Summary:
How Conveyor Belt Idlers Improve Efficiency and Reduce Wear in Material Handling
The Role of Conveyor Belt Idlers in Improving Efficiency
Conveyor Belt Idlers: Key Components for Reducing Wear and Tear
Types of Conveyor Belt Idlers and Their Impact on System Performance
Conveyor Belt Idlers and Energy Efficiency in Material Handling
Best Practices for Maintaining Conveyor Belt Idlers to Ensure Longevity
The Role of Conveyor Belt Idlers in Improving Efficiency
Conveyor belt systems are essential in industries like manufacturing, mining, and logistics, where the efficient transportation of materials is key to smooth operations. Conveyor belt idlers are a fundamental component in ensuring these systems operate at peak efficiency. These small yet critical pieces help maintain the smooth movement of the belt, reduce friction, and enhance overall system performance. Let’s explore how conveyor belt idlers contribute to improving efficiency in material handling.
How Conveyor Belt Idlers Support Smooth Movement of Materials
Conveyor belt idlers are positioned at various points along the conveyor system, typically supporting the belt as it moves and carries materials from one point to another. These idlers prevent the belt from sagging or coming into contact with the frame, which helps maintain a consistent flow of materials. By supporting the belt at the correct tension, conveyor belt idlers ensure the smooth operation of the system, minimizing disruptions and delays. This consistent motion allows for more efficient material handling, which translates to better productivity in industrial operations.
Idlers are designed to keep the belt aligned properly, ensuring it doesn’t drift off track. Misalignment can cause bottlenecks, slow down the speed of the system, and lead to increased wear on the belt and other components. By maintaining proper alignment, conveyor belt idlers prevent such issues, allowing the system to run smoothly without interruptions, thus improving overall throughput.
Reducing Friction and Enhancing Speed with Conveyor Belt Idlers
One of the primary ways conveyor belt idlers enhance efficiency is by reducing friction between the belt and the conveyor system. The rollers in the idlers create a smooth surface for the belt to glide over, which lowers the amount of energy needed to move materials. By minimizing friction, conveyor belt idlers help the system operate with less power, leading to increased efficiency in energy consumption.
In addition to reducing friction, conveyor belt idlers also help maintain the proper tension on the belt. When the belt is too loose, it can slow down or even stop, creating a drag on the system. On the other hand, excessive tension can cause unnecessary wear on the belt and the idlers. Properly installed and maintained idlers ensure the belt moves at the right speed, minimizing energy consumption and maximizing operational efficiency.
Optimizing Conveyor Belt System Performance through Proper Idler Alignment
For conveyor systems to work efficiently, the belt needs to be aligned correctly and run without obstacles. Conveyor belt idlers play a crucial role in this alignment process. They guide the belt and prevent it from veering off course, which could lead to inefficient operation and potential damage to the system. Misaligned belts often experience uneven wear, which can lead to costly repairs and downtime.
With well-aligned idlers, conveyor systems can function at their full potential, reducing friction, wear, and the chances of unexpected failures. Proper idler alignment ensures that the belt runs smoothly and consistently, contributing to a higher level of productivity and efficiency in the material handling process. When idlers are correctly positioned, the entire system operates as it was designed, with fewer interruptions and less wear on other critical components.
Conveyor Belt Idlers: Key Components for Reducing Wear and Tear
Conveyor belt systems are a backbone of modern material handling, transporting bulk goods and materials across industries such as mining, agriculture, and manufacturing. However, like any mechanical system, these belts experience wear and tear over time. Conveyor belt idlers are essential components that help mitigate these issues by reducing the stress placed on the belt, the rollers, and other system parts. By playing a crucial role in managing wear, idlers help prolong the lifespan of conveyor systems, decrease maintenance costs, and increase operational efficiency.
Preventing Belt Slippage and Deformation with Properly Installed Idlers
Belt slippage and deformation are common problems that arise when conveyor belts are subjected to heavy loads or excessive tension. Over time, these issues can lead to poor performance, irregular material transport, and even system failure. Conveyor belt idlers help prevent these problems by maintaining proper tension and alignment.
Idlers support the weight of the belt and the materials it carries, ensuring the belt remains taut and correctly positioned. When the idlers are properly installed, they prevent the belt from stretching or sagging, which can lead to slippage. By keeping the belt at the correct tension, idlers also reduce the risk of deformation, which can occur when the belt becomes too loose or too tight. This helps maintain consistent material flow and reduces the need for frequent adjustments or replacements of the belt.
How Conveyor Belt Idlers Distribute Weight and Minimize Stress
Conveyor belts often carry heavy loads, and the constant movement can cause significant wear on the belt if the load is not properly distributed. Conveyor belt idlers play a vital role in evenly distributing the weight across the length of the belt. By supporting the belt at various points, idlers help to ensure that the pressure is spread evenly, reducing the strain on any one part of the belt.
This even weight distribution minimizes the risk of localized damage, such as tearing or excessive wear in specific areas of the belt. Without idlers, the pressure from heavy loads would focus on a few areas, increasing the likelihood of wear and shortening the life of the conveyor system. With idlers working to distribute the load, the wear is more evenly spread out, which helps to extend the belt’s service life and reduce the frequency of replacements or repairs.
The Impact of Conveyor Belt Idlers on Prolonging Belt and Component Lifespan
The longevity of a conveyor belt is largely dependent on how well the system is maintained and how evenly forces are applied to it during operation. Conveyor belt idlers help minimize the impact of stress and friction on both the belt and the other system components, such as the pulleys and motors. When idlers are functioning properly, they ensure that the belt remains in optimal condition by reducing unnecessary friction that would otherwise cause excessive wear.
Additionally, idlers help protect the entire conveyor system from premature failure. By maintaining the correct belt alignment, preventing slippage, and evenly distributing weight, they reduce the likelihood of damage to the belt or other components. Over time, this leads to fewer system breakdowns and costly repairs, allowing businesses to maintain consistent operations and reduce downtime.
Regular inspection and maintenance of idlers are crucial to keeping them in good working order. Over time, the rollers in the idlers can wear down, and the bearings can become damaged, which can negatively affect their performance. Properly maintained idlers will continue to reduce wear on the belt and other parts of the conveyor system, keeping everything running smoothly for longer periods.
Conveyor belt idlers play a vital role in the longevity and efficiency of conveyor systems. By preventing slippage, distributing weight evenly, and minimizing the stress placed on the belt and other components, they help reduce wear and tear. This not only prolongs the life of the conveyor system but also minimizes downtime and maintenance costs, making idlers a key investment for any material handling operation.
Types of Conveyor Belt Idlers and Their Impact on System Performance
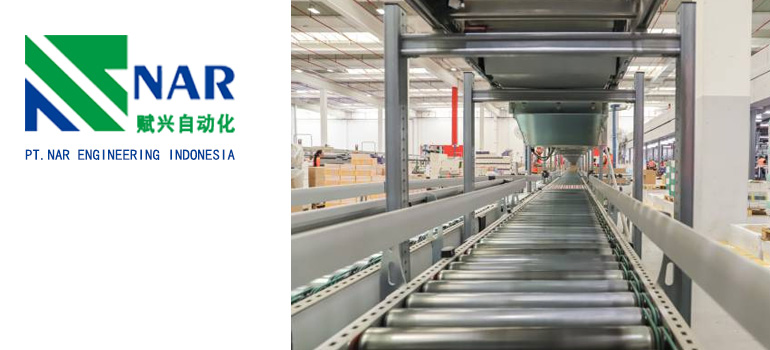
Conveyor belt idlers are integral components of any conveyor system, and they come in a variety of types, each designed to serve a specific function in enhancing performance and ensuring longevity. The type of idler used can significantly influence the efficiency, durability, and operational cost of the entire conveyor system. Understanding the different types of idlers and their unique roles is essential for selecting the right ones for a particular application. In this section, we’ll explore the various types of conveyor belt idlers and how each one impacts the overall system performance.
Carrying Idlers vs. Return Idlers: What’s the Difference?
When discussing conveyor belt idlers, it’s essential to distinguish between carrying idlers and return idlers, as each type serves a distinct role in supporting the conveyor belt.
Carrying Idlers: These are the most common type of idlers and are used to support the weight of the material being transported along the conveyor belt. Carrying idlers are typically placed underneath the conveyor belt, at regular intervals, and they are designed to bear the load of both the belt and the material. Their role is crucial in maintaining the tension of the belt and ensuring it moves smoothly across the conveyor system.
Return Idlers: Located on the underside of the conveyor belt, return idlers support the belt as it moves back to its starting point after it has dropped off the material. Unlike carrying idlers, return idlers do not carry material but ensure that the belt remains aligned and doesn’t sag. By maintaining proper tension on the return journey, these idlers help reduce wear and prevent any misalignment, ensuring that the belt stays on track throughout its entire cycle.
Both types of idlers contribute to the overall efficiency of the system by ensuring smooth, continuous movement of the belt and preventing unnecessary wear. The key difference between them lies in their specific role in either supporting the load (carrying idlers) or maintaining belt alignment (return idlers).
Impact of Idler Materials on Durability and Maintenance
The material used in conveyor belt idlers significantly affects their durability and maintenance requirements. Idlers can be made from various materials, each offering unique benefits depending on the environment and the materials being handled.
Steel Idlers: Steel is one of the most commonly used materials for idlers due to its strength, durability, and ability to withstand heavy loads and rough conditions. Steel idlers are particularly suited for industries such as mining and heavy manufacturing, where the conveyor system is expected to handle large amounts of material and operate in demanding environments. They are resistant to abrasion and can last for years, but they may require more maintenance due to the wear on the bearings and seals over time.
Polymer Idlers: For less demanding applications or where noise reduction is essential, polymer idlers made from plastic materials such as polyurethane or nylon are often used. These idlers are lighter, more resistant to corrosion, and generate less noise, making them ideal for food processing or warehouse systems where hygiene and a quieter operation are priorities. While they may not have the same weight capacity as steel idlers, they offer the benefit of lower maintenance requirements.
Rubber-Coated Idlers: In environments where noise reduction, shock absorption, and non-marking properties are necessary, rubber-coated idlers are commonly used. The rubber coating helps absorb the impact of the material being transported, reducing vibrations and minimizing the risk of damage to both the conveyor system and the materials being moved. These idlers are typically used in applications where the materials are fragile or sensitive to impact, such as in the transportation of delicate electronics or packaged goods.
Each material offers a distinct advantage depending on the specific needs of the application, and choosing the right material for your idlers is essential to optimizing system performance and minimizing long-term maintenance costs.
Choosing the Right Idler Type for Specific Conveyor Belt Systems
The performance of a conveyor system largely depends on selecting the right type of idlers for the specific application. Several factors must be taken into consideration when choosing idlers, including the type of material being transported, the conveyor’s operating environment, and the desired system longevity.
Load Considerations: For systems that carry heavy or abrasive materials, such as mining or gravel transport, robust carrying idlers with strong steel construction are often necessary. For lighter or less abrasive materials, lighter idlers made from polymers or rubber may be sufficient.
Environmental Factors: Conveyor systems operating in harsh environments, such as high humidity, extreme temperatures, or exposure to chemicals, require idlers made from materials that can withstand those conditions. Stainless steel or specially coated idlers may be required to prevent rust and corrosion in such environments.
Speed and Efficiency: For high-speed conveyor systems, idlers with low friction and high rotational capacity are essential to maintaining smooth movement and reducing energy consumption. Specially designed high-speed idlers may include features such as sealed bearings and specific roller coatings to reduce resistance and increase efficiency.
Maintenance and Longevity: Selecting the right idlers can also have a direct impact on long-term maintenance costs. Idlers that require frequent maintenance or have a shorter lifespan can increase operating costs over time. Opting for durable, low-maintenance idlers, such as those made from corrosion-resistant materials or with self-lubricating bearings, can significantly reduce the need for downtime and costly repairs.
The Role of Special Idler Types in Specialized Applications
In some industries, specialized conveyor belt systems require custom idler types to ensure optimal performance. These include:
Impact Idlers: Used in areas where heavy materials are dropped onto the conveyor belt, these idlers have extra padding or cushioning to absorb the shock and reduce damage to both the belt and the system. They are typically found in material handling systems where large chunks of material are being transferred.
Troughing Idlers: These idlers have rollers that are positioned at an angle, creating a trough-like structure that helps hold and contain bulk materials, preventing spillage. They are commonly used in applications involving bulk commodities like coal, sand, or grain.
Training Idlers: These are specifically designed to help correct misalignment in the conveyor system. Misaligned belts can cause uneven wear, tracking problems, and even premature failure of the belt. Training idlers help keep the belt centered and aligned, ensuring smooth operation and preventing costly downtime.
Choosing the right conveyor belt idlers is crucial for optimizing system performance, reducing maintenance, and ensuring the longevity of the conveyor system. Understanding the types of idlers, their materials, and their specific roles in the conveyor system helps businesses make informed decisions. By selecting the appropriate idlers based on factors like load, environment, and material type, companies can enhance the efficiency, durability, and cost-effectiveness of their material handling systems.
Conveyor Belt Idlers and Energy Efficiency in Material Handling
In today’s industrial environments, where material handling systems are integral to operations, energy efficiency is a critical factor in reducing operational costs and improving environmental sustainability. Conveyor belt idlers play a significant yet often overlooked role in optimizing energy use. These components, essential for ensuring smooth operation, not only reduce wear and tear but also contribute to minimizing energy consumption. In this section, we’ll explore how conveyor belt idlers impact energy efficiency and why selecting the right idlers can result in significant cost savings over time.
Reducing Power Consumption with Properly Designed Conveyor Belt Idlers
One of the most notable ways that conveyor belt idlers contribute to energy efficiency is by minimizing the friction between the conveyor belt and the system’s structure. Friction is one of the primary factors that leads to excessive energy consumption in any conveyor system. When friction is high, more energy is required to move the belt, resulting in higher electricity costs and increased wear on both the belt and other components.
By using well-designed idlers, the contact between the belt and the rollers is optimized, ensuring that the belt moves smoothly with minimal resistance. Low-friction idlers, often made from materials like nylon or polymer, can help further reduce resistance, allowing the system to run with less energy. High-quality bearings in the idlers also reduce friction and the need for lubrication, which further improves efficiency.
Idlers that are designed to reduce friction are particularly beneficial for systems operating under high loads or at high speeds. In such cases, even small reductions in friction can lead to noticeable energy savings over time. With less energy required to move the materials, the overall operating cost of the conveyor system decreases, which has a significant positive impact on energy efficiency.
The Relationship Between Conveyor Belt Idlers and Energy Savings
The relationship between conveyor belt idlers and energy savings can be understood through the concept of belt tension. Proper tensioning is critical to the performance of a conveyor system. If the belt is too tight, it will create unnecessary resistance, requiring more energy to move. Conversely, if the belt is too loose, it can slip, causing energy losses and potential damage to the system.
Idlers play a pivotal role in maintaining the correct tension on the conveyor belt. By ensuring that the belt is neither too tight nor too loose, idlers help balance the tension across the system, ensuring smooth and efficient operation. This prevents unnecessary energy expenditure, as the belt operates within an optimal range of tension.
Additionally, the correct idler selection can help in maintaining the belt’s alignment. Misalignment can cause the system to work harder, increasing the energy needed to move materials. Idlers, particularly training idlers, keep the belt centered, reducing the chances of misalignment and ensuring that the conveyor system operates smoothly and efficiently.
Why High-Quality Idlers Can Lower Long-Term Operational Costs
Investing in high-quality idlers can provide substantial long-term savings in terms of both energy and maintenance costs. While inexpensive or low-quality idlers may seem cost-effective in the short term, they can lead to higher operational costs over time. Poorly designed or low-grade idlers often require more frequent maintenance, which results in unplanned downtime, repair expenses, and lost productivity.
High-quality idlers, on the other hand, are designed for durability and performance. By reducing friction and wear, they contribute to energy savings and reduce the frequency of repairs. These idlers are made from durable materials and equipped with high-quality bearings that minimize the need for lubrication and reduce friction, both of which contribute to better energy efficiency.
Additionally, using the right idlers for specific applications can enhance energy efficiency. For example, in systems that handle heavy loads or operate at high speeds, selecting idlers that are specifically designed for such conditions can further reduce energy consumption and increase the longevity of the system.
The Role of Conveyor Belt Idlers in Minimizing Vibration and Energy Loss
Vibrations in conveyor systems can lead to significant energy loss, especially in high-speed or high-load operations. These vibrations not only waste energy but also contribute to increased wear on the conveyor belt and other components. Vibration-dampening idlers are specifically designed to reduce these vibrations by absorbing shock and minimizing movement that can lead to unnecessary energy use.
Idlers with shock-absorbing features help to maintain belt stability and prevent the system from operating inefficiently. By stabilizing the belt and reducing excessive motion, these idlers ensure that the conveyor system runs smoothly with less energy being diverted into compensating for vibrations. The result is a more energy-efficient system that reduces energy loss and improves performance.
The Environmental Impact of Energy-Efficient Conveyor Belt Idlers
In addition to the financial benefits, energy-efficient conveyor belt systems also have a positive environmental impact. By reducing energy consumption, these systems help decrease the overall carbon footprint of a manufacturing or material handling operation. For businesses that are working towards sustainability goals or adhering to environmental regulations, the implementation of energy-efficient idlers is a valuable strategy.
The adoption of energy-efficient conveyor systems, including high-performance idlers, aligns with global efforts to reduce energy consumption and minimize environmental damage. As energy costs rise and environmental regulations become stricter, companies can achieve a competitive advantage by investing in energy-efficient technology that not only lowers operating costs but also contributes to their sustainability initiatives.
Conveyor belt idlers play a critical role in improving energy efficiency in material handling systems. By reducing friction, maintaining proper belt tension, and minimizing vibrations, idlers help minimize energy consumption, which can lead to significant cost savings over time. The selection of high-quality idlers, designed for specific applications and conditions, ensures the system runs smoothly and efficiently. For companies aiming to reduce operational costs and their environmental footprint, investing in energy-efficient idlers is an essential step toward achieving these goals.
Best Practices for Maintaining Conveyor Belt Idlers to Ensure Longevity
Conveyor belt systems are essential in many industries for transporting materials efficiently. However, like any mechanical system, conveyor belts and their components experience wear and tear over time. Conveyor belt idlers, despite being designed to handle significant stress, require regular maintenance to ensure their longevity and optimize system performance. Well-maintained idlers reduce downtime, prevent costly repairs, and increase the overall lifespan of the entire conveyor system. In this section, we will explore the best practices for maintaining conveyor belt idlers to ensure they remain in good working condition for years to come.
Regular Inspection and Monitoring of Idlers
The foundation of effective idler maintenance begins with regular inspection. Frequent checks help identify early signs of wear, damage, or misalignment before they lead to more serious issues. Inspections should focus on the following areas:
- Roller Condition: Ensure that the rollers of the idlers are rotating freely without resistance. Any sign of stiffness or grinding noise could indicate that the bearings are damaged or worn out.
- Alignment: Misaligned idlers can cause undue stress on the conveyor belt, leading to increased friction, uneven wear, and premature failure. Regularly check that the idlers are aligned properly to keep the belt running straight.
- Surface Wear: Inspect the surfaces of the rollers for signs of abrasions, pitting, or grooves, which can cause the belt to wear unevenly. Replacing worn-out rollers is essential to maintaining optimal system efficiency.
- Seals and Bearings: Look for cracks, dirt buildup, or signs of leakage around the idler bearings and seals. Damaged seals can let in contaminants like dirt and moisture, which can deteriorate the bearings and cause the idlers to fail prematurely.
Using specialized equipment such as infrared thermography, vibration analysis, or ultrasonic sensors can help detect issues that may not be immediately visible. Keeping a detailed maintenance log will allow you to track changes over time and make informed decisions about when to replace parts.
Proper Lubrication of Idler Bearings
The bearings within the conveyor belt idlers are critical to smooth operation and low friction. Without proper lubrication, the bearings can wear out prematurely, resulting in increased friction, heat generation, and energy consumption. To ensure the longevity of idlers, it is important to:
- Use the Right Lubricant: The type of lubricant used should match the environmental conditions in which the conveyor system operates. For example, extreme temperatures, moisture, or dust may require special lubricants or sealed bearings.
- Lubricate Regularly: Bearings should be lubricated at regular intervals, as per the manufacturer’s recommendations. Over-lubricating can attract dirt, while under-lubricating leads to inadequate protection against friction and wear.
- Avoid Contaminants: When applying lubricant, ensure that no dirt or contaminants come into contact with the bearing components. Contaminants can wear down the bearings and cause premature failure.
By maintaining proper lubrication, idlers can operate smoothly and with less friction, reducing energy consumption and improving the efficiency of the entire conveyor system.
Adjusting Idler Tension and Alignment
The proper tension and alignment of conveyor belt idlers are essential for minimizing wear and ensuring the smooth operation of the system. Misalignment or incorrect tension can lead to belt slippage, uneven wear, and increased energy consumption. To optimize tension and alignment:
- Monitor Belt Tension: Ensure the belt is neither too tight nor too loose. Excessive tension can cause stress on the idlers, while too little tension may cause the belt to slip and misalign. Regularly check and adjust the tension to keep the belt running at optimal efficiency.
- Align Idlers Properly: Idlers should be positioned correctly to keep the belt straight and prevent unnecessary friction. Misalignment not only causes uneven wear on the belt but also leads to higher energy consumption. Make sure the idlers are placed at regular intervals, and adjust any that may have shifted over time.
A conveyor system that is well-aligned and properly tensioned will have a longer operational life and reduce the frequency of costly repairs.
Replacing Worn or Damaged Idlers
Even with regular inspection and maintenance, some idlers will eventually wear out and need replacement. Worn or damaged idlers can negatively affect the entire system, leading to more extensive damage to the belt and other components. To prevent this:
- Check for Excessive Wear: If an idler’s roller is worn down, cracked, or no longer rotating smoothly, it should be replaced immediately. Likewise, if the seals or bearings are damaged, replacing the entire idler might be necessary to ensure smooth operation.
- Scheduled Replacements: Rather than waiting for an idler to fail completely, consider replacing parts that show early signs of wear as part of a scheduled maintenance program. This reduces the risk of unexpected downtime and costly repairs.
Proactively replacing worn components helps maintain system efficiency and avoids the cascading effect of damage to other parts of the conveyor system.
Preventing Contaminants from Affecting Idlers
Idlers can be vulnerable to damage from external contaminants such as dirt, water, dust, and debris. These contaminants can increase wear on both the bearings and the rollers, leading to performance degradation and shortened lifespan. To prevent damage:
- Install Seals and Covers: Many conveyor systems come equipped with seals or covers that protect the idlers from contaminants. Regularly inspect these seals to ensure they are intact and replace them when necessary.
- Use Dust and Water Protection: In environments with high levels of dust, dirt, or moisture, consider using sealed or specially coated idlers that can better withstand these conditions.
- Clean the System: Periodically clean the conveyor system, removing any built-up debris or foreign objects that might interfere with the operation of the idlers.
Keeping contaminants at bay is key to maintaining the longevity of conveyor belt idlers and ensuring smooth system operation.
Monitoring Environmental Conditions
Environmental factors play a significant role in the wear and tear of conveyor belt idlers. Factors like extreme temperatures, humidity, or exposure to chemicals can degrade the idlers and shorten their lifespan. To mitigate these effects:
- Adapt to the Environment: Choose idlers that are specifically designed for the operating environment. For instance, if the conveyor system operates in a corrosive environment, select idlers made from corrosion-resistant materials like stainless steel.
- Adjust Maintenance Schedules: Harsh environmental conditions may require more frequent inspections and maintenance to ensure the idlers remain in good condition. Account for these conditions in your maintenance program.
Proper maintenance of conveyor belt idlers is essential to ensuring their longevity and optimizing the performance of the entire conveyor system. By following best practices such as regular inspections, proper lubrication, ensuring correct alignment and tension, replacing worn-out parts, preventing contamination, and adapting to environmental conditions, businesses can minimize downtime, reduce operating costs, and extend the life of their equipment. Implementing these practices will not only enhance the efficiency of the material handling process but also ensure a more reliable and cost-effective conveyor system.