Summary:
Advantages of automated storage and retrieval systems in different industries
What is automated storage and retrieval systems?
5 Types of AS/RS system
Application of Automated storage systems
AS/RS (Automated Storage and Retrieval System), which is commonly referred to as the automated storage system, is an automated system composed of high-rise three-dimensional shelves, stackers, conveying systems, information recognition systems, computer control systems, communication systems, monitoring systems, management systems, etc.
AS/RS can continuously check expired or find products in stock, prevent defective inventory and improve management level. The automatic storage system can make full use of the storage space, realize the online control of the equipment through the computer, handle the goods quickly and accurately on the principle of first in, first out, and reasonably conduct the inventory management and data processing.
What is automated storage and retrieval systems
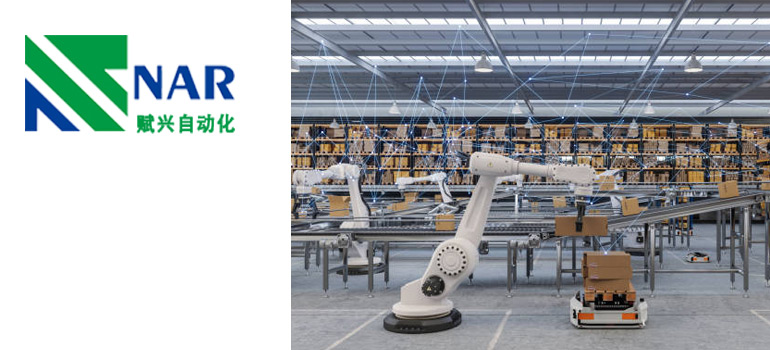
Automated warehouse is generally composed of high-rise shelves, storage machinery and equipment, buildings, control and management facilities and peripheral equipment. Commonly used storage machinery and equipment include various handling equipment and conveying equipment such as stacking cranes, overhead forklifts, roller or chain conveyors, roadway transfer trolleys, elevators, automatic guided trolleys, shuttle cars, and cargo trays.
AS/RS represents “automatic storage and retrieval” to realize automatic storage without human involvement. The use of AS/RS storage system can reduce the time required to find goods and reduce labor costs.
5 Types of AS/RS system
With the development of e-commerce, ASRS technology is constantly updated, and these technologies can handle different quantities, types and speeds of non-palley inventory. Which one you choose depends on your specific operation, the storage density required by your facility, your throughput target and your budget.
The technology used in ASRS determines its type, including several. Let’s take a brief look at the five main automatic storage and retrieval systems.
1. Turntable AS/RS
The turntable AS/RS system can be used as a horizontal or vertical conveyor belt, including stock pallets that rotate continuously along the track. If the operator is running, the conveyor belt will automatically rotate to provide access to the tray containing the box containing the required items.
Only one pallet can be delivered at a time, so the productivity is limited by how many commonly ordered products can be accommodated in one pallet. In order to increase throughput, additional complete machines need to be added, and then the inventory needs to be split to multiple machines, or a separate consolidation process needs to be added.
2. Vertical lift module (VLM) ASRS
Pallets are placed in the vertical lifting system to reduce storage space. It consists of an inserter/extractor in the middle and a tray column closed on both sides. When the operator is running, the inserter/extractor selects the correct tray and delivers it.
Pallet return can be fixed back to the same shelf or dynamic, and the system will automatically adjust when the inventory changes. These systems are especially suitable for warehouses with different stock sizes. It can only handle one pallet at a time, so its productivity is limited.
3. Small load ASRS
The characteristic of small goods is that there is only one crane for each passage. They are located on rails or wheels to handle loads in handbags, boxes or pallets.
The system is applicable to the full-box picking operation, such as store replenishment or minimum order quantity. However, they are considered unreliable because the technology is very old and all work depends on a crane: if it breaks down or breaks down, it may cause huge damage.
4.ASRS based on robot shuttle
This dynamic storage solution uses a robot shuttle to move independently along a narrow track to quickly retrieve inventory and deliver it to the workstation. According to the needs of the warehouse, it can be customized to run at one or more levels.
The advantage of these systems is that they are very fast and can achieve very high rendering rate, so they are very common in high-throughput environments. However, to take advantage of this speed, they need a lot of additional resources and energy. The management cost is high.
5. Robot ASRS
The intelligent robot independently runs through the covered grid, shuffles, classifies and retrieves the boxes, and takes them to the workstation (port) for order picking. These robots are connected to the system wirelessly and charge themselves when not in use. The controller and built-in software can track everything.
The modular design of the robot makes it easy to configure the system according to the change of throughput requirements. With high scalability and flexibility, it is the only solution that can easily add each component independently.
Application of Automated storage systems
Automated storage systems are widely used. They can help track warehouse delivery time and reduce costs. The application brings different advantages in different industries:
Automobile industry: using AS/RS system can easily move parts and distribute them to the whole company chain.
Food and beverage industry: The industry has rapidly adopted AS/AR storage systems to extend the shelf life of products, and transported them from point A to point B without sacrificing the agreement and fresh food standards.
Chemicals: can transport dangerous goods efficiently and reduce harm to employees.
Electronic products: using AS/RS system can handle expensive products carefully.
E-commerce: use the automated training system to reduce the error rate of order information and the risk of product damage.
For more information about automated storage and retrieval systems, contact PT.Nar.