Summary:
From Manual to Automatic: Transforming Processes with Conveyor Controllers
Understanding the Role of Conveyor Controllers
Evolution from Manual to Automatic Processes
Benefits of Implementing Conveyor Controllers
Understanding the Role of Conveyor Controllers
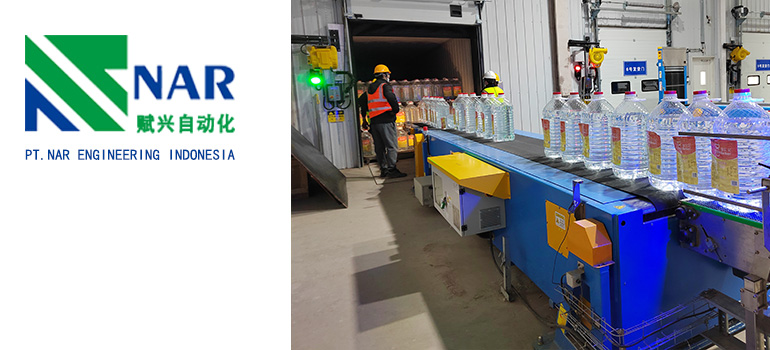
Understanding the role of Conveyor Controllers is like deciphering the language of efficiency in the industrial landscape. These sophisticated devices play a pivotal role in orchestrating the intricate dance of materials and machinery, ensuring a harmonious and streamlined workflow. Let’s delve into the multifaceted aspects that define their significance:
Enhancing Precision and Coordination
Conveyor Controllers act as the precision maestros of the manufacturing orchestra. They synchronize the movements of conveyor belts, ensuring materials traverse the production line with impeccable accuracy. This level of coordination minimizes errors, reduces downtime, and optimizes the overall efficiency of the process.
Enabling Seamless Automation
At the core of their role is the facilitation of automation. Conveyor Controllers empower industries to transition from labor-intensive, manual operations to automated, technology-driven processes. By seamlessly integrating with other automation systems, they contribute to creating a connected and intelligent manufacturing environment.
Adapting to Varied Work Environments
The adaptability of Conveyor Controllers is another key aspect. Whether in automotive assembly lines, food processing units, or e-commerce warehouses, these controllers can be tailored to suit diverse industry requirements. Their versatility makes them indispensable in addressing the unique challenges posed by different work environments.
Monitoring and Optimization
Beyond coordination, Conveyor Controllers serve as vigilant overseers of the production landscape. They incorporate monitoring mechanisms that enable real-time data collection. This data is then analyzed to identify bottlenecks, optimize material flow, and enhance the overall operational efficiency of the system.
Improving Safety Standards
Safety is paramount in industrial settings, and Conveyor Controllers contribute significantly to this aspect. By implementing advanced safety features such as emergency stop protocols and obstacle detection, they ensure a secure working environment for both machines and personnel.
In essence, understanding the role of Conveyor Controllers goes beyond recognizing them as mere components. It involves acknowledging them as transformative agents reshaping the dynamics of modern manufacturing. Their contribution to precision, automation, adaptability, monitoring, and safety positions them as indispensable assets in the pursuit of operational excellence.
Evolution from Manual to Automatic Processes
The evolution from manual to automatic processes marks a transformative journey in the landscape of industrial operations. It’s a narrative of progress, efficiency, and technological advancement. Let’s unravel the key milestones and insights into this evolution:
Embracing Automation: A Paradigm Shift
The journey begins with a paradigm shift from reliance on manual labor to the adoption of automation. This shift is fueled by the quest for increased efficiency, reduced human errors, and the need to meet growing demands. Conveyor Controllers emerge as protagonists in this narrative, serving as the catalysts that bridge the gap between the manual and the automated.
Rise of Mechanization
The early stages witness the rise of mechanization, where basic machinery is introduced to complement human efforts. Conveyor systems enter the scene, streamlining material movement and laying the groundwork for more sophisticated automated processes. This phase sets the foundation for the broader automation revolution.
Conveyor Controllers: Architects of Automation
As industries recognize the limitations of manual processes, Conveyor Controllers emerge as the architects of automation. Their ability to orchestrate the synchronized movement of materials becomes instrumental in shaping automated workflows. This transition not only enhances efficiency but also opens doors to new possibilities in production capabilities.
Technological Milestones in Automation
Advancements in technology become the driving force behind the evolution. From the advent of programmable logic controllers (PLCs) to the integration of sophisticated sensors and artificial intelligence, each milestone propels the automation journey forward. Conveyor Controllers evolve in tandem with these technologies, becoming more intelligent and adaptable.
Programmable Logic Controllers (PLCs)
The introduction of PLCs revolutionizes automation by providing a flexible and programmable solution. Conveyor Controllers leverage PLC technology to offer dynamic control over conveyor systems, enabling customized and precise automation according to specific manufacturing needs.
Integration of Sensors and IoT
The infusion of sensors and the Internet of Things (IoT) further enhances automation capabilities. Conveyor Controllers, equipped with sensors, gain the ability to collect real-time data, monitor performance, and respond dynamically to changing conditions. This connectivity transforms them into intelligent hubs within the automated ecosystem.
Impact on Operational Efficiency and Beyond
The evolution culminates in a significant impact on operational efficiency. Automated processes driven by Conveyor Controllers lead to faster production cycles, reduced operational costs, and improved product quality. Beyond efficiency, the shift towards automation also addresses challenges related to scalability, allowing industries to meet increasing demands seamlessly.
Accelerated Production Cycles
Automated processes, guided by Conveyor Controllers, significantly accelerate production cycles. The consistent and precise movement of materials optimizes throughput, enabling industries to produce more in less time.
Cost Reduction and Resource Optimization
Automation not only boosts efficiency but also contributes to cost reduction. Conveyor Controllers play a crucial role in resource optimization by minimizing waste, reducing labor costs, and ensuring energy-efficient operation.
Quality Improvement
Automated processes under the guidance of Conveyor Controllers enhance product quality. The meticulous control and monitoring capabilities minimize errors, resulting in products that meet higher quality standards.
Future Horizons: Beyond Automation
As we reflect on the evolution from manual to automatic processes, it becomes evident that this journey is ongoing. The future holds promises of further innovations, where Conveyor Controllers continue to evolve alongside emerging technologies like artificial intelligence, machine learning, and robotics. The narrative of evolution persists, with each chapter bringing new possibilities and efficiencies to the forefront.
Benefits of Implementing Conveyor Controllers
The implementation of Conveyor Controllers introduces a myriad of benefits to industrial processes, revolutionizing the way operations are managed. Let’s explore these advantages and understand how Conveyor Controllers contribute to enhancing efficiency, safety, and overall productivity:
Increased Efficiency and Productivity
Streamlined Material Flow
Conveyor Controllers optimize material flow with precision, minimizing delays and bottlenecks. This streamlined movement accelerates production cycles, leading to increased efficiency and higher productivity levels.
Continuous Operations
Conveyor Controllers enable continuous operations by automating material handling. With seamless transitions between production stages, downtime is reduced, and industries can maintain a consistent workflow for extended periods.
Cost Savings and Resource Optimization
Labor Cost Reduction
Automation facilitated by Conveyor Controllers reduces the dependency on manual labor. This not only cuts down labor costs but also mitigates the impact of factors such as fatigue and human errors on operational efficiency.
Energy-Efficient Operation
Conveyor Controllers contribute to energy efficiency by optimizing the use of resources. They can be programmed to operate at varying speeds, ensuring energy is utilized only when necessary and reducing overall energy consumption.
Enhanced Safety Measures in Operations
Accident Prevention
Conveyor Controllers incorporate advanced safety features, such as emergency stop protocols and obstacle detection. These measures enhance workplace safety by minimizing the risk of accidents and ensuring a secure working environment for both machinery and personnel.
Ergonomic Benefits
Automation through Conveyor Controllers reduces the need for manual material handling, decreasing the risk of injuries related to lifting and repetitive tasks. This ergonomic improvement contributes to a healthier and safer working environment.
Flexibility and Adaptability
Customization for Varied Applications
Conveyor Controllers offer a high degree of customization, allowing industries to tailor their operations according to specific needs. Whether in manufacturing, logistics, or other sectors, the adaptability of these controllers makes them suitable for a wide range of applications.
Scalability
Industries experiencing growth can easily scale their operations with Conveyor Controllers. The modular nature of these systems allows for the seamless integration of additional components, accommodating increased production demands without major overhauls.
Real-time Monitoring and Analysis
Data-driven Decision Making
Conveyor Controllers equipped with sensors enable real-time monitoring of operational parameters. The collected data facilitates informed decision-making, helping industries identify areas for improvement, optimize processes, and enhance overall efficiency.
Predictive Maintenance
The ability to monitor equipment health in real-time enables predictive maintenance. Conveyor Controllers can detect potential issues before they escalate, minimizing downtime and reducing the overall maintenance costs.
In conclusion, the implementation of Conveyor Controllers goes beyond automation; it represents a strategic investment in efficiency, safety, and adaptability. The benefits extend across various aspects of industrial operations, positioning these controllers as indispensable tools in the pursuit of operational excellence.