Summary:
Driving Productivity: Innovations in Conveyor Belt Assembly Technology
The Evolution of Conveyor Belt Assembly Technology
Advanced Technologies Driving Efficiency in Conveyor Belt Assembly
Enhancing Productivity Through Conveyor Belt Assembly Optimization
Future Trends and Innovations in Conveyor Belt Assembly
The Evolution of Conveyor Belt Assembly Technology
The evolution of conveyor belt assembly technology is a fascinating journey marked by significant advancements and innovations. Let’s delve into the historical overview of conveyor belt assembly technology and explore key milestones that have shaped its development:
Historical Overview of Conveyor Belt Assembly: The concept of conveyor belt assembly traces back to ancient civilizations, where primitive conveyance systems were used to transport goods and materials over short distances. However, it wasn’t until the Industrial Revolution in the 18th century that conveyor belt technology began to take shape. The invention of the modern conveyor belt by Richard Sutcliffe in 1905 revolutionized material handling and paved the way for mass production in various industries.
Key Milestones in Conveyor Belt Assembly Innovation:
Introduction of Automated Assembly Lines: The introduction of automated assembly lines in the early 20th century marked a significant milestone in conveyor belt technology. Henry Ford’s implementation of the assembly line at the Ford Motor Company in 1913 revolutionized manufacturing processes, allowing for faster, more efficient production of automobiles. Conveyor belts played a crucial role in the movement of components along the assembly line, enabling continuous flow production and mass customization.
Advancements in Conveyor Belt Materials and Design: Throughout the 20th century, advancements in materials science and engineering led to the development of more durable and efficient conveyor belts. The introduction of synthetic materials such as nylon, polyester, and rubber significantly improved the strength, flexibility, and longevity of conveyor belts. Innovations in belt design, including modular belts, cleated belts, and timing belts, expanded the versatility and applicability of conveyor systems across various industries.
Integration of Robotics and Automation: In recent decades, the integration of robotics and automation has transformed conveyor belt assembly technology. Automated guided vehicles (AGVs), robotic arms, and vision systems are increasingly used to enhance conveyor belt assembly processes. Robotics enable precise handling, positioning, and manipulation of parts, reducing human intervention and improving efficiency. Advanced control systems and sensors enable seamless integration of robotics with conveyor systems, enabling real-time monitoring and optimization of assembly operations.
As we look to the future, the evolution of conveyor belt assembly technology continues unabated. Emerging technologies such as artificial intelligence, machine learning, and the Internet of Things (IoT) are poised to further revolutionize conveyor belt assembly processes. By embracing innovation and leveraging advanced technologies, manufacturers can drive productivity, efficiency, and competitiveness in conveyor belt assembly and beyond.
Advanced Technologies Driving Efficiency in Conveyor Belt Assembly
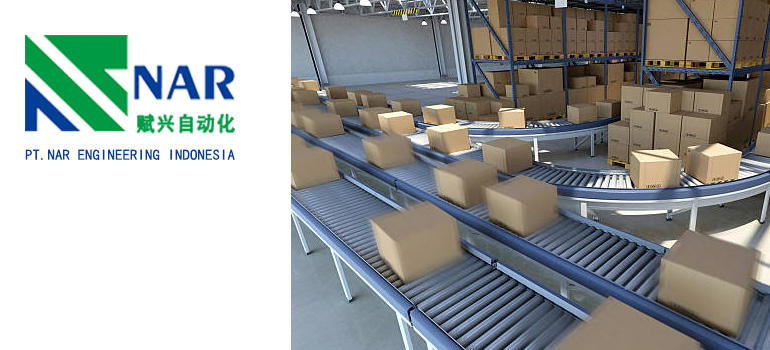
In today’s rapidly evolving manufacturing landscape, advanced technologies are playing a pivotal role in driving efficiency and innovation in conveyor belt assembly processes. Let’s explore how these cutting-edge technologies are revolutionizing conveyor belt assembly:
Automated Conveyor Belt Tracking Systems: One of the most significant advancements in conveyor belt assembly technology is the implementation of automated conveyor belt tracking systems. These sophisticated systems utilize sensors and controllers to continuously monitor and adjust the position and alignment of conveyor belts in real-time. By eliminating the need for manual adjustments, automated tracking systems improve assembly efficiency, reduce downtime, and minimize product damage caused by misalignment.
Conveyor Belt Splicing and Repair Innovations: Innovations in conveyor belt splicing and repair techniques have also contributed to increased efficiency and reliability in assembly processes. Traditional methods of splicing and repairing conveyor belts often require lengthy downtime and specialized skills. However, new advancements in splicing materials and techniques, such as vulcanization and mechanical fastening systems, have significantly reduced repair times and improved the longevity of conveyor belts. These innovations enable faster turnaround times and minimize disruptions in assembly operations.
Impact of Predictive Maintenance on Assembly Efficiency: Predictive maintenance technologies are transforming the way conveyor belt assembly systems are maintained and serviced. By leveraging sensors and data analytics, predictive maintenance systems can monitor the condition of conveyor belts in real-time and predict potential failures before they occur. This proactive approach to maintenance minimizes unplanned downtime, reduces maintenance costs, and extends the lifespan of conveyor belts. By optimizing maintenance schedules and prioritizing critical repairs, predictive maintenance improves overall efficiency and reliability in assembly processes.
Integration of Robotics and Automation: The integration of robotics and automation technologies has revolutionized conveyor belt assembly processes, enabling higher levels of precision, speed, and flexibility. Robotic arms, automated guided vehicles (AGVs), and vision systems are increasingly being deployed to handle tasks such as part picking, sorting, and inspection. Robotics enable seamless integration with conveyor systems, allowing for greater customization, adaptability, and scalability in assembly operations. By automating repetitive tasks and reducing manual labor, robotics enhance efficiency and productivity in conveyor belt assembly.
Optimization Through Data Analytics and AI: Data analytics and artificial intelligence (AI) are being used to optimize conveyor belt assembly processes through real-time monitoring and analysis of operational data. AI-powered algorithms can analyze vast amounts of data generated by conveyor systems to identify patterns, anomalies, and opportunities for optimization. By providing insights into factors such as throughput, downtime, and energy consumption, AI-driven analytics enable manufacturers to make data-driven decisions and continuously improve assembly efficiency. Predictive analytics also enable proactive identification of potential issues, allowing for preventive measures to be taken before problems arise.
In conclusion, advanced technologies such as automated tracking systems, innovative splicing and repair techniques, predictive maintenance, robotics, and AI-driven analytics are driving significant improvements in efficiency, reliability, and productivity in conveyor belt assembly processes. By embracing these technologies, manufacturers can optimize assembly operations, minimize downtime, and gain a competitive edge in today’s dynamic manufacturing environment.
Enhancing Productivity Through Conveyor Belt Assembly Optimization
Enhancing productivity through conveyor belt assembly optimization is a key objective for manufacturing companies seeking to streamline their operations and maximize efficiency. Let’s explore some strategies and best practices for achieving this goal:
Optimized Layout and Configuration for Assembly Lines: Efficient layout and configuration of conveyor belt assembly lines are critical for maximizing productivity. By strategically positioning conveyor belts and workstations, manufacturers can minimize material handling, reduce bottlenecks, and optimize workflow. Utilizing concepts such as lean manufacturing principles and value stream mapping helps identify opportunities for layout optimization and process improvement, leading to increased throughput and productivity.
Considerations for Conveyor Belt Placement and Routing:
Analyzing product flow and material handling requirements to determine the most efficient layout and configuration of conveyor belts.
Minimizing unnecessary stops, turns, and crossovers to streamline material flow and reduce cycle times.
Implementing straight-line conveyors, curves, and merges where appropriate to optimize product movement and reduce congestion.
Integration of Sorting and Packaging Systems:
Integrating sorting and packaging systems with conveyor belt assembly lines to streamline downstream processes and improve overall efficiency.
Implementing automated sorting technologies, such as barcode scanners and RFID systems, to accurately identify and divert products to their designated destinations.
Utilizing automated packaging solutions, such as robotic palletizers and case packers, to optimize packaging operations and reduce manual labor.
Utilization of Lean Manufacturing Principles:
Applying lean manufacturing principles, such as 5S, Kaizen, and just-in-time (JIT) production, to eliminate waste, improve workflow, and optimize resource utilization.
Implementing visual management techniques, such as kanban systems and visual work instructions, to enhance communication, standardization, and accountability on the assembly line.
Empowering employees to identify and address inefficiencies through continuous improvement initiatives and cross-functional collaboration.
By optimizing layout and configuration, integrating sorting and packaging systems, and embracing lean manufacturing principles, manufacturers can enhance productivity and efficiency in conveyor belt assembly operations. These strategies enable organizations to streamline material flow, minimize waste, and maximize throughput, ultimately driving competitive advantage and business success.
Future Trends and Innovations in Conveyor Belt Assembly
Looking ahead, the future of conveyor belt assembly holds exciting possibilities as manufacturers continue to embrace innovation and technology. Let’s explore some emerging trends and innovations that are poised to reshape conveyor belt assembly processes:
Emerging Technologies Reshaping Conveyor Belt Assembly:
Integration of Artificial Intelligence (AI) and Machine Learning: AI and machine learning technologies are revolutionizing conveyor belt assembly by enabling predictive maintenance, optimizing performance, and enhancing automation. AI-powered algorithms analyze real-time data from conveyor systems to predict equipment failures, optimize conveyor settings, and identify opportunities for process improvement. Machine learning algorithms continuously learn from data patterns to refine assembly processes and adapt to changing production requirements.
Advancements in Conveyor Belt Material Science: Innovations in materials science are leading to the development of stronger, lighter, and more durable conveyor belts. Advanced materials such as carbon fiber composites, nano-coatings, and self-healing polymers offer superior performance, longevity, and resistance to wear and tear. These next-generation materials enable conveyor belts to withstand harsh operating conditions, reduce maintenance requirements, and extend service life, thereby improving reliability and efficiency in assembly operations.
Integration of IoT and Industry 4.0 Technologies: The Internet of Things (IoT) and Industry 4.0 technologies are transforming conveyor belt assembly into interconnected, intelligent systems. IoT sensors embedded in conveyor belts and equipment collect data on temperature, vibration, and performance metrics in real-time. This data is then transmitted to cloud-based platforms for analysis, enabling remote monitoring, predictive maintenance, and optimization of assembly processes. Industry 4.0 concepts such as cyber-physical systems and digital twins enable virtual modeling and simulation of conveyor belt assembly operations, facilitating predictive analysis and scenario planning.
Development of Flexible and Modular Conveyor Systems: Flexible and modular conveyor systems are gaining popularity due to their versatility and scalability in assembly operations. These systems feature interchangeable modules, adjustable configurations, and reconfigurable layouts that enable rapid adaptation to changing production needs. By incorporating flexible conveyor technologies, manufacturers can optimize space utilization, accommodate product variations, and enhance agility in assembly processes.
Advancements in Robotics and Automation: Robotics and automation technologies continue to play a pivotal role in conveyor belt assembly, enabling higher levels of precision, speed, and flexibility. Collaborative robots (cobots) work alongside human operators to handle tasks such as part handling, assembly, and inspection. Advanced vision systems and artificial intelligence algorithms enable robots to identify and manipulate parts with greater accuracy and efficiency. Integration of robotics and automation enhances productivity, improves quality, and reduces labor costs in conveyor belt assembly operations.
As these trends and innovations continue to evolve, conveyor belt assembly will undergo transformative changes, driving efficiency, flexibility, and sustainability in manufacturing processes. By embracing emerging technologies and adopting a forward-thinking approach, manufacturers can stay ahead of the curve and unlock new opportunities for growth and competitiveness in the future of conveyor belt assembly.