Summary:
How Industrial Belt Conveyors Improve Workflow and Increase Productivity
What is an Industrial Belt Conveyor?
How Industrial Belt Conveyors Streamline Material Handling
Enhancing Productivity with Industrial Belt Conveyors in the Workplace
The Economic Impact of Industrial Belt Conveyors on Manufacturing Productivity
In modern manufacturing and logistics, industrial belt conveyor have become essential pieces of equipment that play a pivotal role in improving workflow and enhancing productivity. These conveyors help businesses streamline material handling, reduce manual labor, and optimize production lines. Whether in food processing, automotive manufacturing, or warehouse logistics, industrial belt conveyors are indispensable tools that improve product flow, minimize downtime, and ensure smoother operations.
But what exactly is an industrial belt conveyor, and how do they contribute to workflow efficiency and productivity? In this section, we’ll dive into the basics of industrial belt conveyors, explaining their components, how they work, and why they’re critical to modern industrial operations.
What is an Industrial Belt Conveyor?
An industrial belt conveyor is a mechanical system designed to transport materials from one location to another within a production facility or warehouse. Typically made from materials like rubber, PVC, or metal, the conveyor belt moves continuously in a loop, powered by electric motors. The belt transports items—such as raw materials, components, or finished products—across various stages of the production process.
Compared to manual handling or other types of material transport systems, industrial belt conveyors offer greater automation, efficiency, and safety. These systems can be customized in terms of length, width, speed, and design to suit the specific needs of different industries. Whether it’s for moving heavy machinery parts, small components, or packaged goods, belt conveyors are versatile tools that improve overall operational flow.
The Key Components of an Industrial Belt Conveyor System
Industrial belt conveyor is made up of several key components that work together to ensure efficient material transport:
Conveyor Belt: This is the central component, usually made of durable materials designed to handle the weight and type of material being transported. It moves items across the production floor or warehouse, with the ability to carry heavy or lightweight loads depending on the design.
Drive System: The drive system consists of a motor and a drive pulley, which work together to power the conveyor belt. The motor generates the necessary energy, while the drive pulley ensures the belt moves smoothly.
Rollers and Idlers: Rollers support the conveyor belt and allow it to move efficiently. They reduce friction, ensuring the belt runs smoothly while carrying materials. Idlers are typically used to guide the belt and maintain its proper alignment.
Tensioning System: This system ensures the conveyor belt remains taut, preventing slippage or unnecessary stretching. It helps maintain the proper belt tension, which is essential for smooth operation.
Control System: Modern belt conveyors often come with automated control systems that monitor the speed, load, and operational health of the system. These systems allow for adjustments to be made automatically, enhancing efficiency and reducing the need for manual intervention.
Together, these components ensure that the conveyor system operates efficiently and reliably, reducing downtime and improving overall productivity.
How Industrial Belt Conveyors Streamline Material Handling
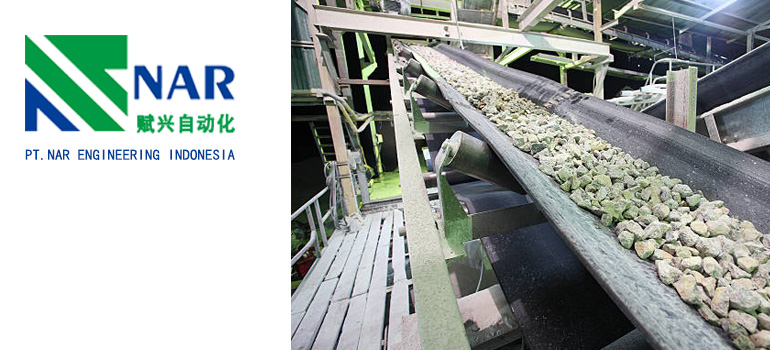
Material handling is a critical aspect of any manufacturing or logistics operation, and efficiency in this area can make a huge difference in productivity and cost-effectiveness. Industrial belt conveyors play a central role in streamlining material handling by automating the movement of goods, reducing the need for manual labor, and minimizing errors. Whether in a manufacturing plant, a warehouse, or a distribution center, conveyors simplify the movement of materials from one point to another, ensuring a smooth and efficient workflow.
In this section, we’ll explore the ways in which industrial belt conveyors help streamline material handling processes, making them faster, more reliable, and cost-effective.
Reducing Manual Labor with Automated Conveying Systems
One of the biggest advantages of industrial belt conveyors is their ability to automate the material transport process. Manual handling of materials—whether moving raw goods or finished products—can be time-consuming, labor-intensive, and prone to human error. Workers are often required to physically lift, carry, and move materials, which can lead to fatigue, inefficiency, and safety hazards.
By implementing an industrial belt conveyor system, businesses can reduce the need for manual labor and allow workers to focus on more complex tasks that require skill and attention. The conveyor system automatically moves items from one location to another, maintaining a steady flow and improving throughput. This not only increases efficiency but also reduces the risk of workplace injuries, as employees are no longer required to lift heavy objects or perform repetitive tasks.
Improving Product Flow Across Multiple Stages of Production
Industrial belt conveyors provide a continuous flow of materials, which is essential for maintaining an efficient production line. In many industries, materials need to move through multiple stages of production, from assembly to quality control, packaging, and shipping. Without an efficient material handling system, this process can become slow and inefficient, causing bottlenecks and delays.
Belt conveyors help keep materials moving smoothly across different stages of production. For example, in an assembly line, materials can be transported from one workstation to the next without interruption, allowing workers to focus on their specific tasks rather than worrying about moving parts. This continuous flow eliminates waiting times between stages and keeps the entire production line running seamlessly.
By reducing delays and keeping materials in constant motion, industrial belt conveyors improve the overall speed and productivity of manufacturing processes. This is especially important in industries where time is a critical factor, such as in automotive or electronics manufacturing.
Minimizing Product Damage and Waste During Transport
In many industries, handling materials improperly or inefficiently can lead to product damage and waste. Whether it’s fragile components or bulk items, improper transport can cause items to fall, become misaligned, or sustain damage during handling. This not only affects product quality but also increases operational costs as damaged goods need to be replaced.
Industrial belt conveyors reduce the risk of such damage by providing a smooth, controlled environment for transporting materials. The conveyor belt moves materials at a steady pace, preventing abrupt movements or drops that could cause damage. Additionally, conveyors can be equipped with features like side rails or specialized carriers that securely hold products in place, further minimizing the risk of mishandling.
By ensuring that products are transported safely and efficiently, industrial belt conveyors help reduce waste, improve quality control, and lower the cost of replacing damaged goods.
Other Key Benefits of Streamlining Material Handling with Industrial Belt Conveyors
While the primary benefits of industrial belt conveyors include automation, improved flow, and reduced product damage, there are several other advantages to consider when using these systems in material handling:
Increased Flexibility and Customization
Industrial belt conveyors can be customized to fit specific material handling needs. Whether you’re moving light items, heavy products, or bulk materials, these systems can be designed with various belt types, widths, speeds, and configurations to suit your operation. For instance, inclined conveyors can move products vertically, while modular belts can be adjusted to fit complex layouts. This level of flexibility ensures that the system can handle a wide range of products and production requirements.
Optimized Space Utilization
Another advantage of belt conveyors is their ability to optimize floor space. In crowded production environments, space is often at a premium. Traditional material handling methods, like forklifts or manual transport, can require a significant amount of floor space and cause congestion. Industrial belt conveyors, on the other hand, can be designed to run along the walls or above production areas, freeing up space for other activities. This vertical or compact design makes the most of available space, improving overall facility layout and workflow.
Scalability and Integration with Other Systems
As businesses grow, so too do their material handling needs. Industrial belt conveyor systems are scalable and can be integrated with other automation systems, such as robotic arms, sorters, and inventory management software. This allows for a seamless and efficient workflow across the entire supply chain, from receiving and storage to production and distribution.
The flexibility and scalability of industrial belt conveyors make them an ideal solution for companies looking to expand their operations without drastically increasing labor costs or operational complexity.
In conclusion, industrial belt conveyors are an invaluable tool for streamlining material handling in modern industries. By automating the movement of goods, improving product flow, reducing manual labor, and minimizing waste and product damage, conveyors enhance operational efficiency and contribute to higher productivity. Moreover, with their scalability and customization options, belt conveyors can be adapted to meet the evolving needs of businesses in various sectors, making them an essential investment for long-term success.
By leveraging the full potential of industrial belt conveyors, businesses can reduce costs, improve efficiency, and stay competitive in an ever-changing market.
Enhancing Productivity with Industrial Belt Conveyors in the Workplace
Industrial belt conveyors are not just tools for material transport—they are productivity powerhouses that help streamline workflows, increase output, and reduce operational costs. By automating the movement of goods and materials, conveyors can transform how a workplace functions, enhancing efficiency and creating a more productive environment. Whether you’re managing a manufacturing plant, a warehouse, or a distribution center, industrial belt conveyors play a crucial role in driving productivity.
In this section, we’ll explore the specific ways in which industrial belt conveyors contribute to workplace productivity and why they are an essential investment for modern businesses.
Speed and Efficiency: How Conveyor Belts Accelerate Production
One of the most significant ways industrial belt conveyors enhance productivity is by speeding up the material handling process. Traditional material handling methods, such as manual labor or forklift operations, can be slow and prone to delays. Workers must stop and start frequently, handle materials manually, and sometimes wait for others to move goods along the line, which can cause bottlenecks and slow down production.
Industrial belt conveyors eliminate these delays by providing continuous, uninterrupted transport of goods. The system is designed to operate 24/7, at consistent speeds, moving materials efficiently through the production line. Whether it’s moving raw materials to the assembly line or transporting finished products to the packaging area, conveyor belts reduce idle time and ensure that operations run smoothly and consistently. This acceleration of processes leads to faster turnaround times, which is key for increasing overall productivity.
For example, in an automotive manufacturing plant, conveyors can move car parts from one station to another with minimal wait time, allowing workers to focus on tasks like assembly or inspection, rather than worrying about transporting materials. This keeps the production process moving at an optimal pace, maximizing output.
Reducing Downtime and Maintenance Costs
Another way that industrial belt conveyors boost productivity is by minimizing downtime and reducing maintenance costs. Traditional material handling methods often require frequent breaks or manual intervention to correct issues like equipment failure, material jams, or human errors. These interruptions can lead to significant delays and affect overall efficiency.
Modern industrial belt conveyors, on the other hand, are equipped with advanced monitoring and control systems that can detect issues before they become major problems. Sensors can monitor belt speed, load weight, and motor function in real-time, alerting operators to potential malfunctions before they cause downtime. This proactive approach to maintenance helps keep the system running smoothly without unnecessary interruptions.
Moreover, many modern conveyor systems are designed to be low-maintenance, with durable components that require less frequent servicing. The use of high-quality materials and design innovations, such as self-lubricating components or easy-to-replace parts, further reduces the need for costly repairs and downtime. This means that industrial belt conveyors can operate for longer periods with fewer disruptions, which contributes directly to increased workplace productivity.
Enhancing Worker Safety and Reducing Injuries
In any workplace, safety is a top priority, and industrial belt conveyors can play an important role in enhancing safety and reducing workplace injuries. Manual material handling involves lifting, carrying, and transporting heavy loads, which can lead to workplace injuries such as back strain, falls, and repetitive stress injuries. These injuries not only affect workers but also reduce productivity due to absenteeism and increased healthcare costs.
By automating material handling with industrial belt conveyors, businesses can minimize these risks. Conveyors eliminate the need for workers to lift or carry heavy items manually, reducing strain and the potential for accidents. Workers are able to focus on their core tasks, such as assembly, quality control, or packaging, instead of physically moving materials. Additionally, conveyor systems can be equipped with safety features like emergency stop buttons, sensors to detect jams, and guards to prevent accidental contact with moving parts.
As a result, the workplace becomes safer, employees are less likely to suffer from injuries, and overall productivity improves. When workers feel safe and are able to perform tasks without the physical strain of material handling, their output and efficiency increase significantly.
The Economic Impact of Industrial Belt Conveyors on Manufacturing Productivity
Industrial belt conveyors are not only valuable tools for enhancing operational efficiency—they can also significantly affect the bottom line. By streamlining material handling processes, improving workflow, and reducing operational costs, industrial belt conveyors contribute directly to the economic success of manufacturing businesses. Whether you’re in a factory, warehouse, or distribution center, these conveyors provide tangible economic benefits that help businesses remain competitive in an increasingly demanding market.
In this section, we’ll explore the economic impact of industrial belt conveyors on manufacturing productivity, highlighting how they reduce costs, improve output, and ultimately provide a high return on investment (ROI).
Lowering Operational Costs with Conveyor Systems
One of the primary economic advantages of industrial belt conveyors is their ability to lower operational costs across various aspects of manufacturing. Manual material handling, forklifts, and other traditional methods often require significant labor, fuel, and maintenance costs. These manual processes can also be less efficient, leading to wasted time, higher risk of injury, and potential delays.
By automating material handling, industrial belt conveyors replace many of these manual tasks, reducing the need for workers to lift, move, and transport materials by hand. This leads to:
Labor Cost Savings: With conveyors handling much of the heavy lifting and material transport, businesses can reduce the number of workers needed for these tasks. This not only reduces direct labor costs but also minimizes expenses related to workplace injuries, employee turnover, and training.
Energy and Fuel Savings: Traditional material handling equipment, such as forklifts, requires fuel and regular maintenance, adding up to significant operating expenses. Industrial belt conveyors, especially energy-efficient models, reduce these costs by providing a more sustainable and cost-effective alternative for transporting goods.
Reduced Equipment Maintenance: Industrial belt conveyors typically require less frequent maintenance compared to forklifts or other heavy machinery. With fewer moving parts and more durable components, these systems are designed for long-lasting performance, reducing both maintenance and repair costs over time.
In sum, industrial belt conveyors reduce the reliance on costly manual labor and inefficient equipment, leading to lower operational costs and higher overall profitability.
Maximizing Space Utilization and Facility Layout Efficiency
Another important economic benefit of industrial belt conveyors is their ability to maximize space utilization in manufacturing facilities. Space is often a premium commodity in manufacturing environments, and optimizing how space is used can have a significant economic impact.
Conveyors help optimize facility layouts by allowing for more compact, organized workspaces. By moving materials in a continuous loop along a set path—often along walls, overhead, or even underground—belt conveyors can free up valuable floor space for other operations. This can lead to:
Improved Production Flow: A more efficient facility layout leads to smoother production flows, reducing downtime and material transport delays. This translates into faster production cycles, which directly impacts profitability.
Higher Throughput: By freeing up space and creating a more organized system, businesses can increase production capacity without expanding their facility or investing in additional space.
Streamlined Inventory Management: Conveyors can be integrated with automated inventory tracking systems, further optimizing storage and materials management. With a more efficient use of space, manufacturers can handle more inventory without needing larger storage areas, which leads to cost savings.
Optimizing floor space and improving workflow can provide a competitive edge by reducing operational bottlenecks, improving cycle times, and allowing businesses to produce more products with the same amount of physical space.
Return on Investment (ROI) and Long-Term Cost Savings
Investing in industrial belt conveyors can seem like a significant upfront expense, but the long-term cost savings and return on investment (ROI) can be substantial. By improving efficiency, reducing labor and energy costs, and minimizing downtime, industrial belt conveyors often pay for themselves over time.
Consider the following factors when calculating ROI for conveyor systems:
Labor Savings: As mentioned earlier, conveyors reduce the need for manual labor, which lowers direct labor costs. The savings in labor can quickly offset the initial cost of the conveyor system.
Increased Throughput: Faster production times and fewer delays mean more products can be produced in the same amount of time. This increases the overall output without requiring additional workers or significant investment in other equipment.
Reduced Downtime: With fewer mechanical failures and the automated nature of conveyor systems, businesses experience less downtime. This means more hours of production, directly contributing to higher output and greater revenue.
Lower Maintenance Costs: Industrial belt conveyor is designed for durability and ease of maintenance. They require less frequent servicing compared to forklifts or manual systems, which means lower maintenance and repair costs over time.
While the initial investment in industrial belt conveyor can vary depending on the complexity of the system and the specific needs of the business, the long-term benefits typically result in a high ROI, making conveyors a smart economic investment