Summary:
Conveyor Belt Loading Systems: A Key to Streamlining Your Logistics Operations
What Are Conveyor Belt Loading Systems and How Do They Work
Key Benefits of Conveyor Belt Loading Systems in Logistics Operations
How to Choose the Right Conveyor Belt Loading System for Your Business
Optimizing Conveyor Belt Loading Systems for Maximum Performance
What Are Conveyor Belt Loading Systems and How Do They Work?
Conveyor belt loading systems are an essential part of modern logistics and material handling operations. These systems are designed to move goods efficiently from one location to another, especially during the loading and unloading phases of the supply chain. The basic idea behind these systems is simple: they use a continuous belt to carry products, materials, or packages along a set path, often at high speeds. This allows for automated handling, which significantly reduces manual labor, increases productivity, and improves the overall efficiency of logistics operations.
The Basic Components of Conveyor Belt Loading Systems
At the heart of any conveyor belt loading system is, of course, the conveyor belt itself. But the system is made up of several key components that work together to ensure smooth operation:
Conveyor Belt: The belt is usually made from durable materials like rubber, plastic, or metal, depending on the type of goods being transported. It’s the part that physically moves products from one place to another.
Drive Motor: This is the powerhouse behind the system. The drive motor powers the conveyor belt, making it move smoothly and consistently.
Rollers: These are positioned along the length of the conveyor system to help guide and support the belt. Rollers ensure that the belt runs properly without slipping or misaligning.
Idlers: These are used to support the belt and help keep it in place, reducing wear and tear.
Loading and Unloading Stations: These are the points where goods are either placed onto or removed from the conveyor belt. In loading operations, products are often placed onto the system by workers or automated machines for transportation to the next stage.
Controls and Sensors: Modern systems often come with advanced controls that can automatically adjust speed, direction, and load size. Sensors may be integrated to detect when products are placed or removed, ensuring smooth flow and preventing jams or delays.
How Conveyor Belt Loading Systems Improve Material Handling
In logistics operations, time is money. Every minute counts when it comes to loading and unloading goods, and that’s where conveyor belt loading systems come in. By automating these processes, companies can greatly increase their throughput. Instead of relying on workers to manually load items onto trucks or containers, the conveyor system can continuously move products with minimal intervention, speeding up the process and ensuring greater efficiency.
The loading process itself is made much simpler and faster. For example, a conveyor belt loading system in a warehouse may automatically deliver goods to a truck waiting to be loaded. Workers may simply monitor the process or adjust the positioning of items, rather than physically lifting or carrying them.
This automation reduces human error, enhances consistency in the operation, and helps businesses meet deadlines more reliably. For industries like e-commerce, where high order volumes need to be processed quickly, conveyor belt loading systems are indispensable for keeping up with demand.
Types of Conveyor Belt Loading Systems Used in Logistics
There isn’t just one type of conveyor belt loading system—different industries and applications may require specific designs. Here are a few common types of conveyor belt systems used in logistics:
Flat Belt Conveyors: This is the most common type used for a wide range of materials, from small packages to larger containers. Flat belt conveyors are versatile and can be customized for different load capacities and operational speeds.
Roller Conveyors: These are often used for heavier loads or for goods that need to be transported with more stability. Instead of a continuous belt, roller conveyors use rotating rollers to move products.
Incline Conveyors: In situations where items need to be moved vertically, incline conveyor systems are used. They are particularly useful for loading or unloading from trucks or bins at different heights.
Z-Shape Conveyors: This type is ideal for changing the flow of goods from one level to another in a compact space. Z-shape conveyors are designed to move products from the ground level to an elevated platform or vice versa.
Automated Guided Vehicle (AGV) Conveyor Systems: These systems combine conveyor technology with robotics to create more flexible and mobile solutions for transporting goods around warehouses or factories. AGVs can navigate around obstacles and adapt to changing layouts in the facility.
Each type of conveyor belt loading system has its own advantages depending on the specific needs of the business, such as the type of goods being handled, space limitations, and required speed of operation.
Key Benefits of Conveyor Belt Loading Systems in Logistics Operations
Conveyor belt loading systems have become integral to modern logistics operations, offering numerous advantages that enhance efficiency, safety, and cost-effectiveness. These systems automate the transportation of goods, significantly improving the speed and reliability of warehouse and supply chain processes. Below, we explore the key benefits that make conveyor belt loading systems a vital asset in logistics operations.
Increased Efficiency and Productivity
One of the most significant benefits of using conveyor belt loading systems is the dramatic increase in operational efficiency. These systems enable goods to be moved continuously and at high speeds without the need for manual intervention. In logistics operations, where speed is crucial, conveyor belts help ensure that products are loaded and unloaded quickly and accurately.
For example, conveyor belt systems allow items to be placed onto the belt at one location and automatically transported to a designated loading area, ready to be loaded into trucks or containers. This reduces the time required to move products manually, leading to faster turnaround times for shipping and receiving.
By automating repetitive tasks, such as loading and unloading, conveyor belts help logistics operations achieve higher throughput, manage larger volumes of goods, and meet tight deadlines without compromising on quality.
Reduction in Manual Labor and Labor Costs
In traditional manual loading and unloading processes, workers are often required to lift, carry, and place products onto trucks or containers, which can be physically demanding and time-consuming. By implementing conveyor belt loading systems, many of these manual labor tasks can be automated, reducing the need for human intervention.
With the automation of loading and unloading, businesses can reduce their dependency on labor-intensive processes, which can lead to significant cost savings. Fewer workers are required for loading tasks, allowing companies to reallocate labor resources to other areas of the operation that may need attention. Moreover, by reducing the potential for worker injuries due to repetitive physical tasks, conveyor belt systems also contribute to lower healthcare costs and workers’ compensation claims.
Improved Safety and Reduced Workplace Injuries
Safety is a top priority in any workplace, especially in logistics environments where workers are often moving heavy loads. Conveyor belt loading systems enhance safety by minimizing the need for employees to physically handle goods that may be heavy, bulky, or hazardous. With fewer workers manually lifting products, the likelihood of workplace injuries—such as back strains, sprains, or falls—can be significantly reduced.
Additionally, modern conveyor belt systems are designed with safety features such as emergency stop buttons, automatic shut-off sensors, and built-in guards to prevent accidents. These safety features, combined with reduced physical strain on employees, create a safer working environment and help companies maintain compliance with workplace safety regulations.
Consistent and Reliable Material Handling
Conveyor belt systems are known for their ability to provide consistent and reliable material handling. Unlike manual processes, where there may be variability in speed, accuracy, or efficiency, conveyor belt loading systems ensure that goods are transported in a steady and controlled manner. This consistency is especially valuable in industries with high volumes of products, such as retail distribution or e-commerce, where fast and reliable throughput is essential.
Moreover, conveyor belt systems can be easily programmed to move goods in a specific order or to follow certain routes, ensuring that products are transported in the most efficient manner possible. This predictability and precision in material handling help prevent bottlenecks, reduce errors, and ensure a smoother flow throughout the logistics process.
Space Optimization in Warehouses and Distribution Centers
Warehouses and distribution centers are often limited in terms of space. However, conveyor belt loading systems can be designed to maximize the available space in these facilities, making operations more efficient without requiring a large amount of floor space. Conveyor systems can be configured to move goods vertically, horizontally, or even along complex routes that make use of overhead space, freeing up valuable floor space for other tasks.
By optimizing space in this way, businesses can improve their storage capacity, reduce congestion, and make better use of their warehouse facilities. Additionally, conveyor belt systems can often be customized to fit the specific layout of a warehouse, ensuring that the system works efficiently within the available space.
Scalability and Flexibility
As businesses grow, so do their logistics needs. Conveyor belt loading systems offer the scalability and flexibility required to meet evolving demands. These systems can be expanded or reconfigured as business needs change, allowing companies to scale their operations without the need for major overhauls.
For instance, additional conveyor lines can be added to accommodate increasing product volumes, or different conveyor types (e.g., roller conveyors, incline conveyors) can be integrated to handle different types of products. This adaptability ensures that logistics operations can keep up with growth, whether it’s handling more inventory, serving additional locations, or processing more shipments.
Conveyor belt loading systems provide a host of advantages that significantly enhance logistics operations. From increasing efficiency and reducing labor costs to improving safety and optimizing space, these systems are essential tools for businesses seeking to streamline their material handling processes. By automating key tasks, conveyor belts help companies achieve faster turnaround times, reduce errors, and create a safer, more productive work environment. Whether in warehouses, distribution centers, or manufacturing plants, these systems offer the reliability and scalability needed to support growing logistics needs in today’s fast-paced world.
How to Choose the Right Conveyor Belt Loading System for Your Business
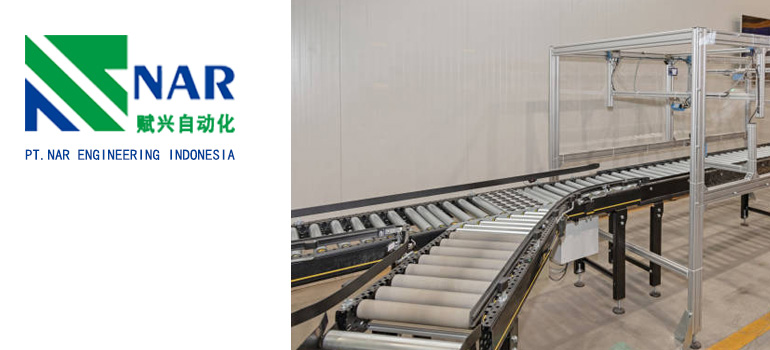
Choosing the right conveyor belt loading system for your business is a critical decision that can impact the efficiency, productivity, and overall success of your logistics operations. A conveyor belt system that’s well-suited to your specific needs will streamline your processes, reduce costs, and improve throughput. However, selecting the right system involves considering several key factors, ranging from the type of goods you handle to space constraints and budget considerations. Below are the key factors you should consider when choosing the perfect conveyor belt loading system for your business.
Understand the Type of Goods You Handle
The first step in choosing a conveyor belt loading system is to understand the types of goods your business handles. Different materials require different types of conveyors, so this is a crucial factor. For example:
Heavy goods: If your business handles large, heavy products, you’ll need a heavy-duty conveyor belt system designed to handle weight and pressure. Consider roller conveyors or heavy-duty flat belts, which are ideal for carrying large, bulky items.
Small or irregularly shaped goods: For small, delicate, or irregularly shaped items, consider using modular belt conveyors or cleated belts. These types of systems provide more stability and prevent goods from slipping during transport.
Fragile or sensitive items: If your business deals with fragile products like glass bottles or electronics, a gentle conveyor system (such as a soft belt conveyor) might be best to avoid damage. Additionally, systems that reduce vibrations or jerks are ideal for these types of items.
Bulk materials: For businesses that handle bulk goods, like grains or aggregates, hopper conveyors or screw conveyors might be the most suitable option.
By clearly understanding the type of goods you’ll be handling, you can narrow down your choices to the most appropriate conveyor systems that provide the right level of support and protection.
Consider the Layout and Space Available
The available space in your warehouse, factory, or distribution center will significantly influence your conveyor belt system choice. A well-optimized layout ensures that the system operates efficiently without taking up too much space or causing bottlenecks. Consider these layout-related factors:
Horizontal vs. vertical transportation: Do your goods need to be moved horizontally, or do they need to be lifted to different levels? For horizontal transport, flat belt conveyors or roller conveyors are great options. For vertical transport, you’ll need incline conveyors or spiral conveyors that can handle height differences.
Space constraints: If space is limited, a modular conveyor system that can be customized and fit within your existing layout is ideal. Alternatively, overhead conveyors or Z-shaped conveyors can maximize vertical space and reduce the amount of floor area required for the conveyor system.
Integration with other equipment: Think about how your conveyor system will integrate with other machinery, such as sorting systems, palletizers, or automated guided vehicles (AGVs). Ensure that the conveyor belt system is compatible with your existing equipment to avoid disruptions.
Choosing a conveyor system that fits well into your available space can improve operational flow and reduce clutter in your facility, leading to smoother operations.
Determine Your Budget and ROI
Conveyor belt loading systems can vary widely in terms of price, depending on their complexity, features, and customization options. It’s crucial to assess your budget before making a decision, as well as to evaluate the potential return on investment (ROI) these systems can provide.
Initial cost vs. long-term savings: While more advanced conveyor systems may require a larger upfront investment, they may lead to significant cost savings in the long term by improving efficiency, reducing labor costs, and minimizing downtime.
Customization and upgrades: Consider whether you’ll need a standard conveyor system or one that’s custom-built for your specific needs. Customization usually comes at a higher cost, but it may be necessary for certain operations. Factor in potential future upgrades, such as automation and AI integration, that could enhance your system as your business grows.
Maintenance costs: Be sure to evaluate the cost of maintaining the system over time. Some conveyor systems may require more frequent maintenance, which could affect your total cost of ownership. Systems that are easier to repair and maintain might save you money in the long run.
A well-chosen conveyor system should fit within your budget and offer a solid ROI by improving efficiency and reducing operational costs over time.
Think About Speed and Load Capacity
The speed and load capacity of your conveyor belt loading system are directly linked to how well the system can handle your logistics operations. Factors to consider include:
Speed: How quickly do you need your goods to be transported? Some conveyor systems allow for adjustable speed settings, so you can tailor the system to meet your needs. If your logistics operation is high-volume and requires fast loading, look for systems that can handle higher speeds.
Load capacity: Determine the maximum weight and volume of the materials that your system will need to carry. If you need to transport large, heavy products, make sure to choose a conveyor system with a sufficient load capacity. For lighter goods, a more economical, less robust system may suffice.
Ensuring that your system is appropriately matched to the speed and load demands of your operation will prevent strain on the system and help avoid costly breakdowns.
Look for Flexibility and Scalability
Business needs can change over time, and so can your logistics requirements. Choosing a conveyor belt loading system that is flexible and scalable can provide long-term benefits as your business grows. Here’s what to keep in mind:
Scalability: If you anticipate growth in your business or an increase in the volume of goods handled, opt for a system that can be easily expanded or upgraded. Scalable systems allow you to add more belts, sections, or even automation features in the future without a major overhaul.
Flexibility: If your product types or handling needs are likely to evolve, consider a modular conveyor system that can be adjusted to accommodate different products or changes in your workflow. Flexible systems also offer the ability to integrate new technologies as they become available.
By selecting a flexible and scalable system, you can ensure that your conveyor belt system continues to meet your operational needs as your business grows and evolves.
Choosing the right conveyor belt loading system for your business is a crucial step in optimizing logistics operations. By considering factors like the type of goods you handle, space constraints, budget, load capacity, and scalability, you can select a system that enhances efficiency and provides long-term value. Take the time to evaluate your specific needs, and ensure that the system you choose integrates smoothly with your workflow and can grow with your business. With the right conveyor system, you can streamline your loading processes, reduce costs, and improve overall productivity.
Optimizing Conveyor Belt Loading Systems for Maximum Performance
To get the most out of your conveyor belt loading system, optimization is key. A well-maintained and properly optimized conveyor system not only improves efficiency but also extends the life of the equipment, reduces downtime, and increases overall productivity. Whether you’re operating in a warehouse, distribution center, or manufacturing facility, maximizing the performance of your conveyor belt loading system requires a combination of regular maintenance, smart automation, and continuous monitoring. Let’s explore the best strategies for optimizing your system.
Implement Regular Maintenance Practices
Like any complex mechanical system, conveyor belt loading systems require regular maintenance to function at their best. Preventative maintenance ensures that potential issues are caught early before they cause major breakdowns. Here are some key maintenance practices to follow:
Inspect Belt Alignment and Tension: Over time, the conveyor belt can slip or become misaligned, causing inefficiencies or damage to the system. Regularly check the alignment of the belt and ensure that it is properly tensioned. A misaligned or loose belt can lead to uneven material flow, increased wear, and even system failure.
Clean the Conveyor System: Dirt, dust, and debris can accumulate on both the conveyor belt and the surrounding components. This buildup can slow the system down and cause friction, leading to premature wear and tear. Regular cleaning of the belt and the rollers helps to maintain smooth operation and avoid material transfer issues.
Lubricate Moving Parts: Conveyor belts have many moving components, including rollers, pulleys, and motors. Proper lubrication of these parts reduces friction, minimizes wear, and prevents overheating. Schedule regular lubrication intervals based on the manufacturer’s recommendations and the operational environment.
Check for Wear and Tear: Wear and tear are inevitable, but frequent inspections allow you to catch problems early. Inspect the belt for cracks, fraying, or holes, and replace worn parts before they cause further damage or interruptions to the system.
By staying on top of routine maintenance tasks, you can keep your conveyor belt loading system running smoothly and avoid costly repairs or downtime.
Use Automation and Integration to Enhance Efficiency
Automation plays a crucial role in optimizing conveyor systems. By integrating automation technologies into your conveyor belt loading system, you can improve speed, accuracy, and reliability while reducing human intervention. Here are some ways to incorporate automation for maximum performance:
Automated Sorting Systems: Integrating automated sorting systems with your conveyor belt can help quickly direct goods to the correct location. This reduces the time spent manually sorting items, speeds up loading processes, and increases throughput.
Sensors and Smart Technology: Use sensors to monitor the movement of goods along the conveyor. These sensors can detect when goods are in place, when a product has moved off the belt, or when a system failure occurs. This real-time data allows you to identify problems quickly and adjust operations accordingly. Smart systems can also automatically adjust the speed and routing of the conveyor to optimize flow.
Automated Loading and Unloading: Automated loading and unloading technologies, such as robotic arms or automated guided vehicles (AGVs), can be integrated with conveyor belt loading systems to reduce manual labor. These technologies can pick up and place items onto the conveyor, increasing loading speed and reducing human error.
Predictive Maintenance: Advanced predictive maintenance technologies use data and machine learning to anticipate when parts of the conveyor system may need attention. This proactive approach to maintenance reduces the risk of unexpected breakdowns and extends the life of the system.
Integrating automation into your conveyor belt loading system not only enhances performance but also future-proofs your operation by keeping pace with advancements in technology.
Optimize Conveyor Speed and Load Capacity
Adjusting the speed and load capacity of your conveyor belt loading system is essential for optimizing its performance. Conveyor systems often come with adjustable settings to match the specific needs of your operation. Here’s how to optimize these settings:
Adjust Conveyor Speed: Conveyor speed must be carefully adjusted to match the pace of the loading or unloading process. If the belt is moving too fast, products may pile up, leading to jams or misalignment. Conversely, if the belt is moving too slowly, it could create bottlenecks and reduce overall throughput. Fine-tuning the speed ensures a balanced workflow that aligns with your logistics requirements.
Right Load Capacity: Ensuring your conveyor system has the right load capacity is crucial to avoid overloading and underperformance. Running a system at maximum capacity can cause excessive wear and tear, while a system that’s under-utilized could be inefficient and waste energy. Know the weight limits of your conveyor belt and adjust the load volume accordingly.
Optimized Material Flow: To maximize efficiency, design the material flow in such a way that products move smoothly from one stage of the operation to the next. Avoid bottlenecks by ensuring that products aren’t waiting too long at any stage, whether it’s loading, unloading, or sorting.
By continuously adjusting the speed and load capacity to match operational demands, you can ensure your conveyor belt loading system operates at peak performance.
Monitor and Adjust for System Downtime
Minimizing downtime is crucial to the efficient operation of your conveyor belt loading system. Any unplanned interruption can delay production, leading to lost time and revenue. Here’s how to reduce downtime and maintain continuous operation:
Real-Time Monitoring: Use real-time monitoring tools and sensors to track the performance of the conveyor belt system. Monitoring systems can alert operators to potential issues before they lead to full system failures. For instance, if there’s an increase in motor temperature or a drop in belt tension, sensors can trigger automatic adjustments or prompt manual intervention before it leads to downtime.
Quick Response to Failures: Ensure that you have a trained team ready to respond quickly in case of an emergency. The faster you can troubleshoot and repair any problems, the less time your conveyor belt system will be down. Regular training for maintenance staff and operators will help speed up the response time during system failures.
Spare Parts and Backup Systems: Having essential spare parts on hand can reduce the time needed to replace damaged components. Consider maintaining a stock of commonly replaced parts such as rollers, belts, and motors, so you can quickly get the system back up and running.
By optimizing system uptime, you can ensure that your conveyor belt loading system operates continuously, maintaining the flow of goods without unnecessary interruptions.
Optimizing conveyor belt loading systems for maximum performance involves a combination of preventive maintenance, automation, load management, and energy efficiency. By following best practices such as routine inspections, integrating automation, and continuously adjusting speed and load capacity, you can improve the overall efficiency and longevity of your system. Additionally, minimizing downtime and optimizing energy use ensures your conveyor belt system operates smoothly, cost-effectively, and sustainably. A well-optimized conveyor system isn’t just an asset—it’s a competitive advantage that can drive the success of your logistics operations.