Summary:
Anchored in Efficiency: The Role of Ship Loading Systems in Maritime Operations
Components of Ship Loading Systems
Importance of Efficient Ship Loading
Optimization Techniques for Ship Loading Systems
Future Trends in Ship Loading Systems
In this chapter, we will delve into various aspects of ship loading system, taking you into this precise and complex world. The ship loading system is not just about simply loading goods onto the ship, it involves a series of complex processes and technologies, from the smooth transfer of goods from the dock to the ship, to ensuring the safe and effective distribution of loads.
In the following content, we will delve into the various components of a ship loading system, understand their functions and roles, and how they work together to achieve a smooth loading process. Whether you are a beginner or an expert in ship loading systems, this chapter will provide you with valuable insights and give you a deeper understanding of this critical field.
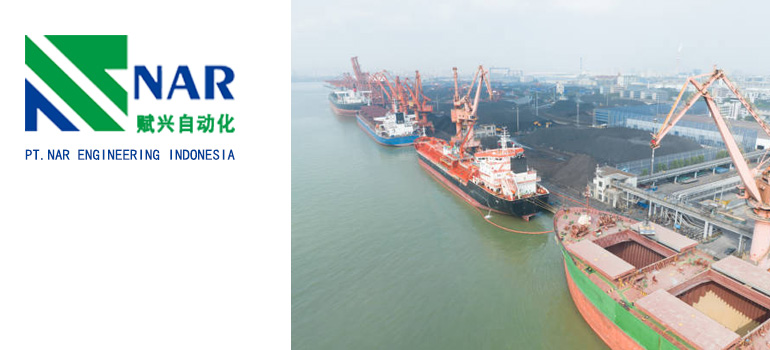
Components of Ship Loading Systems
The ship loading system consists of multiple key components, each of which plays a crucial role in ensuring the safe and efficient loading of goods onto the ship. The following are some common key components in ship loading systems:
1. Conveyor Systems
The conveyor belt system is one of the most common components in ship loading system. These systems use conveyor belts to transport goods from docks or warehouses to the cargo hold of ships. A conveyor belt system typically consists of one or more conveyor belts that can be adjusted and controlled as needed to accommodate different types and sizes of goods.
a. Belt Conveyors
Belt conveyors are one of the most common types of conveyor belts, which transport goods from one location to another through electrically driven belt conveyors. Belt conveyors are suitable for transporting various types of goods, including bulk materials, solid materials, and liquid materials.
b. Roller Conveyors
Roller conveyors use drums to support and transport goods, usually used to transport heavy goods or goods that require additional support. Roller conveyors can be customized as needed to meet various cargo and loading needs.
2.Cranes and Lifts
Cranes and elevators are another important component in ship loading systems, used to lift cargo from the ground or dock to the ship’s cargo hold. These devices can be operated and controlled as needed to ensure the safety and effective loading of goods.
a.Gantry Cranes
Gantry cranes are a commonly used type of crane that lift and move cargo through a frame spanning the cargo hold. Gantry cranes usually have a large lifting capacity and are suitable for loading heavy goods or goods that require significant movement.
b. Ship to Hole Cranes
Quay crane is a type of crane specifically designed for cargo loading and unloading between docks and ships. These cranes typically have large lifting arms and adjustable operating platforms that can easily handle various types and sizes of goods.
3. Loading Software
Loading software plays an increasingly important role in modern ship loading systems, helping to optimize the loading process and improve efficiency by providing real-time data and intelligent control functions. These software typically include functions such as ship loading planning, cargo tracking, and loading operation monitoring, which can help ship operators achieve more precise and efficient loading operations.
Importance of Efficient Ship Loading
Efficient ship loading is not just about getting cargo onto a vessel; it’s the linchpin of maritime operations, influencing everything from profitability to environmental impact. Let’s delve into why efficient ship loading is paramount:
Economic Implications: Time is money in the shipping industry. Efficient loading means quicker turnaround times at ports, reducing idle time for vessels and minimizing labor costs. Moreover, it ensures that vessels can adhere to tight schedules, avoiding costly delays and penalties.
Optimized Resource Utilization: Every square meter of a ship’s cargo hold is valuable real estate. Efficient loading maximizes cargo capacity, allowing shipping companies to transport more goods in fewer trips. This optimization leads to increased revenue potential and reduced fuel consumption per unit of cargo transported.
Safety and Stability: Properly distributed cargo enhances a vessel’s stability and reduces the risk of accidents such as capsizing or cargo shifting during transit. Efficient loading involves careful consideration of weight distribution, securing methods, and adherence to maritime regulations, ultimately safeguarding crew, cargo, and the environment.
Environmental Impact: Shipping is a significant contributor to global carbon emissions. Streamlining loading processes reduces the time vessels spend idling at ports, resulting in lower fuel consumption and emissions. Additionally, maximizing cargo capacity per voyage reduces the carbon footprint per unit of cargo transported.
Competitive Advantage: In today’s global market, efficiency is a competitive differentiator. Shipping companies that can consistently offer faster turnaround times and lower transportation costs gain a competitive edge. Efficient ship loading enables companies to deliver goods more swiftly and cost-effectively, attracting and retaining customers in a fiercely competitive industry.
Supply Chain Reliability: Efficient ship loading contributes to the overall reliability of the supply chain. By ensuring timely and predictable delivery of goods, it minimizes disruptions and inventory shortages for businesses relying on maritime transportation. This reliability fosters trust among suppliers, manufacturers, and retailers, strengthening business relationships and enhancing customer satisfaction.
In essence, efficient ship loading is the cornerstone of a sustainable and profitable maritime industry. By optimizing loading processes, shipping companies can achieve economic efficiency, environmental sustainability, and operational resilience, driving growth and innovation in global trade.
Optimization Techniques for Ship Loading Systems
Optimization techniques play a crucial role in enhancing the efficiency and effectiveness of ship loading system. Let’s explore some key strategies:
Advanced Planning and Scheduling: Utilizing sophisticated planning software can optimize loading sequences based on factors such as cargo type, destination, vessel capacity, and port infrastructure. These tools consider various constraints, including weight distribution, stability requirements, and berth availability, to generate optimal loading plans.
Real-Time Data Integration: Integrating real-time data streams from sensors, RFID tags, and port management systems allows for dynamic adjustments during the loading process. By continuously monitoring factors such as cargo volume, weight distribution, and weather conditions, operators can adapt loading plans in response to changing circumstances, maximizing efficiency and safety.
Automation and Robotics: Implementing automation technologies, such as automated stacking cranes and robotic loaders, can significantly reduce loading times and labor costs while improving accuracy and safety. These systems can handle repetitive tasks with precision, freeing up human operators to focus on supervisory roles and exception handling.
Simulation and Modeling: Utilizing simulation software enables operators to simulate loading scenarios and evaluate the impact of different variables on performance and safety. By conducting virtual trials, operators can identify potential bottlenecks, optimize equipment utilization, and validate loading plans before implementation, minimizing risks and maximizing efficiency.
Containerization and Unitization: Standardizing cargo packaging into containers or units facilitates efficient handling and loading processes. By consolidating smaller shipments into larger containers, operators can reduce loading times, minimize handling costs, and optimize space utilization within vessels, ultimately increasing throughput and profitability.
Dynamic Berth Allocation: Implementing dynamic berth allocation systems allows ports to allocate berths based on real-time conditions and vessel priorities. By optimizing berth assignments and minimizing waiting times, ports can reduce congestion, improve turnaround times, and enhance overall port efficiency.
Energy-Efficient Equipment: Investing in energy-efficient loading equipment and technologies, such as electric cranes and eco-friendly materials, can reduce fuel consumption and environmental impact. By adopting sustainable practices, operators can achieve cost savings, regulatory compliance, and enhanced corporate responsibility.
Collaborative Decision-Making: Facilitating collaboration among stakeholders, including shipping companies, port authorities, and terminal operators, fosters alignment of interests and sharing of resources. By coordinating efforts and sharing data, stakeholders can optimize resource allocation, streamline processes, and improve overall supply chain efficiency.
By leveraging these optimization techniques, operators can unlock significant efficiency gains, reduce costs, and enhance competitiveness in the global maritime industry. Continual innovation and investment in technology will be key drivers in shaping the future of ship loading systems.
Future Trends in Ship Loading Systems
As technology continues to advance, several future trends are poised to transform ship loading system, revolutionizing efficiency, safety, and sustainability. Here are some key trends to watch:
Smart and Autonomous Systems: The integration of artificial intelligence (AI) and machine learning (ML) algorithms will enable ship loading systems to become smarter and more autonomous. AI-powered optimization algorithms can dynamically adjust loading plans based on real-time data, optimizing cargo distribution, and vessel stability. Autonomous loading equipment, such as robotic cranes and automated conveyors, will further streamline operations while reducing labor costs and enhancing safety.
Internet of Things (IoT) Connectivity: IoT sensors embedded in loading equipment and cargo containers will enable real-time monitoring of cargo status, environmental conditions, and equipment performance. This connectivity will facilitate predictive maintenance, allowing operators to identify and address potential issues before they lead to downtime or accidents. Additionally, IoT data analytics will provide valuable insights into loading operations, enabling continuous improvement and optimization.
Digital Twins and Simulation: Digital twin technology will enable operators to create virtual replicas of loading systems and simulate loading scenarios in real time. By simulating various factors such as cargo types, weather conditions, and equipment configurations, operators can optimize loading plans, assess the impact of different variables, and identify potential risks or bottlenecks. This predictive capability will improve efficiency, safety, and resilience in loading operations.
Green and Sustainable Practices: Growing environmental concerns and regulatory pressures will drive the adoption of green and sustainable practices in ship loading systems. This includes the use of eco-friendly materials in loading equipment, the integration of renewable energy sources such as solar and wind power, and the implementation of energy-efficient technologies. Sustainable loading practices will not only reduce carbon emissions and environmental impact but also improve corporate social responsibility and stakeholder trust.
Blockchain and Supply Chain Transparency: Blockchain technology will enhance transparency and traceability in the supply chain, including loading operations. By recording transactional data in a tamper-proof and decentralized ledger, blockchain can provide a verifiable record of cargo movements, ownership transfers, and compliance with regulations. This transparency will improve trust among supply chain partners, reduce disputes, and enhance security in loading operations.
3D Printing and On-Demand Manufacturing: Advances in 3D printing technology will enable on-demand manufacturing of spare parts and replacement components for loading equipment. This decentralized approach to manufacturing will reduce lead times, inventory costs, and reliance on traditional supply chains. Additionally, 3D printing can enable customized solutions for specific loading requirements, improving adaptability and efficiency in loading operations.
These future trends represent exciting opportunities for innovation and transformation in ship loading systems. By embracing emerging technologies and sustainable practices, operators can unlock new levels of efficiency, safety, and resilience in maritime logistics. Continual investment in research and development will be essential to staying ahead in a rapidly evolving industry landscape.
Maybe you are interested in the following: Maximizing Efficiency: Strategies for Bulk Material Handling Excellence