Summary:
Conveyor Belt Pulleys: Essential Components for Efficient Material Handling
What Are Conveyor Belt Pulleys
Why Conveyor Belt Pulleys Are Essential for Material Handling Efficiency
Types of Conveyor Belt Pulleys and Their Specific Functions
Conveyor Belt Pulleys and Their Role in System Efficiency and Longevity
Selecting and Installing Conveyor Belt Pulleys for Your System
What Are Conveyor Belt Pulleys?
Conveyor belt pulleys are essential components in any material handling system that uses a conveyor belt. These pulleys serve as the driving force behind the movement of the conveyor belt, enabling it to transport goods and materials efficiently. Whether you’re working in a warehouse, manufacturing facility, or mining operation, understanding the role of conveyor belt pulleys is crucial to optimizing your system’s performance and minimizing downtime.
At their core, conveyor belt pulleys are cylindrical wheels that the conveyor belt wraps around. They are strategically positioned along the conveyor to drive, support, and guide the belt as it moves. Without pulleys, a conveyor belt wouldn’t be able to move efficiently or carry loads over long distances. But the importance of conveyor belt pulleys goes far beyond just providing the motion—they also contribute to system stability, reduce wear on the belt, and ensure the proper alignment of the entire conveyor system.
Basic Function of Conveyor Belt Pulleys
The primary function of conveyor belt pulleys is to transfer mechanical energy from the motor to the conveyor belt, allowing it to move and transport materials.
- Head pulleys, located at the discharge end of the conveyor, typically drive the belt. These pulleys are connected to the motor or drive system and provide the force needed to move the belt forward.
- Tail pulleys, found at the opposite end of the conveyor, serve to return the belt to the beginning of the system, maintaining tension and stability in the belt loop.
Beyond this, conveyor belt pulleys also help with belt alignment. They ensure that the belt stays centered and doesn’t drift off the path, which could cause wear or even belt failure. By maintaining proper alignment, pulleys reduce the risk of accidents and costly downtime caused by misalignment.
Why Conveyor Belt Pulleys Are Essential for Material Handling Efficiency
Conveyor belt pulleys are more than just mechanical components—they are vital to the overall efficiency and longevity of the conveyor system. Here’s why they matter so much:
Ensuring Smooth Operation: Without well-functioning pulleys, your conveyor system could experience issues like belt slippage, misalignment, or excessive wear. These problems can lead to downtime, repairs, and lost productivity. By keeping the belt properly aligned and tensioned, pulleys ensure that the system runs smoothly, without interruptions.
Reducing Maintenance Costs: Properly selected and maintained conveyor belt pulleys can significantly extend the life of your conveyor system. Pulleys that are sized and positioned correctly prevent excess wear on the belt, reducing the frequency of replacements and repairs. Over time, this can result in substantial savings on maintenance costs.
Preventing Belt Damage: The tension and alignment provided by the pulley system are critical for preventing issues like belt sag, misalignment, or excessive friction. Without pulleys to manage these factors, the belt could become damaged, leading to system inefficiency or even failure. Proper tensioning and alignment also ensure that the load is distributed evenly across the belt, preventing localized damage or stress.
Improving Load Handling: In material handling systems, especially those that deal with heavy or bulky loads, conveyor belt pulleys help distribute the weight of the load evenly across the system. This not only reduces strain on the belt but also ensures that the system can handle high-volume or heavy-duty operations without compromising performance.
In summary, conveyor belt pulleys are crucial for maintaining the stability, efficiency, and longevity of your conveyor system. They not only drive the belt but also provide tension, alignment, and load distribution. Ensuring you have the right pulleys and maintaining them properly will directly contribute to the success and cost-effectiveness of your material handling operations.
Types of Conveyor Belt Pulleys and Their Specific Functions
Conveyor belt pulleys are crucial components in any material handling system, playing a pivotal role in the movement and stability of conveyor belts. Different types of pulleys are used depending on their specific functions within the system, each designed to handle a particular aspect of conveyor operation. From driving the belt to maintaining tension and redirecting the path, conveyor belt pulleys ensure that the entire conveyor system operates smoothly and efficiently.
In this section, we’ll explore the main types of conveyor belt pulleys and their distinct functions, so you can make informed decisions when selecting the right pulleys for your system.
Head Pulleys: Driving the Conveyor Belt
Peralatan head pulley is one of the most important pulleys in a conveyor system. It is located at the discharge end of the conveyor and is typically the primary driving pulley that powers the conveyor belt.
Function: The head pulley is responsible for driving the conveyor belt. It is connected to the motor through a drive shaft and provides the necessary force to move the belt forward. The rotation of the head pulley pulls the belt, causing it to transport materials along the conveyor system.
Lagging: Often, head pulleys are equipped with a rubber or ceramic lagging to increase traction between the pulley and the belt. This improves the grip, preventing slippage and increasing the efficiency of power transmission. Lagging also helps protect the pulley from wear caused by friction with the belt.
Applications: Head pulleys are commonly used in high-speed, high-volume conveyor systems, such as those found in manufacturing facilities, airports, and bulk material handling operations. They are essential for keeping the belt moving at the required speed and carrying the load effectively.
Tail Pulleys: Maintaining Belt Tension and Support
Peralatan tail pulley is positioned at the opposite end of the conveyor system, opposite the head pulley. It does not drive the conveyor belt but plays a critical role in maintaining the stability and tension of the belt.
Function: The tail pulley serves two main functions: providing support and maintaining belt tension. By keeping the belt taut, the tail pulley helps to prevent the belt from sagging, ensuring that it remains in proper alignment. The tension in the belt is crucial for smooth operation and load handling.
Non-Driven: Unlike the head pulley, the tail pulley is typically non-driven, meaning it doesn’t have a motor connected to it. Instead, it functions as a passive pulley that guides the belt into its return section, preparing it for the next cycle.
Applications: Tail pulleys are often found in the return section of the conveyor system, where they provide essential support for the belt, especially in systems with long conveyor lines or when carrying heavy loads.
Snub Pulleys: Enhancing Belt Performance and Redirection
Snub pulleys are often used in conjunction with head and tail pulleys to help improve the performance and efficiency of the conveyor system.
Function: The primary purpose of a snub pulley is to change the direction of the conveyor belt or to increase the contact area between the belt and the driving pulley. By doing so, snub pulleys can improve the transfer of power from the head pulley to the belt, which is particularly useful in systems requiring a high level of power transmission or when the belt needs to be redirected.
Increasing Wrap Angle: One of the key roles of a snub pulley is to increase the wrap angle between the conveyor belt and the head pulley, which helps improve the friction and power transfer. This is particularly important in situations where the load on the conveyor is heavy or where the system operates under high stress.
Applications: Snub pulleys are typically used in situations where the conveyor belt needs to be redirected, or where additional traction is needed to ensure smooth belt movement. They can also be found in high-power conveyor systems where belt performance and energy efficiency are essential.
Take-Up Pulleys: Adjusting Tension and Ensuring Proper Alignment
Peralatan take-up pulley is essential for maintaining correct tension in the conveyor belt, especially in systems where the belt may stretch or sag over time.
Function: The take-up pulley is used to adjust the tension of the conveyor belt as needed. It is typically part of a take-up unit, which allows for the adjustment of belt length to ensure proper tension. By tightening or loosening the take-up pulley, operators can prevent belt slack, reduce the risk of slippage, and ensure smooth, continuous operation.
Types of Take-Up Systems: There are two main types of take-up pulleys: manual take-up and automatic take-up. Manual take-ups require operators to adjust the tension manually, while automatic take-ups use spring mechanisms or hydraulic systems to maintain constant tension automatically.
Applications: Take-up pulleys are used in long conveyor systems or systems where the belt is likely to stretch over time, such as in mining or quarry operations. Proper tensioning is critical to prevent the belt from becoming loose or misaligned.
Drum Pulleys: Versatile and High-Torque Solutions
Drum pulleys are a specific type of pulley used in heavy-duty applications where high torque and durability are needed.
Function: Drum pulleys are designed with a larger diameter, making them more capable of handling higher loads and providing greater torque. These pulleys are ideal for high-load systems and applications where maximum strength and durability are required.
Design: Drum pulleys feature a cylindrical shape, which allows for more contact with the belt, improving grip and ensuring that the belt stays securely in place. These pulleys are often used in high-capacity systems where the belt is carrying large quantities of material over long distances.
Applications: Drum pulleys are often found in bulk material handling systems, such as those in mining, cement manufacturing, and other heavy industries. They are especially useful when working with large, heavy loads or in harsh operating environments where high resistance to wear is necessary.
Conveyor belt pulleys are essential to the smooth operation of conveyor systems, each designed to handle specific functions like driving the belt, maintaining tension, redirecting the belt, or providing support. Understanding the roles of different types of pulleys—head pulleys, tail pulleys, snub pulleys, take-up pulleys, and drum pulleys—is vital for optimizing the efficiency and longevity of your conveyor system. By choosing the right pulleys for your specific application, you can ensure smooth, reliable, and cost-effective material handling.
Conveyor Belt Pulleys and Their Role in System Efficiency and Longevity
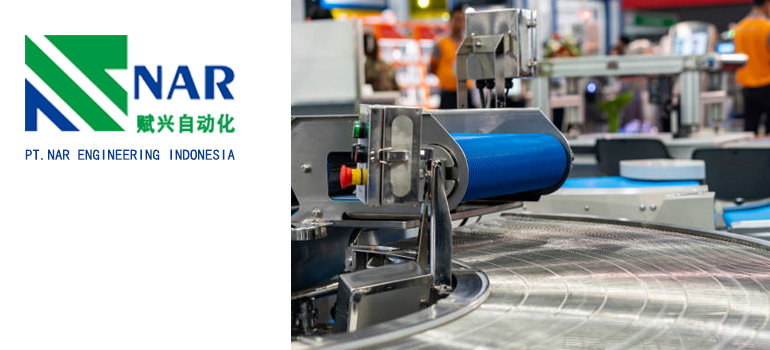
Conveyor belt pulleys are fundamental components that drive, support, and guide the movement of conveyor belts. While they may seem like simple mechanical parts, their design, material selection, and functionality are crucial to the efficiency and longevity of the entire conveyor system. Understanding how conveyor belt pulleys contribute to system performance can help you optimize your material handling operations, reduce maintenance costs, and extend the lifespan of your equipment.
In this section, we will explore the integral role that conveyor belt pulleys play in maintaining system efficiency and promoting longevity, as well as how choosing the right pulley design can impact performance.
The Impact of Conveyor Belt Pulleys on System Efficiency
The efficiency of a conveyor system depends largely on the smooth, uninterrupted movement of the conveyor belt. Pulley design and materials are essential to achieving this goal by ensuring proper belt movement, alignment, and traction.
Power Transmission and Torque Management
Conveyor belt pulleys are directly responsible for transferring power from the motor to the belt. The head pulley, which is typically connected to the motor, generates the rotational force that drives the conveyor. The torque and power transmitted through the pulley system are critical for achieving the required speed and load capacity.
Efficiency Impact: A well-designed head pulley with the correct diameter and material can optimize power transfer, reducing energy consumption while maintaining high throughput. If pulleys are under-designed, it can lead to slippage, increased energy usage, and unnecessary wear on both the pulley and the belt.
Belt Alignment and Tracking
Pulley design, especially crowned pulleys, plays a significant role in ensuring that the conveyor belt stays aligned and does not drift off course. Misalignment can cause the belt to wear unevenly, potentially leading to belt failure or increased friction, which reduces system efficiency.
Efficiency Impact: Properly aligned pulleys prevent excessive belt wear and keep the conveyor running smoothly, preventing downtime and improving operational throughput. By ensuring that the belt runs in the correct path, pulleys help reduce friction, which not only extends the life of the belt but also improves the efficiency of power transmission.
Reducing Slippage and Enhancing Traction
Pulleys, especially head pulleys, often feature lagging (rubber or ceramic coatings) that increase friction between the pulley and the belt. This helps prevent slippage, especially in systems dealing with heavy loads or inclined belts.
Efficiency Impact: When slippage is minimized, the pulley maintains consistent power transfer, reducing energy loss and avoiding the risk of damage to the belt or motor. This results in better energy efficiency and smoother operation.
Conveyor Belt Pulleys and Their Role in Longevity
In addition to improving efficiency, conveyor belt pulleys play a key role in extending the longevity of the entire conveyor system. By reducing wear and tear on the belt and other components, well-maintained pulleys help ensure that the system continues to function effectively for longer periods, ultimately lowering maintenance costs and improving the system’s return on investment.
Preventing Excessive Belt Wear
The tension and alignment provided by pulleys are critical for preventing uneven wear on the conveyor belt. For example, tail pulleys help keep the return portion of the belt taut, preventing sagging and unnecessary friction that could damage the belt.
Longevity Impact: Pulley systems that maintain proper belt tension and alignment reduce the risk of belt sag, stretching, or excessive friction, all of which can cause premature wear and increase the frequency of belt replacements. By minimizing these issues, pulleys contribute to the longer lifespan of the belt.
Protecting the Pulley Surface from Wear
Lagging on pulleys—rubber, ceramic, or other abrasion-resistant coatings—helps protect the pulley’s surface from wear caused by continuous friction with the conveyor belt. Over time, the repeated contact between the pulley and the belt can cause surface degradation, affecting both performance and durability.
Longevity Impact: Lagging reduces the frictional wear on pulleys, preventing metal fatigue and extending the life of the pulleys themselves. It also helps maintain consistent traction, preventing slippage, and further protecting the system from damage.
Reducing Stress on Other Conveyor Components
Well-maintained pulleys help distribute the load more evenly across the system, reducing stress on other components like the idler rollers, motors, and bearings. By providing proper tension and alignment, pulleys prevent undue strain on these other parts, reducing the likelihood of component failure and extending the lifespan of the entire conveyor system.
Longevity Impact: Even load distribution minimizes wear on other parts of the system, leading to fewer breakdowns and reduced maintenance costs. With fewer parts needing repair or replacement, the overall system operates more efficiently over a longer period.
How to Choose the Right Conveyor Belt Pulley for Optimal Efficiency and Longevity
To get the most out of your conveyor belt pulleys, it’s important to consider a few key factors when choosing the right pulleys for your system. Selecting the correct materials, designs, and features can directly affect both the efficiency and longevity of the entire conveyor system.
Consider the Load and Capacity
The size and material of the pulley should be chosen based on the weight of the materials being transported. For high-load applications, steel or cast iron pulleys are ideal due to their durability and strength. For lighter loads, aluminum or rubber-coated pulleys may be sufficient.
Efficiency and Longevity Tip: Choose pulleys with a high torque capacity and durable materials to ensure they can handle the load without excessive wear or slippage.
Understand Environmental Conditions
If your conveyor system operates in harsh conditions (e.g., wet, corrosive, or high-temperature environments), selecting corrosion-resistant pulleys (such as stainless steel or pulleys with protective coatings) will improve both system efficiency and longevity.
Efficiency and Longevity Tip: Opt for pulleys with rubber or ceramic lagging in applications where wear is likely to be an issue, such as those handling abrasive materials or operating in extreme conditions.
Choose the Right Pulley Size and Design
The diameter and design of the pulley must match the requirements of the conveyor belt. Larger pulleys increase surface contact, improving power transfer and reducing slippage. Crowned pulleys are ideal for maintaining belt alignment, ensuring the belt moves smoothly without drifting.
Efficiency and Longevity Tip: Ensure that the pulleys are properly sized for the system. Oversized pulleys may cause unnecessary stress on the motor, while undersized pulleys can lead to slippage and inefficient power transfer.
Regular Maintenance and Inspection
Properly maintaining your pulleys is crucial for ensuring the continued efficiency and longevity of the system. Regular inspection for wear, proper alignment, and the condition of lagging and shafts will help identify any issues before they cause system failures.
Efficiency and Longevity Tip: Implement a scheduled maintenance program to inspect and replace pulley lagging, check for misalignment, and ensure the proper functioning of pulleys and associated components. This proactive approach will prevent major breakdowns and extend the life of the system.
Conveyor belt pulleys are essential components that directly influence both the efficiency and longevity of the conveyor system. By ensuring proper power transmission, belt alignment, and load distribution, pulleys help the system run smoothly and efficiently, while also reducing wear and extending the lifespan of other components. To maximize the performance of your conveyor system, it’s important to choose the right materials, design, and size for your specific application, and to regularly maintain and inspect your pulleys. This proactive approach will not only improve efficiency but also ensure the long-term durability and cost-effectiveness of your conveyor system.
Selecting and Installing Conveyor Belt Pulleys for Your System
When designing or upgrading a conveyor system, conveyor belt pulleys are key components that need careful consideration to ensure optimal performance and longevity. Choosing the right pulleys and installing them correctly can significantly improve the efficiency of your conveyor system, reduce wear and tear, and minimize maintenance costs.
In this section, we’ll explore how to select the right conveyor belt pulleys for your system, the factors to consider during selection, and the best practices for installation to ensure that your system operates smoothly.
Factors to Consider When Selecting Conveyor Belt Pulleys
Selecting the right conveyor belt pulleys involves understanding the specific needs of your system and the environmental conditions in which the system will operate. Here are key factors to consider during the selection process:
Conveyor System Type and Application
The first step in selecting the appropriate pulleys is understanding the type of conveyor system you have. There are different types of conveyor systems, including horizontal, inclined, and vertical conveyors, each requiring specific pulley designs. The application will also determine the pulley size, material, and features.
Flat Belt Conveyors: For standard flat belt conveyors, pulleys are generally simpler, with a focus on maintaining alignment and driving the belt.
Inclined/Declined Conveyors: These systems require pulleys designed to handle the added tension and load of materials moving up or down a slope. Pulley sizes and torque capacity must be chosen accordingly.
Heavy-Duty Conveyors: Applications like mining, construction, or bulk material handling demand high-strength pulleys capable of withstanding high loads and abrasive materials.
Belt Width and Load Capacity
The width of your conveyor belt and the load it will carry directly impact the size and material of the pulleys. Wider belts and systems that carry heavier loads require larger, more robust pulleys to distribute the weight effectively.
Heavy Load Systems: Pulleys made of steel or cast iron are typically used for heavy-duty systems, as they can withstand high torque and provide better power transmission.
Lighter Systems: For lighter conveyor systems, aluminum or rubber-coated pulleys may be sufficient, offering a good balance between cost and performance.
Material and Environmental Conditions
The materials being transported, as well as the environment in which the conveyor system operates, play a significant role in pulley selection. Factors such as temperature extremes, humidity, dust, chemicals, and abrasion need to be taken into account.
Corrosive Environments: For systems operating in wet or corrosive environments (e.g., food processing or chemical industries), stainless steel pulleys or pulleys with corrosion-resistant coatings are essential to prevent rust and degradation.
Heavy Abrasion: If your system handles materials that are abrasive (e.g., sand, gravel, or coal), pulleys with ceramic lagging or other abrasion-resistant materials will extend the lifespan of both the pulley and the belt.
Pulley Lagging and Surface Coatings
Lagging is a critical feature for head pulleys, where it helps improve traction between the pulley and the belt, reducing slippage and wear. Depending on your application, you may need to choose the right type of lagging:
Rubber Lagging: This is commonly used for most general-purpose applications, offering a good balance of durability and traction.
Ceramic Lagging: For highly abrasive applications, ceramic lagging offers superior protection and increased grip, especially in mining or quarrying environments.
Pulley Shaft and Mounting Type
Peralatan pulley shaft and mounting method must be designed to withstand the torque and loads generated by the conveyor. Different mounting options, such as tapered bushings, keyed shafts, or bearing mounts, offer flexibility in installation and maintenance.
Tapered Bushing Mounting: Common in industrial applications, this allows for easy pulley installation and removal, especially when pulleys are subjected to high torque.
Keyed Shaft Mounting: Provides secure mounting but may require more effort during installation or replacement.
Best Practices for Installing Conveyor Belt Pulleys
Once you’ve selected the right conveyor belt pulleys, proper installation is essential for optimal performance and system longevity. Here are some best practices to follow during installation:
Ensure Proper Alignment
Misaligned pulleys can cause the conveyor belt to wear unevenly, drift, or even come off the tracks. It’s critical to ensure that pulleys are aligned correctly to prevent these issues.
Installation Tip: Use a laser alignment tool or a string line to verify the alignment of both the head and tail pulleys. Proper alignment ensures that the conveyor belt runs smoothly and reduces the chances of misalignment.
Check Pulley Mounting and Shaft Installation
When mounting pulleys, make sure that the shaft is installed correctly and securely. The shaft should be checked for any damage or wear, as this can affect pulley performance.
Installation Tip: Tighten the pulley fasteners to the manufacturer’s recommended torque specifications to avoid issues such as slippage or misalignment. Ensure the shaft is firmly seated in the bearing.
Install Lagging on the Head Pulley
If your system uses lagging, make sure that it is installed correctly, especially on the head pulley. Lagging helps increase traction and prevents slippage, but it needs to be properly attached and aligned.
Installation Tip: Use the correct adhesive or fastening method for the lagging material, depending on whether it’s rubber, ceramic, or another type of material. Ensure that there are no gaps or loose sections, as these can cause uneven wear.
Verify Tension and Tracking
Once the pulleys are installed, check the belt tension and ensure that the belt is tracking properly. Incorrect tension can lead to belt slippage or excessive wear, while improper tracking can cause the belt to drift off the pulleys.
Installation Tip: Adjust the take-up pulley (if equipped) to maintain proper belt tension. Also, inspect the alignment of all pulleys to ensure that the belt is running smoothly along its path.
Test the System Before Full Operation
After installation, it’s important to test the conveyor system to ensure that everything is operating correctly before full-scale production. Run the system at low speeds and gradually increase to the desired operating speed, monitoring for any unusual vibrations, misalignment, or noise.
Installation Tip: During the test run, check for any unusual wear on the belt or pulleys, and inspect the pulley bearings for proper operation. Make adjustments as needed to ensure smooth, efficient operation.
Maintenance and Monitoring After Installation
Even after proper installation, ongoing maintenance and monitoring are necessary to keep conveyor belt pulleys operating at their best. Here are some key tips for maintaining your system:
Regular Inspections
Regularly inspect the pulley lagging for signs of wear, and check the pulleys themselves for any damage, such as cracks, rust, or misalignment. Pulley bearings should also be inspected for proper lubrication and wear.
Maintenance Tip: Keep a detailed log of inspections and replace parts that show signs of significant wear before they fail. This proactive approach minimizes downtime and reduces emergency repairs.
Lubricate Bearings and Shafts
Proper lubrication of pulley bearings and shafts is crucial to reducing friction, wear, and overheating. Follow manufacturer guidelines for lubrication intervals and types of grease or oil to use.
Maintenance Tip: Implement a regular lubrication schedule to ensure bearings remain well-lubricated and to avoid bearing failure, which could lead to costly downtime.
Monitor Belt Tension and Tracking
Over time, the tension on your conveyor belt may change due to stretching or wear. Keep an eye on belt tension and tracking to ensure that the pulleys are operating efficiently.
Maintenance Tip: If the belt becomes loose or misaligned, adjust the take-up pulley and check pulley alignment again to ensure everything is running smoothly.
Selecting and installing the right conveyor belt pulleys is essential for ensuring the efficiency and longevity of your conveyor system. Key considerations include the type of application, belt width and load capacity, material choices based on environmental conditions, and pulley design. Proper installation, alignment, and ongoing maintenance are critical to keeping your conveyor running smoothly and avoiding costly downtime. By following these selection and installation best practices, you can optimize system performance, reduce maintenance costs, and extend the life of your conveyor system.