Summary:
How to Select the Right Conveyor System Accessories for Your Business Needs
Why Conveyor System Accessories Are Critical to Operational Efficiency
Types of Conveyor System Accessories You Should Consider
How to Choose the Right Conveyor System Accessories for Your Industry Needs
Key Factors to Consider When Selecting Conveyor System Accessories
When it comes to optimizing material handling and streamlining operations in industries ranging from manufacturing to logistics, the role of conveyor system accessories cannot be overstated. While conveyor systems are the backbone of efficient production lines, the accessories that accompany them play an equally critical role in ensuring smooth, uninterrupted operations. These accessories are not merely add-ons; they are essential components that enhance the performance, longevity, and safety of your entire conveyor system.
Why Conveyor System Accessories Are Critical to Operational Efficiency
Conveyor system accessories are designed to improve the overall efficiency of material flow within your facility. Without the right accessories, even the most well-designed conveyor system can struggle to meet the demands of your operation. For instance, conveyor belts, rollers, and other related accessories ensure that materials are transported smoothly, without unnecessary friction or delays.
Accessories such as belt cleaners, impact beds, and dust covers are indispensable in maintaining the efficiency of the system. They prevent the accumulation of debris, which can cause conveyor belt jams and disrupt the flow of materials. Rollers, whether they’re idler or return rollers, play a significant role in reducing wear and tear on the conveyor belt, thus extending the lifespan of your equipment.
In industries where high throughput is critical, accessories such as variable speed controllers or automation components allow conveyors to adapt to fluctuating demands, ensuring that the material handling process remains agile and responsive to changes in production schedules. When you invest in the right conveyor system accessories, you create an environment where materials move efficiently, contributing to faster throughput and increased productivity.
The Role of Accessories in Enhancing Conveyor System Longevity
Conveyor systems are often a long-term investment for businesses, and their longevity is directly influenced by the quality and selection of conveyor system accessories. Accessories such as wear-resistant coatings for rollers, vibration dampers, and anti-static devices help reduce wear and tear, protecting the conveyor system from damage caused by prolonged use in harsh conditions.
For example, protective guards and cushioning materials help prevent damage to the system from heavy or sharp-edged items being transported on the conveyor. These accessories act as a buffer, absorbing impacts and preventing the conveyor from taking unnecessary strain, which ultimately helps reduce maintenance costs and extend the life of the system.
Moreover, conveyor belt tracking systems are designed to keep the belt properly aligned, ensuring it runs smoothly without slipping or veering off track. These accessories are crucial for avoiding premature wear on the belt, which can lead to costly downtime and repairs. By ensuring that your conveyor system accessories are of the highest quality and suited to the specific demands of your industry, you help safeguard the longevity of your equipment, saving your business from unnecessary operational interruptions and capital expenses in the long run.
How Proper Accessories Improve Workplace Safety and Reduce Downtime
Safety is a top priority in any industrial environment, and conveyor system accessories play a vital role in reducing risks associated with conveyor operations. For example, safety guards and emergency stop switches are key accessories that protect workers from the potential hazards posed by moving conveyor belts. These safety features ensure that operators can stop the system quickly in the event of an emergency, minimizing the chances of injury.
In addition, anti-slip conveyor belts and edge guards prevent material from falling off the conveyor, which can create hazardous conditions in the workplace. Accessories like dust suppression systems and soundproofing materials can also help mitigate the environmental impact of conveyor operations, reducing the risk of respiratory issues for workers exposed to dust or excessive noise.
By minimizing downtime caused by accidents or damage to the system, proper conveyor system accessories contribute to a safer work environment. The ability to quickly replace or maintain certain components—like belts, rollers, or motors—through easily accessible accessories ensures that any disruptions are dealt with swiftly, allowing the operation to continue without significant delays.
In conclusion, the importance of conveyor system accessories extends far beyond being simple add-ons; they are integral to the efficiency, safety, and longevity of your entire conveyor system. From boosting operational efficiency and ensuring smooth material flow to enhancing the safety of workers and reducing downtime, the right accessories can make all the difference in the performance of your conveyor system. By carefully selecting and maintaining these accessories, businesses can maximize productivity, lower maintenance costs, and extend the life of their equipment—ultimately contributing to smoother, more cost-effective operations.
Types of Conveyor System Accessories You Should Consider
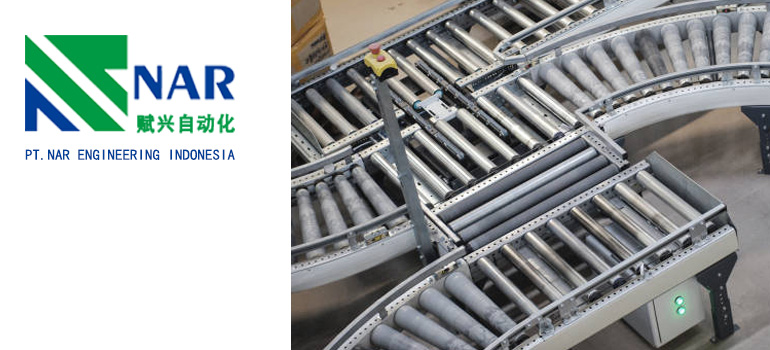
When designing or upgrading a conveyor system, selecting the right accessories is crucial for optimizing its performance, durability, and safety. Conveyor system accessories are essential components that enhance the efficiency, reliability, and safety of your material handling system. Depending on your specific operational needs, there are several types of accessories that can improve productivity, reduce maintenance costs, and extend the lifespan of your equipment. Below are some of the most important conveyor system accessories you should consider:
Conveyor Belts and Rollers: The Foundation of Efficient Material Handling
Conveyor belts and rollers are the core components of any conveyor system. These accessories are responsible for the smooth and efficient transportation of materials across different areas of your facility.
- Conveyor Belts: Conveyor belts are designed to carry materials from one point to another. They come in a variety of materials, including rubber, PVC, and metal, depending on the nature of the products being transported. For example, heavy-duty belts are used for bulk material handling, while lightweight belts are better suited for small items or packaged goods.
- Rollers: Rollers work with the conveyor belt to provide support and reduce friction, allowing the belt to move smoothly. There are different types of rollers, including idler rollers, return rollers, and crowned rollers, each serving a specific purpose to enhance belt alignment and reduce wear.
Without properly selected conveyor belts and rollers, your system may experience issues such as increased friction, uneven movement, and unnecessary wear, all of which can lead to increased maintenance and operational downtime.
Conveyor Belt Cleaners and Maintenance Accessories
Keeping your conveyor system clean and properly maintained is essential to its longevity and performance. Over time, conveyor belts can accumulate dust, debris, and material build-up, which can lead to blockages, reduced efficiency, and even belt damage.
- Belt Cleaners: Belt cleaners are essential for removing debris and material build-up from the surface of the conveyor belt. These cleaners come in various types, such as primary cleaners, secondary cleaners, and scrapers, all designed to handle specific cleaning tasks. Using belt cleaners helps maintain the smooth running of your conveyor system, reducing the risk of jams and damage.
- Belt Tensioners: These accessories help maintain proper tension on the conveyor belt, ensuring it stays properly aligned and operates at optimal performance. Belt tensioners are especially useful for systems that carry heavy loads or are subject to frequent changes in load and speed.
With the right maintenance accessories, you can prevent costly downtime and ensure that your conveyor system continues to operate efficiently for years.
Conveyor System Supports and Frames: Structural Stability
The supports and frames of your conveyor system provide the structural integrity necessary for safe and efficient material transport. Without strong and reliable supports, the conveyor system might become misaligned or unstable, leading to wear and potential failure.
- Support Stands: Support stands are used to hold and stabilize the conveyor system at the required height and position. They ensure that the entire system is level and correctly aligned.
- Frames and Chassis: These are the backbone of the conveyor system, providing the foundation for the entire structure. They are typically made of strong materials like steel or aluminum to ensure durability and strength. The frames are designed to accommodate various conveyor types, including roller conveyors, belt conveyors, and chain conveyors.
By selecting high-quality supports and frames, you ensure the system’s stability and safety, allowing materials to be transported without issues caused by poor structural support.
Conveyor System Guides and Diversion Accessories
In some conveyor applications, materials need to be directed to different pathways or sorted efficiently. Guides and diversion accessories help control the flow of materials along the conveyor system, allowing for greater flexibility and productivity.
- Guide Rails: These rails are used to keep materials properly aligned during transportation. They are especially useful in systems that handle smaller or more fragile items. Guide rails can be adjusted to accommodate different material sizes and ensure that they stay on track throughout the entire conveyor process.
- Chutes and Diverting Systems: These accessories are used to change the direction of materials along the conveyor. Chutes help guide materials from one conveyor belt to another, while diverting systems can sort materials into different bins or containers, speeding up processes like packaging, sorting, or quality control.
These accessories improve the flexibility of the system and ensure that materials are delivered to the correct destinations with minimal interruption.
Safety and Protection Accessories for Conveyor Systems
Safety is a top priority in any industrial environment, and safety accessories for conveyor systems are designed to protect both workers and equipment. These accessories help minimize risks associated with moving conveyor parts, material handling, and system maintenance.
- Safety Guards and Barriers: These accessories are installed around the moving parts of a conveyor to prevent accidental contact with workers. Safety guards can be made from various materials, including mesh or solid metal, and are essential for keeping employees safe while the system is in operation.
- Emergency Stop Buttons: These buttons allow workers to stop the conveyor system immediately in case of an emergency. Emergency stop switches are crucial for ensuring that operators can quickly respond to potential hazards or malfunctions.
- Anti-slip Mats: These mats are installed along conveyor walkways to provide better grip for workers and prevent slips and falls. Anti-slip mats are particularly useful in areas where moisture or other hazardous materials may make the floors slippery.
By incorporating safety and protection accessories, you ensure that your conveyor system meets industry safety standards and minimizes the risk of accidents in the workplace.
In conclusion, selecting the right conveyor system accessories is essential for optimizing the performance, safety, and longevity of your conveyor system. From conveyor belts and rollers to safety guards and maintenance accessories, each accessory plays a critical role in ensuring that your system runs smoothly, efficiently, and safely. By investing in high-quality accessories tailored to your specific operational needs, you can reduce downtime, increase productivity, and extend the life of your equipment.
How to Choose the Right Conveyor System Accessories for Your Industry Needs
Choosing the right conveyor system accessories is essential to ensure your material handling system operates efficiently, safely, and cost-effectively. The correct accessories not only improve the overall performance of your conveyor system but also help reduce downtime, extend the life of the equipment, and enhance workplace safety. However, with a wide variety of conveyor system accessories available on the market, selecting the right ones for your specific industry needs can be a complex task. This guide will walk you through the key factors to consider when choosing conveyor system accessories based on your industry requirements.
Assess Your Industry-Specific Material Handling Needs
The first step in selecting the right conveyor system accessories is to understand the unique material handling needs of your industry. Different industries have different demands when it comes to product types, production processes, and transportation speeds. The accessories you choose should be tailored to these specific needs.
- Manufacturing and Assembly Lines: In these industries, speed and precision are critical. If you are transporting small, heavy, or delicate items, accessories such as accurate conveyor belts, precision rollers, and adjustable guide rails will help ensure smooth material flow and prevent damage.
- Warehousing and Distribution: For businesses involved in storage and distribution, diversion systems, belt cleaners, and slat conveyors are essential. These accessories help sort and manage goods quickly, increasing productivity and reducing delays.
- Food Processing and Packaging: In food handling, hygiene is a primary concern. Stainless steel conveyor belts, washdown systems, and antimicrobial accessories are vital to meet sanitation standards and prevent contamination during the transport process.
Understanding your specific industry requirements will guide you in selecting the most appropriate conveyor system accessories that can handle the demands of your operation effectively.
Consider the Type and Weight of Materials Being Transported
The type, size, and weight of the materials being transported play a crucial role in determining which conveyor system accessories are needed. Heavy, bulky, or delicate materials will have different requirements when it comes to handling, protection, and durability.
- Heavy-Duty Applications: For industries that deal with large or heavy materials, such as automotive, construction, or mining, you’ll need durable rollers that can support high loads, impact beds to cushion heavy falls, and reinforced conveyor belts to handle the strain.
- Lightweight or Small Materials: For industries dealing with smaller, lightweight items (such as electronics, pharmaceuticals, or packaging), you may need high-speed conveyors, precision guides, and low-friction rollers to ensure smooth and efficient movement without damaging the products.
- Delicate Products: If you’re transporting fragile products, such as glass, food items, or electronic components, consider cushioned rollers, anti-static materials, and soft-touch belts that prevent damage during transit. Accessories like slip-resistant surfaces and belt tensioners help maintain control and reduce the risk of product loss.
Choosing accessories based on the specific materials you’re handling will ensure that the system works optimally without unnecessary wear and tear.
Evaluate Conveyor Speed and Load Requirements
Every conveyor system has different speed and load requirements depending on the scale and nature of your operation. Understanding these requirements will help you select the appropriate conveyor system accessories to match.
- High-Speed Operations: In industries such as automotive manufacturing, electronics, or parcel handling, high-speed conveyors are often required to keep up with the fast pace of production. Accessories like high-speed bearings, vibration dampers, and synchronized drive systems are essential for maintaining operational efficiency and reducing mechanical stress on the system.
- Heavy Load Handling: For industries handling large, heavy items like metalworking, construction, or bulk goods, selecting the right conveyor system accessories such as reinforced rollers, heavy-duty motors, and impact-resistant beds is crucial. These accessories ensure that the system can handle the weight and prevent failure due to excessive strain.
By evaluating your speed and load requirements, you can select conveyor system accessories that are appropriately designed to meet the demands of your business.
Factor in Environmental Conditions
Environmental factors, such as temperature, humidity, and exposure to chemicals or corrosive elements, significantly affect the performance of your conveyor system accessories. Choosing accessories that can withstand these conditions is essential for maintaining the longevity of your system and reducing maintenance costs.
- Temperature Extremes: If your conveyor system is exposed to extreme temperatures, either hot or cold, accessories made from heat-resistant materials or cold-resistant compounds are required. High-temperature belts, stainless steel rollers, and temperature-controlled motors are essential for industries such as food processing, chemical manufacturing, or metals.
- Corrosive Environments: For industries such as mining, chemicals, or marine applications, exposure to corrosive substances requires corrosion-resistant materials for both the conveyor belts and accessories. Galvanized steel rollers, polyurethane belts, and coated components are suitable options that will endure harsh conditions and reduce the need for frequent replacements.
- Hygiene Requirements: In food processing or pharmaceutical industries, strict hygiene standards must be met. Washdown conveyors, stainless steel components, and antimicrobial coatings are essential to maintain sanitary conditions.
Considering the environmental conditions where your conveyor system operates helps ensure that you select the correct accessories that will last and perform efficiently in those settings.
Focus on Maintenance and Support Needs
To minimize downtime and ensure long-term performance, consider the maintenance and support needs of your conveyor system accessories. Some accessories are designed to be low-maintenance, while others may require more frequent attention.
- Self-Cleaning Systems: For systems that handle sticky or dirty materials, consider self-cleaning conveyor belts, automatic belt tensioners, and integrated belt scrapers. These accessories help maintain the cleanliness and efficiency of your system with minimal effort.
- Easy-to-Replace Parts: Choose conveyor system accessories that are easy to replace and maintain. Components like modular belt sections, quick-release rollers, and adjustable motor drives reduce downtime when repairs or replacements are needed.
- Monitoring and Control Systems: To prevent unexpected failures and reduce downtime, consider installing real-time monitoring systems that provide alerts for any system malfunctions. These accessories can help you predict maintenance needs and avoid costly breakdowns.
By focusing on maintenance and support features, you can extend the lifespan of your system and ensure smooth operations with minimal disruption.
In conclusion, selecting the right conveyor system accessories is a crucial step in optimizing the efficiency, safety, and durability of your material handling system. By considering factors such as your industry-specific needs, the type and weight of materials being transported, conveyor speed and load requirements, environmental conditions, and maintenance needs, you can make informed decisions that will enhance the performance of your conveyor system. Choosing the correct accessories not only improves operational efficiency but also reduces downtime, enhances safety, and prolongs the life of your equipment.
Carefully selecting conveyor system accessories tailored to your business needs ensures that your material handling processes run smoothly and contribute to overall operational success.
Key Factors to Consider When Selecting Conveyor System Accessories
Choosing the right conveyor system accessories is crucial for maintaining efficiency, ensuring safety, and extending the lifespan of your system. Whether you’re designing a new conveyor system or upgrading an existing one, it’s essential to select accessories that align with your operational needs. However, with a wide range of options available, it can be difficult to determine which accessories will offer the best performance for your specific requirements. To help you make informed decisions, here are the key factors you should consider when selecting conveyor system accessories.
Material Type and Weight
The type of materials being transported is one of the most important factors to consider when selecting conveyor system accessories. Different materials require different accessories for optimal handling. Understanding the material’s characteristics — such as its weight, size, fragility, and abrasiveness — is essential in determining which accessories will provide the best performance and durability.
- Heavy Materials: If your system is designed to carry heavy loads, like metals, construction materials, or large products, you need accessories such as heavy-duty rollers, reinforced conveyor belts, and impact-resistant beds. These accessories are specifically designed to handle higher loads and reduce wear and tear on your equipment.
- Light Materials: For smaller or lighter items like electronics or packaging materials, accessories such as light-duty conveyor belts, precision rollers, and adjustable guides will ensure efficient handling without causing damage to the products.
- Fragile or Delicate Items: If you’re transporting delicate items, such as glass, food, or electronics, consider using cushioned rollers, anti-static conveyor belts, and soft-touch guides. These accessories help prevent damage from impact or friction, keeping products safe during transportation.
By considering the material type and weight, you can ensure that your conveyor system accessories are equipped to handle your products efficiently without causing unnecessary wear or damage.
Conveyor Speed and Load Capacity
Another critical factor when selecting conveyor system accessories is the required conveyor speed and load capacity. The speed at which materials move through your system, as well as the load the system must handle, will influence which accessories are best suited for your needs.
- High-Speed Operations: If your conveyor system operates at high speeds, you need accessories designed to maintain smooth, stable operation. For example, high-speed bearings, precision rollers, and dynamic drive systems will help maintain performance at fast speeds without causing excessive wear or vibration.
- Heavy Load Handling: If your system is required to carry large, heavy items, it’s essential to choose accessories that are built to handle such loads without compromising the system’s structural integrity. Heavy-duty rollers, reinforced drive motors, and high-capacity pulleys are designed to withstand the strain of carrying large materials.
- Variable Load Handling: In many industries, the load carried by a conveyor system can vary depending on the stage of the production process or type of products being handled. To accommodate these fluctuations, consider variable speed drives, adjustable tensioners, and modular belts. These accessories can easily adapt to different load and speed requirements, providing flexibility in your operations.
Matching conveyor system accessories to your system’s speed and load requirements will ensure that your equipment operates at peak efficiency while reducing the risk of damage or failure.
Environmental Conditions
The environment in which your conveyor system operates can significantly impact the performance of your accessories. Factors like temperature, humidity, dust, and exposure to chemicals or corrosive materials can all influence the durability and functionality of your conveyor system accessories.
- Temperature Extremes: For conveyors operating in extreme temperatures, such as in food processing or metalworking industries, accessories made from materials that can withstand high or low temperatures are essential. Heat-resistant belts, cold-resistant rollers, and thermal protection covers ensure that the system continues to perform well under temperature fluctuations.
- Chemical or Corrosive Environments: In industries like pharmaceuticals, chemicals, or mining, conveyors may be exposed to corrosive substances. To prevent degradation and extend the life of your system, choose accessories made from corrosion-resistant materials like stainless steel or high-grade polymers. Polyurethane rollers, coated pulleys, and acid-resistant conveyor belts are ideal for these environments.
- Dusty or Wet Environments: For systems that operate in dusty or wet conditions (e.g., in cement, food processing, or woodworking industries), it’s important to select accessories that are resistant to moisture and dust accumulation. Waterproof motors, dust covers, and washdown systems help maintain performance while preventing contamination and buildup on your system.
By selecting conveyor system accessories that are compatible with the environmental conditions in your facility, you ensure that the system runs smoothly and remains durable under harsh conditions.
Maintenance and Serviceability
The ease of maintenance and serviceability of conveyor system accessories plays a major role in ensuring long-term system efficiency and minimizing downtime. The right accessories should be easy to inspect, maintain, and replace when necessary.
- Modular Components: Accessories such as modular belts, quick-release rollers, and replaceable components make it easier to perform routine maintenance and repairs. These components can be quickly swapped out, reducing downtime during maintenance and preventing lengthy disruptions to your production line.
- Self-Cleaning Accessories: Accessories like self-cleaning conveyor belts, automatic belt tensioners, and integrated scrapers can help reduce the time spent on cleaning and maintenance. These accessories ensure that your conveyor system stays clean and efficient without requiring constant attention.
- Long-Life Components: Investing in high-quality, durable accessories reduces the frequency of repairs and replacements. Accessories made from wear-resistant materials like ceramic-coated rollers or high-durability belts will lower maintenance costs and increase the overall longevity of your conveyor system.
By selecting accessories that are easy to maintain and service, you can minimize downtime and extend the lifespan of your entire conveyor system.
Safety Features
Safety is a top priority when operating any industrial equipment, including conveyor systems. The right conveyor system accessories can help prevent accidents and improve worker safety in your facility.
- Safety Guards and Barriers: Install safety guards around moving parts, such as conveyor belts and pulleys, to protect workers from injury. Safety barriers and mesh enclosures are designed to prevent accidental contact with moving components while ensuring proper airflow and visibility.
- Emergency Stop Systems: Emergency stop buttons or pull-cords should be installed at key locations along the conveyor system to allow operators to quickly halt the system in case of an emergency. Accessories such as light curtains and proximity sensors can also be used to detect obstacles and stop the system automatically if necessary.
- Anti-Slip and Anti-Static Features: For conveyors that operate in environments with slippery floors or sensitive electronic components, anti-slip mats, anti-static belts, and grounding systems are essential for preventing accidents and product damage.
Incorporating safety features into your conveyor system accessories helps protect both workers and the equipment, reducing the risk of accidents and downtime due to injuries.
Selecting the right conveyor system accessories requires careful consideration of various factors, including material type and weight, conveyor speed and load capacity, environmental conditions, maintenance needs, and safety features. By evaluating these factors, you can ensure that your conveyor system is optimized for efficiency, longevity, and safety. Well-chosen accessories will not only improve the performance of your conveyor system but also contribute to a safer, more cost-effective operation in the long run.
Take the time to assess your specific needs, and consult with manufacturers or experts to choose the best accessories that align with your operational requirements. This will help you maximize productivity, minimize downtime, and extend the life of your conveyor system.