprehensive safety framework that effectively mitigates risks and promotes a culture of safety in the workplace.
By prioritizing hazard identification and risk mitigation, organizations can create a safer working environment for personnel and minimize the potential for accidents and injuries associated with conveyor belt operations. Regular risk assessments, targeted risk mitigation measures, and ongoing monitoring and evaluation are essential components of an effective conveyor belt safety program.
Emergency Preparedness and Response
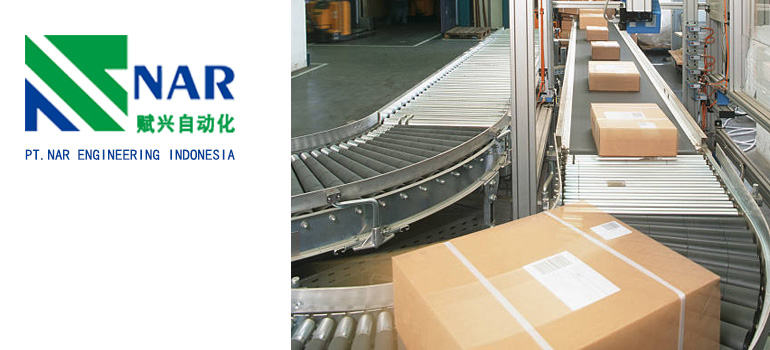
Despite proactive safety measures, emergencies can still occur in conveyor belt operations. Being prepared to respond effectively to emergencies is essential for minimizing the impact on personnel and property and preventing escalation of the situation.
Developing Emergency Response Plans: Quick Actions in Case of Accidents
Developing comprehensive emergency response plans is essential for ensuring a swift and coordinated response to accidents or incidents involving conveyor belt systems. These plans should outline specific procedures for responding to emergencies, including roles and responsibilities, communication protocols, evacuation procedures, and emergency shutdown procedures. By establishing clear guidelines and protocols, organizations can minimize confusion and ensure that personnel respond promptly and effectively in emergency situations.
First Aid Training: Equipping Workers for Prompt Medical Assistance
Providing first aid training to personnel is essential for ensuring prompt medical assistance in the event of injuries or medical emergencies related to conveyor belt operations. Employees should be trained in basic first aid techniques, such as wound care, CPR, and use of automated external defibrillators (AEDs). Additionally, designated personnel should be trained as first aid responders to provide immediate assistance until professional medical help arrives. By equipping workers with the skills and knowledge to administer first aid, organizations can improve outcomes for injured personnel and minimize the severity of injuries.
Mock Drills and Exercises: Testing Emergency Procedures for Conveyor Belt Safety
Regularly conducting mock drills and emergency response exercises is essential for testing the effectiveness of emergency procedures and identifying areas for improvement. These drills should simulate various emergency scenarios, such as conveyor belt fires, entrapments, or chemical spills, and involve all relevant personnel, including operators, maintenance staff, and emergency responders. By practicing emergency response procedures in a controlled environment, organizations can enhance preparedness, build confidence, and ensure a coordinated response in real-life emergencies.
By prioritizing emergency preparedness and response, organizations can minimize the impact of emergencies on personnel and property and ensure a safe working environment for all employees involved in conveyor belt operations. Comprehensive emergency response plans, first aid training, and regular drills are essential components of an effective conveyor belt safety program.
Continuous Improvement and Feedback Mechanisms
Continuous improvement involves regularly evaluating existing processes, identifying areas for enhancement, and implementing changes to achieve better outcomes. By soliciting feedback from personnel and stakeholders, organizations can gather valuable insights and drive ongoing improvements in conveyor belt safety.
Encouraging Worker Feedback: Identifying Safety Gaps and Concerns
Employees who work directly with conveyor belt systems are often well-positioned to identify potential safety hazards or inefficiencies in existing processes. Encouraging workers to provide feedback on their observations, concerns, and suggestions for improvement creates a culture of safety and fosters employee engagement. By actively seeking input from frontline workers, organizations can identify safety gaps, address underlying issues, and implement targeted improvements to enhance conveyor belt safety.
Analyzing Incident Reports: Learning from Past Mistakes for Future Improvements
Analyzing incident reports and near-miss incidents is essential for identifying root causes and underlying factors contributing to safety incidents. By conducting thorough investigations and analyzing trends in incident data, organizations can gain valuable insights into recurring issues and implement corrective actions to prevent future occurrences. Learning from past mistakes and near-miss incidents allows organizations to proactively address potential safety hazards and continuously improve conveyor belt safety protocols and procedures.
Implementing Changes: Incorporating Suggestions for Enhanced Conveyor Safety
Feedback gathered from workers and incident reports should inform decision-making processes and drive meaningful changes to enhance conveyor belt safety. Implementing recommendations for safety improvements, such as updating safety protocols, providing additional training, or investing in new safety equipment, demonstrates a commitment to prioritizing safety in the workplace. By incorporating suggestions from personnel and stakeholders, organizations can create safer work environments, improve operational efficiency, and foster a culture of continuous improvement in conveyor belt safety.
By prioritizing continuous improvement and feedback mechanisms, organizations can identify opportunities for enhancing conveyor belt safety, drive meaningful changes, and create safer work environments for all personnel involved in conveyor belt operations. Regularly soliciting feedback, analyzing incident data, and implementing targeted improvements are essential components of an effective conveyor belt safety program.