Summary:
Maximizing Efficiency with Conveyor Belt Loading Systems: Key Benefits for Your Operations
Understanding Conveyor Belt Loading Systems: How They Work
Top Benefits of Conveyor Belt Loading Systems for Your Operations
Optimizing Conveyor Belt Loading Systems for Maximum Performance
Understanding Conveyor Belt Loading Systems: How They Work
Conveyor belt loading systems have become an essential component in modern industries, transforming the way materials are moved from one place to another. Whether in manufacturing, logistics, or mining, these systems provide a highly efficient method for transporting goods, raw materials, and products, helping businesses maximize productivity while reducing manual labor. But how do these systems work, and what makes them so effective in a wide range of applications? Let’s dive into the mechanics and components that make conveyor belt loading systems a key player in modern operations.
The Basic Mechanism of Conveyor Belt Loading Systems
At its core, a conveyor belt loading system is a continuous loop of material handling equipment designed to move items from one location to another, often across long distances or at varying elevations. These systems typically consist of a flexible belt that is driven by a motor and supported by rollers or pulleys. The belt moves materials, products, or components along a predetermined path, allowing for smooth and consistent transportation.
The most fundamental mechanism behind a conveyor belt loading system is the motorized drum or pulley that drives the belt. The motor, which is usually powered by electricity or hydraulic energy, rotates the pulley, causing the belt to move in a continuous loop. As the belt moves, it can be equipped with different loading and unloading mechanisms—such as hoppers or chutes—that allow materials to be added or removed at specific points along the system.
A key feature of conveyor belt systems is their ability to operate continuously, offering a steady and reliable flow of goods without the need for constant human intervention. The use of a conveyor belt loading system minimizes downtime and enhances efficiency, as it can run for extended periods without requiring significant maintenance or attention.
Different Types of Conveyor Belt Loading Systems
Not all conveyor belt loading systems are created equal. Depending on the specific needs of the operation, there are various types of conveyor systems designed to handle different materials and tasks. Let’s take a look at some of the most commonly used systems:
Flat Belt Conveyors: These are the most basic and versatile type of conveyor belt system, with a flat, continuous belt that moves goods along a horizontal or slightly inclined path. They are ideal for moving light to medium-weight products, such as packaged goods, small components, and even food items in certain cases. Flat belt conveyors are commonly used in manufacturing lines and packaging facilities.
Trough Belt Conveyors: For industries like mining or bulk material handling, trough belt conveyors are ideal. These systems have a belt that forms a trough-like shape, allowing for the transportation of loose, bulk materials such as coal, gravel, or sand. The edges of the belt are typically raised to prevent materials from spilling off during transport.
Inclined and Declined Conveyors: In many cases, materials need to be moved vertically or at an incline to reach different levels of a facility. Inclined and declined conveyors are designed to handle these challenges by using belts that are angled to lift or lower materials from one height to another. These systems are especially useful in warehouses or distribution centers where products need to be moved between different floors or sections of a building.
Cleated Belt Conveyors: These systems feature belts with raised edges or cleats that help keep materials in place while they’re being transported. This makes them ideal for moving materials that are inclined or prone to slipping, such as packaged products, boxes, or even wet materials in food processing applications.
Each of these conveyor belt loading systems is tailored to different operational needs. The choice of system largely depends on the type of material being handled, the required speed, the environment in which the system operates, and the overall layout of the facility.
Key Components of a Conveyor Belt Loading System
The efficiency and reliability of a conveyor belt loading system depend on its components, each of which plays a critical role in ensuring smooth and continuous operation. Here are the main components you’ll typically find in a conveyor belt system:
Belt: The heart of the system, the conveyor belt itself can be made from a variety of materials depending on the type of goods being transported. For example, rubber or PVC belts are commonly used for general material handling, while steel belts may be used for heavy-duty applications that require durability and heat resistance.
Pulleys and Rollers: These are the rotating components that guide the belt along its path. Pulleys at either end of the conveyor (the drive pulley and the tail pulley) provide the necessary tension to keep the belt moving smoothly, while rollers along the length of the conveyor reduce friction and ensure the belt remains aligned.
Motor: The motor is what drives the system, providing the energy needed to turn the pulleys and move the belt. The motor can be either electric or hydraulic, depending on the size of the system and the power required. Larger industrial systems may use more powerful motors to handle heavy loads.
Frames and Supports: The structure that holds everything in place, the frame supports the pulleys, rollers, and the belt itself. Frames are typically made from steel or aluminum, designed to be both strong and lightweight, ensuring the conveyor system can withstand the weight of the materials being moved without tipping or sagging.
Loading and Unloading Mechanisms: Conveyor belt loading systems often feature mechanisms that allow for the efficient loading and unloading of materials. These can include chutes, hoppers, or automated arms that feed materials onto the belt or remove them once they reach their destination. These systems can be designed to operate manually or automatically, depending on the complexity of the operation.
By understanding how these components work together, businesses can better maintain and optimize their conveyor belt loading systems, ensuring they run smoothly and without interruption.
Top Benefits of Conveyor Belt Loading Systems for Your Operations
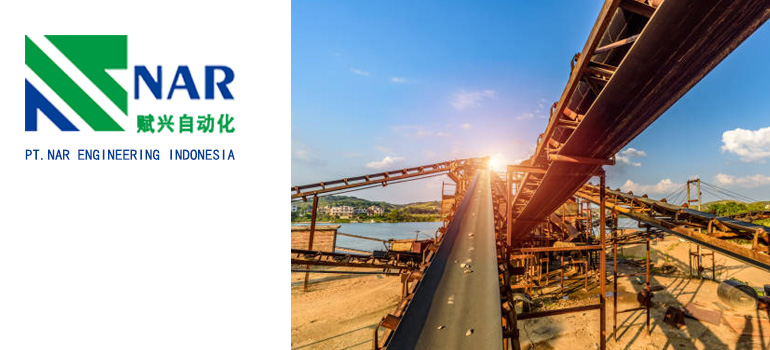
Conveyor belt loading systems are a game changer for many industries, offering a wide range of benefits that streamline operations, enhance safety, and improve efficiency. Whether you’re working in manufacturing, logistics, mining, or food processing, these systems provide powerful solutions to common challenges in material handling. In this section, we will explore the key advantages of implementing conveyor belt loading systems and how they can transform your operations for the better.
Increased Operational Efficiency with Conveyor Belt Loading Systems
One of the most significant advantages of conveyor belt loading systems is the boost in operational efficiency. By automating the movement of materials, these systems reduce the need for manual labor and eliminate inefficiencies associated with traditional material handling methods.
Faster Material Movement: Conveyor belts are designed to move materials continuously, which means they can handle large volumes of goods much faster than human workers. This speed increases overall throughput and ensures that products or materials are consistently available when needed, minimizing delays.
24/7 Operation: Conveyor belt systems can run continuously, providing around-the-clock operation. Unlike manual labor, which is limited by shift changes, breaks, and human fatigue, conveyor systems can maintain a high level of productivity for longer periods, ultimately maximizing output and reducing downtime.
Reduced Bottlenecks: In many industrial environments, bottlenecks in the supply chain can slow down operations. Conveyor belt loading systems help to mitigate these bottlenecks by creating a steady and predictable flow of materials. This consistency allows for smoother transitions between different stages of production, assembly, or packaging.
By reducing manual intervention and speeding up the movement of materials, conveyor belt systems optimize workflows and significantly improve overall efficiency.
Enhancing Safety and Reducing Workplace Injuries
Workplace safety is a top priority in any industrial operation. Conveyor belt loading systems contribute to a safer work environment in several key ways.
Minimizing Manual Handling: One of the primary risks in warehouses, factories, and distribution centers is the manual handling of heavy or bulky materials. Conveyor belts take over much of this responsibility, reducing the physical strain on workers and lowering the risk of musculoskeletal injuries.
Automation of Hazardous Tasks: In some industries, such as mining or food processing, workers are often exposed to dangerous materials or conditions. Conveyor systems can be designed to handle hazardous materials, thus minimizing direct human contact with potentially harmful substances like chemicals, hot items, or sharp objects.
Improved Workplace Ergonomics: Conveyor belt systems can be customized to adjust to the optimal working height for loading and unloading materials. This reduces the need for employees to bend, lift, or stretch, which helps to avoid back injuries, strains, and repetitive stress injuries.
By automating tasks that would otherwise require manual labor, conveyor belt systems not only increase efficiency but also protect the well-being of your workforce.
Cost Savings: How Conveyor Belt Loading Systems Reduce Operational Costs
Investing in conveyor belt loading systems can lead to significant cost savings across various areas of operation.
Labor Cost Reduction: One of the most immediate cost-saving benefits is the reduction in labor costs. With conveyor belts handling the bulk of the material movement, businesses can reallocate workers to more value-added tasks. In some cases, the reduction in manual labor can lead to a decrease in the number of employees needed for specific operations, directly lowering payroll expenses.
Minimized Product Damage: Conveyor belt systems are designed to handle materials gently and consistently. The automation process reduces the likelihood of damage during loading, unloading, or transportation. With fewer damaged products, companies can reduce waste and lower the cost of replacements or rework.
Energy Efficiency: Modern conveyor belt systems are increasingly energy-efficient, with motors designed to minimize energy consumption while delivering high performance. Some systems even feature regenerative drives that recapture energy from braking, further reducing electricity costs. Choosing energy-efficient components can significantly lower long-term operational expenses.
Reduced Downtime and Maintenance Costs: Conveyor systems are designed for durability and reliability. With proper maintenance, these systems can run for extended periods with minimal interruptions. Preventative maintenance practices, such as lubrication and regular inspections, can help reduce unexpected breakdowns and costly repairs.
In the long run, the initial investment in conveyor belt loading systems pays off through labor savings, less product damage, and reduced maintenance costs, all contributing to lower overall operating expenses.
Versatility Across Various Applications and Industries
Conveyor belt loading systems are highly versatile and can be customized to meet the needs of different industries. Whether you’re transporting raw materials, packaged goods, or perishable items, there’s a conveyor system design that fits the job.
Manufacturing and Assembly Lines: In manufacturing plants, conveyor belts are used to transport parts between workstations, making the assembly process more streamlined and reducing manual handling. With the ability to handle various materials, from small components to large, heavy parts, these systems are integral to assembly lines.
Warehousing and Distribution: In distribution centers, conveyor belts move goods through sorting and packing stations, improving inventory control and order fulfillment. Automated conveyor systems can be synchronized with warehouse management software to track goods in real-time, ensuring faster and more accurate shipments.
Food Processing and Packaging: In food industries, conveyor belts are used to move products through different stages of processing and packaging. These systems are designed to meet food safety standards, such as easy cleaning and sanitation, to prevent contamination during processing.
Mining and Bulk Material Handling: Conveyor belts are also widely used in industries that handle bulk materials, like coal, grains, or minerals. Trough belt conveyors, for example, are designed to carry large quantities of material over long distances and rough terrain, making them ideal for mining and quarrying operations.
The adaptability of conveyor belt loading systems allows them to be used in virtually any industry, helping businesses improve processes, scale operations, and meet specific handling requirements.
Environmental Benefits: Sustainability and Waste Reduction
In today’s environmentally-conscious world, many businesses are seeking ways to reduce their carbon footprint and adopt more sustainable practices. Conveyor belt loading systems contribute to environmental goals in several ways.
Energy Efficiency: As mentioned earlier, modern conveyor systems are designed with energy efficiency in mind. Energy-efficient motors and regenerative drives help to reduce the overall electricity consumption of the system, contributing to a lower carbon footprint.
Reduced Packaging Waste: Conveyor belts can streamline the packaging process, ensuring that materials are moved efficiently through automated packing stations. By minimizing human handling and optimizing the packaging process, businesses can reduce material waste, such as excess plastic or packaging materials, leading to more sustainable operations.
Recycling and Reuse: Conveyor belt systems can be designed with the ability to sort materials for recycling, making them an integral part of sustainability efforts in industries like manufacturing, recycling, and construction. By separating recyclable materials or waste during the transportation process, conveyor systems help to reduce landfill waste.
By embracing conveyor belt loading systems, businesses can achieve greater efficiency and, at the same time, support their sustainability initiatives, reducing environmental impact.
Optimizing Conveyor Belt Loading Systems for Maximum Performance
To get the most out of your conveyor belt loading system, it’s crucial to focus on optimization. Whether you’re running a high-volume warehouse, a manufacturing plant, or a logistics center, maximizing the performance of your conveyor belt system will lead to smoother operations, lower costs, and higher productivity. Optimization doesn’t just mean increasing speed or efficiency—it also involves improving reliability, reducing wear, enhancing safety, and aligning the system to meet the specific needs of your operation. In this section, we’ll explore how you can optimize your conveyor belt loading system to achieve these goals.
Regular Maintenance Practices for Conveyor Belt Loading Systems
A well-maintained conveyor belt system is essential for ensuring long-term performance. Regular maintenance not only extends the lifespan of the system but also helps prevent costly breakdowns and unexpected downtime. Here are some key maintenance practices to follow:
Inspection of Belts and Components: Regularly inspect the belts for signs of wear, such as fraying, cracking, or stretching. Even small issues with the belt can escalate quickly, leading to a system failure. It’s also important to check the pulleys, rollers, and idlers to make sure they are functioning correctly and free from obstructions.
Lubrication and Tension Adjustment: Conveyor belts rely on proper tension to move efficiently. Over time, the tension in the belt can slacken, reducing the system’s overall performance. Regularly check and adjust the tension according to manufacturer specifications. Additionally, lubricating moving components, such as rollers and bearings, helps reduce friction, preventing wear and improving the system’s overall efficiency.
Cleaning and Debris Removal: Dirt, dust, and debris can accumulate on the conveyor belt, leading to slippage, decreased performance, and even damage. Regularly clean the system and remove any materials that could obstruct the belt’s movement or affect its load-carrying capacity.
Monitoring System Alignment: Misalignment of the belt or rollers can lead to uneven wear and tear, causing the system to operate inefficiently. Ensure that the system is properly aligned and that the belt runs straight to avoid unnecessary friction and damage.
By sticking to a regular maintenance schedule, you can ensure your conveyor belt system continues to perform at its best, avoiding unplanned downtime and extending the life of the equipment.
Upgrading Conveyor Belt Loading Systems for Increased Throughput
As your operations grow, it’s crucial to consider upgrading your conveyor belt loading system to keep pace with higher throughput demands. Increasing the system’s capacity without compromising on performance can be achieved through several strategies:
Increasing Belt Width or Speed: If your current conveyor system is regularly running at full capacity, consider upgrading to a wider or faster belt. A wider belt allows for the transportation of larger loads or more materials at once, while a faster belt can move products or materials more quickly, enhancing throughput.
Automating Load Detection: Implementing sensors or automated load detection systems can optimize the flow of materials. These systems can monitor the load on the conveyor and adjust the speed or direction accordingly, ensuring that the system operates at optimal levels. For example, if there is a heavy load on the belt, the system can slow down to prevent overloading or damage.
Adding Multiple Lines or Diversions: In high-volume environments, it may be necessary to add more conveyors or create diversion systems that redirect goods to different processing areas. Multiple conveyor lines help reduce congestion and allow materials to be handled in parallel, thus increasing overall throughput.
Advanced Controls and Automation: Integration with advanced control systems, such as programmable logic controllers (PLCs), allows for precise management of conveyor belt speeds, timing, and routing. These systems can optimize material flow and improve synchronization with other machines, reducing bottlenecks and delays.
By upgrading your conveyor belt system with these enhancements, you can improve throughput, reduce cycle time, and ensure your system can handle increased demand as your business scales.
Troubleshooting Common Issues in Conveyor Belt Loading Systems
Even the most well-maintained conveyor belt systems can experience issues from time to time. Identifying and addressing problems quickly can help maintain performance and prevent costly delays. Here are some common issues and how to address them:
Slipping Belts: If the belt is slipping or not moving at the required speed, it could be due to a lack of tension, debris on the belt, or worn-out components. To fix this, check the tension on the belt and adjust it accordingly. Clean the belt and rollers to ensure smooth movement, and replace any worn components.
Excessive Vibration: Vibration can be a sign of misalignment, uneven loading, or worn rollers. To fix this, check the alignment of the belt and rollers, and ensure they are securely mounted. Additionally, check the load distribution to make sure it’s even across the entire belt. If necessary, replace or realign the components that are causing the vibrations.
Overheating Motors: Overheated motors can be a result of overloading the system, insufficient lubrication, or dirt buildup. Ensure that the motor is properly maintained, lubricated, and free from debris. If overheating persists, consider upgrading to a higher capacity motor that can handle the increased load or speed demands.
Clogging and Blockages: Conveyor belts, especially those used in food processing or bulk material handling, are prone to clogging and blockages. Regularly clean the system and monitor for any buildup of materials that might cause obstructions. For sticky or wet materials, consider installing self-cleaning belts or upgrading to a conveyor with a specialized surface that can reduce the likelihood of material buildup.
Belt Damage or Wear: If the belt shows signs of damage, it’s crucial to address the issue quickly before it worsens. Replace damaged sections of the belt, and inspect the system regularly for signs of excessive wear. Proper tensioning and alignment can also help prevent premature belt wear.
By staying proactive in troubleshooting and resolving issues as they arise, you can ensure that your conveyor belt system continues to operate smoothly and efficiently without unexpected disruptions.
Training and Empowering Staff for Optimal System Use
Even the best conveyor belt system can underperform if not properly utilized by the operators. Training your staff to use the system effectively is an often-overlooked aspect of optimization. Well-trained personnel can help identify issues early, perform basic maintenance tasks, and ensure the system is being used to its full potential. Here’s how to ensure your team is equipped to maximize the performance of your conveyor belt system:
Operator Training: Ensure that all employees operating the conveyor system are trained on how to use it efficiently and safely. This includes training on proper loading techniques, recognizing signs of potential issues, and how to report problems to maintenance staff.
Regular Updates and Refresher Courses: Conveyor systems and technology evolve over time. Offering regular training sessions helps keep staff updated on new features, maintenance procedures, and best practices for system use.
Promote a Culture of Safety and Efficiency: Encourage workers to take ownership of the system’s performance. Create a culture where safety and efficiency are prioritized, and empower staff to make suggestions for improvement. Regularly engage with staff to identify potential areas for optimization that they may have noticed on the floor.
By investing in your staff’s knowledge and skillset, you ensure that your conveyor belt system is used to its full potential, minimizing inefficiencies and reducing the likelihood of system failure.