Summary:
How Conveyor Belt Tracking Devices Improve Efficiency and Reduce Downtime?
What Are Conveyor Belt Tracking Devices?
Key Benefits of Conveyor Belt Tracking Devices in Reducing Downtime
How Conveyor Belt Tracking Devices Enhance Operational Efficiency?
Best Practices for Implementing Conveyor Belt Tracking Devices in Your Facility
In today’s industrial production, conveyor belt tracking devices are essential tools for ensuring that conveyor systems operate efficiently. These devices continuously monitor the position and condition of the conveyor belt, allowing them to detect any misalignment or deviation. By addressing common belt issues and improving productivity, tracking devices play a crucial role in optimizing operations.
What Are Conveyor Belt Tracking Devices?
Conveyor belt tracking devices are tools designed to monitor and adjust the operation of a conveyor belt system. Their main function is to ensure that the conveyor belt stays on track and does not wander or drift off its path. These devices typically include sensors and adjustment mechanisms that automatically correct the position of the belt if any misalignment occurs, ensuring smooth operation without the need for constant human intervention.
Compared to traditional conveyor systems, those equipped with tracking devices significantly reduce manual adjustments, automatically realigning the belt and preventing downtime caused by misalignment or wear.
How Conveyor Belt Tracking Devices Work
The conveyor belt tracking devices operate through precise sensors and automated adjustment systems. These sensors continuously monitor the position of the conveyor belt, detecting even the slightest deviations. When the sensors identify that the belt is straying from its intended path, the tracking device activates an automatic correction mechanism. This mechanism may include adjustments to rollers, tensioners, or other components to bring the belt back on track.
In addition, many modern tracking devices are equipped with smart features that enable users to analyze the health of the conveyor belt and even predict potential failures. This helps enhance overall system efficiency and minimize downtime by addressing issues before they cause significant problems.
Types of Conveyor Belt Tracking Devices Available
There are various types of conveyor belt tracking devices available on the market, each suited for different work environments and conveyor needs. Common types include:
Mechanical Tracking Devices: These devices use simple mechanical components, such as rollers and adjustment frames, to keep the conveyor belt stable. They are typically used in applications where precision is not the highest priority.
Sensor-Driven Tracking Devices: These devices rely on sensor technology to detect the position of the conveyor belt in real time. They automatically adjust the belt according to feedback from the sensors. These systems are ideal for high-precision and high-demand industrial applications.
Smart Tracking Systems: Combining modern technologies like the Internet of Things (IoT) and Artificial Intelligence (AI), these systems not only track the status of the conveyor belt in real time but also use data analytics to predict potential failures and maintenance needs. They represent the future of industrial automation.
By understanding the different types of tracking devices available, businesses can choose the right one for their specific production requirements, maximizing efficiency while minimizing downtime.
Key Benefits of Conveyor Belt Tracking Devices in Reducing Downtime
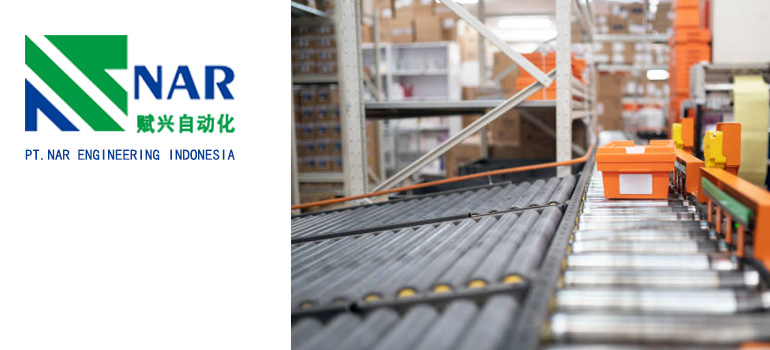
Downtime in manufacturing and production can be costly, both in terms of lost productivity and increased operational costs. One of the most effective ways to minimize downtime is by using conveyor belt tracking devices. These devices are designed to keep conveyor belts aligned and functioning smoothly, addressing issues before they escalate into major problems. Below are the key benefits of implementing conveyor belt tracking devices to reduce downtime:
Minimizing Conveyor Belt Misalignment
One of the primary causes of downtime in conveyor systems is belt misalignment. When a conveyor belt drifts off track, it can cause a variety of issues such as wear and tear on the belt, damage to the rollers, and even more significant system failures if left unaddressed. Conveyor belt tracking devices continuously monitor the belt’s position and make automatic adjustments when misalignment is detected. This proactive approach prevents issues that would otherwise lead to costly delays or repairs.
By keeping the belt properly aligned, these devices not only reduce the risk of system failure but also extend the lifespan of the belt and related components, reducing the frequency of repairs and replacements.
Preventing System Failures and Breakdowns
Conveyor systems are complex, and many factors—such as belt misalignment, uneven load distribution, and excessive friction—can contribute to breakdowns. Tracking devices help prevent these failures by providing real-time feedback on the condition of the conveyor system. If a problem is detected, such as an impending misalignment or excessive tension, the device can automatically adjust settings to prevent further issues from developing.
By addressing small problems early, these devices can prevent larger, more expensive issues down the line, significantly reducing unplanned downtime caused by system failures.
Reducing Maintenance and Repair Costs
Frequent breakdowns and maintenance are a major source of downtime in many industries. Conveyor belt tracking devices help reduce maintenance needs by ensuring that the conveyor belt remains aligned and operates smoothly over time. When belts are properly aligned, wear on other components—such as pulleys, rollers, and motors—is minimized, leading to fewer repairs.
Moreover, many modern tracking devices provide diagnostic data that can alert operators to potential issues before they become serious. This predictive maintenance capability allows maintenance teams to plan and address repairs during scheduled downtimes rather than being forced into costly emergency repairs.
By streamlining maintenance and reducing the frequency of repairs, conveyor belt tracking devices play a crucial role in keeping production lines running smoothly with minimal disruptions.
How Conveyor Belt Tracking Devices Enhance Operational Efficiency
In today’s fast-paced industrial environments, maintaining high operational efficiency is crucial for staying competitive. Conveyor belt tracking devices play an integral role in improving efficiency by ensuring that conveyor systems run smoothly, without interruptions or unnecessary delays. These devices not only address alignment issues but also optimize the overall performance of the conveyor system. Here’s how they enhance operational efficiency:
Improving Conveyor Belt Speed and Consistency
One of the key factors affecting operational efficiency is the speed and consistency of the conveyor system. When a conveyor belt is misaligned or running unevenly, it can cause fluctuations in the speed of material handling, leading to bottlenecks and delays in production. Conveyor belt tracking devices help maintain a consistent path for the belt, ensuring smooth and steady operation.
With a properly aligned conveyor belt, production lines experience less friction and reduced drag, allowing for faster movement of materials and consistent output. This consistency directly contributes to improved throughput and better synchronization with other processes, ultimately boosting overall production efficiency.
Enhancing Load Handling and Transport
Conveyor systems are often used to handle heavy loads across long distances. If the belt drifts or loses its alignment, it can lead to uneven distribution of weight, which may result in the load shifting, causing items to fall or be damaged. Conveyor belt tracking devices ensure that the belt remains properly aligned, even when transporting heavy or irregularly shaped loads.
By keeping the belt stable, these devices improve load handling and ensure that materials are transported smoothly, reducing the risk of product loss or damage. This reliable material flow helps ensure that production lines stay on schedule and that products reach their intended destinations without unnecessary delays or damage.
Boosting Overall Production Capacity
When conveyor systems operate without interruptions, the overall capacity of a production line is significantly increased. Misalignment or downtime caused by conveyor issues can lead to delays in manufacturing or assembly, which impacts the ability to meet production goals. Conveyor belt tracking devices reduce the likelihood of such disruptions by automatically correcting alignment and minimizing the need for manual adjustments.
By preventing these disruptions, these devices help maximize the uptime of conveyor systems, enabling facilities to operate at peak efficiency. This increased uptime allows for higher throughput, faster processing times, and improved productivity, all of which contribute to an increase in overall production capacity.
Reducing Energy Consumption
Another often overlooked benefit of conveyor belt tracking devices is their ability to optimize energy consumption. When a conveyor belt is misaligned or running inefficiently, it requires more energy to move materials due to increased friction and strain on the system. Tracking devices help keep the belt properly aligned, reducing the amount of energy needed to operate the system.
By minimizing energy waste and improving the overall efficiency of the conveyor system, these devices contribute to a more cost-effective and environmentally friendly operation. This energy savings not only cuts operational costs but also aligns with sustainability goals for businesses looking to reduce their environmental footprint.
Best Practices for Implementing Conveyor Belt Tracking Devices in Your Facility
Implementing conveyor belt tracking devices in your facility can significantly improve the efficiency, reliability, and longevity of your conveyor systems. However, to ensure you get the most out of these devices, it’s important to follow best practices for installation, calibration, and ongoing maintenance. Here’s a guide to help you successfully implement conveyor belt tracking devices in your facility:
Choosing the Right Conveyor Belt Tracking Device
The first step in implementing conveyor belt tracking devices is selecting the right type of device for your specific needs. There are various options available, each with its own set of features designed for different applications.
Consider the Environment: The type of materials you’re handling, the operating conditions (such as temperature, humidity, or dust levels), and the physical layout of your conveyor system all play a role in selecting the best tracking device. For example, a heavy-duty sensor-based system may be more suitable for an industrial environment with high load capacities, while a simple mechanical system might work well for lighter operations.
Understand Your Production Requirements: If you need high precision and real-time feedback, opt for sensor-driven or smart tracking systems that offer automatic adjustments and data insights. On the other hand, mechanical tracking devices can be a more cost-effective solution for environments with less stringent requirements.
Compatibility: Ensure the chosen device is compatible with your existing conveyor system. Some tracking devices are designed to work seamlessly with specific belt types or configurations.
Installation and Calibration Tips
Proper installation and calibration of your conveyor belt tracking devices are critical to their performance. Here are some tips for getting it right:
Follow Manufacturer Guidelines: Each tracking device will come with its own installation instructions, so be sure to follow the manufacturer’s recommendations carefully. Proper installation will ensure the device works optimally and provides accurate alignment corrections.
Positioning and Alignment: For sensor-driven devices, precise positioning is essential. Ensure the sensors are placed in the right locations along the conveyor to detect misalignments effectively. The tracking device should be installed where it can monitor the entire length of the conveyor belt, ensuring real-time feedback across the system.
Calibration for Accuracy: Once installed, the device will need to be calibrated. This ensures it can detect deviations accurately and make appropriate adjustments. Calibration should be done according to the manufacturer’s instructions and should include checks for alignment, tension, and tracking sensitivity.
Test the System: After installation and calibration, run the system to check for any inconsistencies in the belt’s alignment. Fine-tune settings if necessary and make sure the system reacts correctly to any misalignment.
Ongoing Monitoring and Maintenance for Optimal Performance
To ensure your conveyor belt tracking devices continue to perform optimally, ongoing monitoring and maintenance are essential.
Regular Inspections: Conduct routine inspections to ensure the tracking devices are functioning as expected. Check for signs of wear and tear on the sensors or mechanical components, and ensure the system is free of debris or obstructions that might affect its operation.
Software Updates: If your tracking system includes software or digital features, make sure to keep the software updated. Manufacturers often release updates that improve functionality, add new features, or fix known issues.
Cleaning and Lubrication: For mechanical tracking devices, regular cleaning and lubrication of moving parts will help prevent friction and ensure smooth operation. Dirt or rust buildup can interfere with the device’s ability to detect misalignment and make necessary adjustments.
Predictive Maintenance: Some advanced conveyor belt tracking devices come with diagnostic features that allow for predictive maintenance. These systems can monitor wear and tear on belts and components and alert you when maintenance is required. Leveraging this feature can help you plan maintenance schedules, reduce unplanned downtime, and extend the life of your conveyor system.
Employee Training and Awareness
To maximize the effectiveness of your conveyor belt tracking devices, it’s important that your team understands how to operate, monitor, and troubleshoot the system. Provide training on:
How to interpret tracking device feedback: Operators should be able to understand alerts and data generated by the system.
Basic troubleshooting techniques: In case of issues, employees should know how to handle minor fixes or when to escalate problems.
Preventive measures: Educate the team on how to avoid common issues that could interfere with the tracking device’s function, such as overloading the conveyor or neglecting proper maintenance.