Summary:
All you need to know about Robotic palletising
What is Robotic palletising?
Benefits of robotic palletising
Applications of Robotic Palletising in Manufacturing
Factors to Consider in Selecting a Material Conveyor System
What is Robotic palletising?
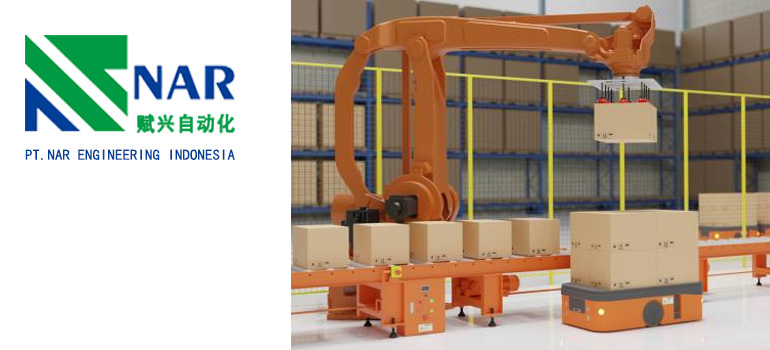
Robotic Palletising refers to the automated process of stacking or arranging products onto pallets using robotic arms or machinery. This advanced industrial automation technique has gained prominence in manufacturing and warehouse operations, streamlining the palletising process and enhancing overall efficiency.
In a typical robotic palletising system, a robotic arm equipped with specialized end-of-arm tools is programmed to pick up individual items or boxes from a conveyor belt or production line and strategically place them onto a pallet. The programming is precise, allowing the robot to arrange items according to a predetermined pattern or specific requirements.
Key components of a robotic palletising system include:
Robotic Arm: The core element of the system, the robotic arm is responsible for the actual handling and placement of items onto the pallet.
End-of-Arm Tooling: Specialized grippers or tools attached to the robotic arm that allow for the secure and precise handling of various types of products.
Vision Systems: Cameras or sensors that enable the robot to “see” and accurately locate items for picking and placing.
Programming and Control Software: The software that instructs the robot on how to perform the palletising task, including the specific arrangement of products and the coordination of movements.
Benefits of robotic palletising
The adoption of robotic palletising in manufacturing and logistics comes with various benefits, contributing to increased efficiency, cost-effectiveness, and overall operational improvements. Here are key advantages of implementing robotic palletising systems:
Efficiency and Speed:
Increased Throughput: Robotic palletising systems operate at a high speed, allowing for faster palletising compared to manual methods.
Continuous Operation: Robots can work continuously without breaks, leading to a consistent and uninterrupted production flow.
Accuracy and Precision:
Reduced Errors: Robotic systems provide precise control over the placement of items on pallets, minimizing the risk of errors associated with manual handling.
Consistent Patterns: The ability to program robots for specific palletising patterns ensures uniformity in packaging and stacking.
Labor Cost Savings:
Reduced Manual Labor: Automation of palletising tasks reduces the need for manual labor, leading to cost savings in wages and associated expenses.
Redeployment of Labor: Employees can be redeployed to more skilled and value-added tasks, enhancing workforce productivity.
Flexibility:
Adaptability to Varied Products: Robotic palletising systems can be easily reprogrammed to handle different product types, sizes, and packaging configurations.
Quick Changeovers: Rapid reconfiguration allows for efficient transition between different products or production runs.
Space Optimization:
Maximized Storage: Robots can optimize pallet stacking, making the best use of available storage space in warehouses and distribution centers.
High-Density Pallets: Efficient stacking patterns can result in higher pallet density, reducing the overall storage footprint.
Safety Improvements:
Reduced Workplace Injuries: Automation of palletising tasks minimizes the physical strain on workers and lowers the risk of injuries associated with manual handling.
Enhanced Workplace Safety: Robotic systems are designed with safety features to prevent accidents and ensure a secure working environment.
Increased Production Capacity:
24/7 Operation: Robotic palletising systems can operate round the clock, contributing to increased production capacity and overall output.
Scalability: These systems can scale easily to accommodate growing production demands.
Data and Analytics:
Data Collection: Integration with analytics tools allows for data collection on palletising performance, contributing to process optimization and continuous improvement.
Performance Monitoring: Real-time monitoring of robotic palletising operations enables quick identification and resolution of issues.
Quality Control:
Consistent Quality: Robotic systems ensure consistent product placement, reducing the likelihood of damaged goods and improving overall product quality.
Traceability: Tracking capabilities in robotic systems enhance traceability, aiding in quality control and compliance.
Competitive Advantage:
Technological Edge: Adopting robotic palletising technology provides companies with a competitive edge by staying at the forefront of technological advancements in manufacturing and logistics.
Customer Satisfaction: Efficient and error-free palletising contributes to timely deliveries and customer satisfaction.
The benefits of robotic palletising make it a valuable investment for businesses looking to enhance their operational efficiency, reduce costs, and stay competitive in a rapidly evolving industrial landscape.
Applications of Robotic Palletising in Manufacturing
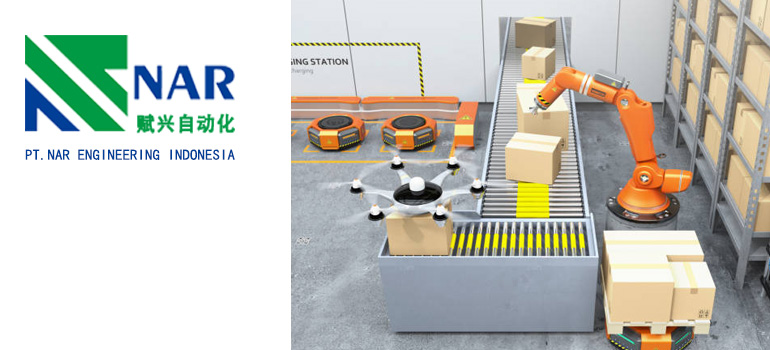
Automotive Industry: Delve into how automotive manufacturers use robotic palletising to streamline the packing and shipping of automotive parts.
Food and Beverage: Examine how the food and beverage industry benefits from the hygienic and precise nature of robotic palletising in packaging and palletizing goods.
Pharmaceuticals: Discuss how the pharmaceutical industry leverages robotic palletising for accurate and compliant stacking of medical products.
Consumer Electronics: Explore how manufacturers of electronics utilize robotic palletising to handle delicate and diverse product types efficiently.
By exploring the practical applications and success stories, manufacturers can gain insights into the versatility and adaptability of robotic palletising in diverse
Factors to Consider in Selecting a Material Conveyor System
Consider the nature of the materials being conveyed and how well they align with the characteristics of different conveyor types.
Bulk Density: Address the importance of selecting a conveyor system that can handle the bulk density of the materials without causing inefficiencies or damage.
Abrasiveness: Discuss how abrasive materials may require specific conveyor types and features to prolong the equipment’s lifespan.
Moisture Content: Explore the impact of moisture on materials and the need for conveyor systems that can handle varying moisture levels.
Maybe you are interested in the following: From Manual to Automatic: Transforming Processes with Conveyor Controllers