Summary:
Why Belt Conveyors Are Essential for Packaging Automation in Modern Factories?
Introduction to Belt Conveyors for Packaging in Modern Factories
How Belt Conveyors Improve Efficiency in Packaging Systems?
The Impact of Belt Conveyor for Packaging on Product Quality
Introduction to Belt Conveyors for Packaging in Modern Factories
In modern factories, belt conveyors have become an essential part of packaging automation. These conveyor systems not only enhance production efficiency but also play a crucial role in maintaining packaging consistency and quality. With their efficient material handling capabilities, belt conveyors seamlessly connect various packaging stages on high-speed production lines, helping factories achieve automated workflows, reduce manual intervention, minimize errors, and save valuable time and costs.
The design of belt conveyors is highly flexible, allowing customization to meet the specific needs of different factories. Whether it’s food, electronics, pharmaceuticals, or cosmetics, belt conveyors provide stable and efficient solutions for transporting products, ensuring that each item is handled accurately throughout the production process.
Additionally, belt conveyors are not just used for transporting goods—they can also integrate perfectly with other automated equipment such as inspection systems, packaging machines, and labeling devices. In the automated packaging process, the role of belt conveyors goes far beyond simple material transport. They significantly improve overall production line coordination, shorten production cycles, and help factories stay competitive by quickly adapting to market demands.
With continuous advancements in technology, modern belt conveyors can now be integrated with smart control systems for automation and real-time data monitoring. This shift towards smart solutions not only boosts production efficiency but also allows factories to continuously adjust and optimize workflows, ensuring that each stage of the process is as efficient and precise as possible.
How Belt Conveyors Improve Efficiency in Packaging Systems
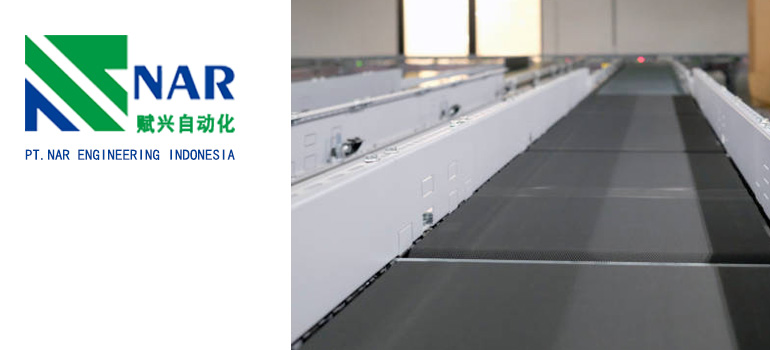
Belt conveyors are essential for optimizing packaging systems in factories, driving efficiency through automation and streamlined workflows. By automating the transport of materials and products, these systems reduce the need for manual handling, saving both time and labor costs while increasing output. Below are key ways in which belt conveyors improve efficiency in packaging systems.
Enhancing Speed and Accuracy with Belt Conveyors
One of the primary benefits of belt conveyors in packaging systems is the significant boost they provide to speed and accuracy. With automated conveyor belts moving products at a consistent rate, the risk of human error is minimized, ensuring that items are consistently packaged and labeled correctly. This high level of precision is crucial for industries like food, pharmaceuticals, and electronics, where strict standards must be met.
By maintaining a steady flow of materials from one stage of the production process to the next, belt conveyors help factories meet high-volume demands, reduce delays, and maintain a fast-paced operation. This speed is especially important in industries where time-sensitive packaging is essential, such as in food production, where the quality of perishable items must be maintained.
Reducing Labor Costs through Automation
Belt conveyors help reduce labor costs by automating the movement of products between different parts of the packaging process. With fewer manual interventions required, the need for large teams of workers handling items on the production floor is minimized. Workers can instead focus on other critical tasks that require human attention, such as quality control or machine maintenance.
This reduction in manual labor not only lowers payroll expenses but also allows for more efficient use of staff. Additionally, by reducing the physical strain on workers, belt conveyors can contribute to a safer work environment, preventing workplace injuries caused by repetitive movements and heavy lifting.
Increasing Throughput and Reducing Downtime
Belt conveyors play a vital role in increasing throughput and minimizing downtime. They operate continuously and reliably, unlike manual labor, which can suffer from fatigue or interruptions. A well-maintained conveyor system can run for extended periods without requiring significant breaks or maintenance, ensuring that packaging operations run smoothly and efficiently.
Furthermore, belt conveyors can be integrated with other automated systems, such as sorting and inspection machines, to create a continuous flow of materials. This integration reduces bottlenecks and minimizes delays, ensuring that the entire packaging line runs at optimal speed. With reduced downtime and fewer interruptions, factories can achieve higher production outputs and meet tight deadlines more effectively.
The Impact of Belt Conveyor for Packaging on Product Quality
Belt conveyors are not just vital for improving the speed and efficiency of packaging systems—they also have a significant impact on the quality of the final product. By ensuring smooth, consistent, and gentle handling of products throughout the packaging process, these systems help maintain the integrity, appearance, and safety of items. Here’s how belt conveyors contribute to enhancing product quality in packaging.
Ensuring Consistent Packaging and Reducing Errors
One of the key advantages of using belt conveyors in packaging is their ability to ensure consistency throughout the production line. With manual handling, there’s always the possibility of human error—whether it’s placing items incorrectly, mislabeling, or damaging fragile products. In contrast, belt conveyors provide a uniform method of transporting goods, eliminating many of these potential errors.
The steady and continuous movement of products along the conveyor belt ensures that each item is packaged in the same way, with consistent labeling, sealing, and portioning. This consistency is essential in industries where product quality and regulatory compliance are paramount, such as pharmaceuticals, food, and cosmetics. By automating these repetitive tasks, manufacturers can ensure that every product meets the same high standards.
Preventing Damage to Products During Transport
In packaging lines that rely on manual labor or poorly designed systems, products can often be jostled, dropped, or damaged as they are handled. This is especially a concern in industries that deal with fragile items, like glass bottles or delicate electronics. Belt conveyors, however, are designed to provide smooth, controlled transport, minimizing the risk of product damage.
The conveyor belts can be customized to suit the product, with special materials and configurations used to cushion and support fragile items. For instance, cushioned or soft surface belts can prevent sensitive items from being scratched or broken during transit. This careful handling helps ensure that the final product reaches the consumer in its best possible condition, reducing waste and returns.
How Belt Conveyors Help Maintain Packaging Standards
Belt conveyors also play a critical role in ensuring that packaging standards are maintained. Packaging isn’t just about placing a product into a box—it also involves ensuring that the packaging material itself is properly applied and sealed. Whether it’s shrink-wrapping, labeling, or sealing, belt conveyors ensure that these processes are completed correctly and consistently.
By keeping products moving at a steady pace, conveyor systems reduce the chances of errors in these tasks. For example, when products are transported along the conveyor to labeling machines, the pace is consistent, and each product is aligned for accurate label placement. This results in packaging that looks professional, adheres to regulations, and maintains the brand’s reputation for quality.
Additionally, belt conveyors often incorporate sensors and control systems that can detect issues, such as misaligned packages or defective seals. If a problem is detected, the system can automatically stop or alert operators, preventing faulty products from reaching the final packaging stage and ensuring that only high-quality products are delivered to consumers.