Summary:
The Future of Logistics: How Automated Belt Conveyors are Revolutionizing Industry
Introduction to Automated Belt Conveyors in Logistics
The Advantages of Automated Belt Conveyors for Supply Chain Efficiency
How Automated Belt Conveyors are Revolutionizing Warehouse Operations
The Impact of Automated Belt Conveyors on Safety and Worker Well-being
The Future of Automated Belt Conveyors: Trends and Innovations
Introduction to Automated Belt Conveyors in Logistics
Automated belt conveyors are becoming a cornerstone of modern logistics and supply chain management. As technology continues to evolve, more industries are turning to automated systems to increase efficiency, reduce costs, and streamline operations. Whether in large warehouses, manufacturing floors, or distribution centers, automated belt conveyors are transforming the speed and accuracy of material handling. In this section, we’ll explore what automated belt conveyors are, how they are impacting the logistics industry, and why they are essential for the future of logistics.
What is an Automated Belt Conveyor?
An automated belt conveyor is a mechanical system powered by electric motors and controlled automatically to transport materials or goods from one point to another. The system typically consists of various components, including belts, motors, rollers, and sensors. Unlike manual handling, automated belt conveyors can significantly improve operational efficiency, reduce human error, and lower labor costs, all while enhancing the speed and precision of material movement throughout a facility.
Automated belt conveyors are widely used in industries ranging from manufacturing to e-commerce logistics, where fast and reliable material handling is crucial. They are often integrated with other automation systems, such as robotic arms or automated guided vehicles (AGVs), to create fully automated workflows.
Key Features of Automated Belt Conveyors
The success of automated belt conveyors in logistics lies in their key features, which make them an attractive solution for businesses looking to enhance efficiency:
Automation & Control: Automated belt conveyors operate without the need for constant manual intervention. They are controlled by advanced software systems that manage the speed, direction, and routing of the goods, ensuring smooth and uninterrupted material flow.
Modular Design: One of the key advantages of automated belt conveyors is their modularity. These systems can be customized to meet the specific needs of a business, whether it’s a large-scale warehouse or a small production line. The modular design also allows for easy expansion or reconfiguration as business needs change.
Smart Monitoring & Diagnostics: Modern automated belt conveyors come equipped with sensors and monitoring systems that track the operational status of the conveyor in real-time. These systems can detect potential issues like jams or mechanical failures, allowing for predictive maintenance and minimizing downtime.
The Growing Role of Automation in Logistics
As e-commerce continues to grow and global supply chains become more complex, traditional manual labor simply cannot keep up with the demand for faster, more efficient operations. Automation is becoming increasingly vital in logistics, with automated belt conveyors playing a central role in this transformation. By implementing automated systems, businesses can not only increase the speed of material handling but also improve inventory management accuracy, leading to more efficient warehouse operations.
For example, automated belt conveyors are used in warehouses to automatically sort and transport products, reducing the need for manual sorting, which can be prone to errors. Additionally, the integration of robotics and AI technologies is enhancing the intelligence of automated systems, allowing them to adapt to changing demands and optimize operations in real-time.
In short, automated belt conveyors are becoming indispensable to modern logistics. They help companies streamline operations, reduce costs, and improve reliability, setting the stage for the next generation of supply chain management.
The Advantages of Automated Belt Conveyors for Supply Chain Efficiency
Automated belt conveyors play a pivotal role in optimizing supply chain efficiency. As supply chains become increasingly complex, businesses are turning to automation to enhance speed, reduce errors, and lower operational costs. In this section, we’ll delve into how automated belt conveyors provide tangible benefits to supply chain operations, helping companies stay competitive in a fast-paced market.
Reducing Labor Costs with Automated Belt Conveyors
One of the most significant advantages of automated belt conveyors is the reduction in labor costs. By automating material handling tasks, companies can decrease their reliance on manual labor, which not only cuts down on wages but also minimizes the risk of human error. Automated systems can work around the clock, handling repetitive tasks like transporting goods between production lines or sorting products, freeing up workers for higher-value roles. Over time, these savings add up, making the initial investment in automation highly cost-effective.
Improving Throughput and Speed with Automation
Automated belt conveyors drastically improve throughput and speed, two critical factors in supply chain efficiency. Unlike manual processes, which are limited by human capabilities, automated systems can continuously move goods with high precision and speed. Whether transporting large volumes of products in a warehouse or facilitating quick product transfers in manufacturing, automated conveyors can significantly reduce cycle times and increase the overall output of operations. This increased speed translates to faster order fulfillment and improved customer satisfaction.
Enhancing Accuracy and Minimizing Errors
In supply chains, accuracy is key, and automated belt conveyors excel in this area. Automated systems are designed to handle materials consistently and accurately, reducing the chances of errors such as misplaced or lost items. With integrated sensors and tracking capabilities, these conveyors ensure that items are sorted, transported, and delivered to the correct locations without manual oversight. This precision helps to minimize costly mistakes, like wrong shipments or inventory discrepancies, and allows businesses to maintain high levels of operational accuracy.
Automated belt conveyors offer a wide range of advantages that directly contribute to improved supply chain efficiency. From reducing labor costs to boosting throughput and enhancing accuracy, they are an essential technology for companies aiming to streamline their operations and stay competitive. As automation continues to evolve, the role of automated belt conveyors in optimizing supply chains will only become more significant, driving cost savings and operational excellence across industries.
How Automated Belt Conveyors are Revolutionizing Warehouse Operations
Warehouse operations have traditionally relied on manual labor to move goods, sort inventory, and fulfill orders. However, as demand for faster, more accurate deliveries increases, the limitations of manual processes have become more apparent. Automated belt conveyors are transforming warehouse management by boosting efficiency, accuracy, and scalability. In this section, we’ll explore how automated belt conveyors are revolutionizing warehouse operations, providing significant advantages over traditional systems.
Streamlining Warehouse Layout with Automated Belt Conveyors
One of the most impactful ways automated belt conveyors are revolutionizing warehouse operations is by optimizing warehouse layout. Traditional warehouses often rely on labor-intensive manual processes that can create bottlenecks and inefficiencies, especially as order volumes rise. With automated belt conveyors, warehouses can be designed for maximum flow, ensuring that goods move seamlessly from one location to another without unnecessary delays.
Automated conveyors enable a more organized and structured warehouse layout, allowing goods to be transported along dedicated paths that reduce human intervention. This organization makes it easier to manage inventory, improves overall space utilization, and reduces the chances of misplaced or lost items. Additionally, conveyors can be strategically placed to ensure a smooth flow of materials from receiving to sorting, storage, and ultimately shipping—reducing downtime and increasing overall throughput.
Integrating Automated Belt Conveyors with Warehouse Management Systems (WMS)
The integration of automated belt conveyors with Warehouse Management Systems (WMS) has further revolutionized how warehouses operate. WMS software helps manage inventory, track shipments, and optimize picking routes in real time. When automated belt conveyors are connected to a WMS, goods can be moved, sorted, and stored with minimal human input.
For example, as orders are received in the WMS, the system can automatically direct the conveyor to transport items from the appropriate storage locations to packing or shipping areas. This integration eliminates manual handoffs and speeds up order fulfillment, reducing the chance of errors and speeding up the entire order-to-shipment process. As a result, warehouses can increase their capacity and reduce operational costs by minimizing labor and improving order accuracy.
Case Studies of Successful Warehouse Automation
Many companies have already implemented automated belt conveyors in their warehouses and seen significant improvements. For instance, Amazon, one of the world’s largest e-commerce companies, has integrated automated conveyors and robotics into its fulfillment centers, enabling lightning-fast order fulfillment. The company uses conveyor systems to transport packages from one part of the warehouse to another, allowing workers to focus on tasks that require human intervention, like picking and packing.
Similarly, large retailers like Walmart and Target have implemented conveyor systems to improve the speed and accuracy of inventory sorting, reducing time spent on manual sorting. By automating these processes, these companies have been able to handle increasing volumes of goods without expanding their workforce, thus improving efficiency while keeping labor costs in check.
Another example is Zara, which uses automated belt conveyors in its warehouse to support its just-in-time inventory model. Automated systems move products from sorting stations to the distribution area, ensuring that orders are fulfilled quickly and efficiently, which is critical to their fast-fashion model.
Automated belt conveyors are transforming warehouse operations by enhancing the flow of materials, improving inventory management, and integrating with Warehouse Management Systems (WMS) for greater precision and speed. As demonstrated by leading companies in e-commerce, retail, and manufacturing, automation in the warehouse not only increases operational efficiency but also provides the flexibility needed to adapt to growing demands. The future of warehouse operations is undoubtedly tied to automation, and automated belt conveyors are at the forefront of this revolution, making logistics faster, more reliable, and cost-effective.
The Impact of Automated Belt Conveyors on Safety and Worker Well-being
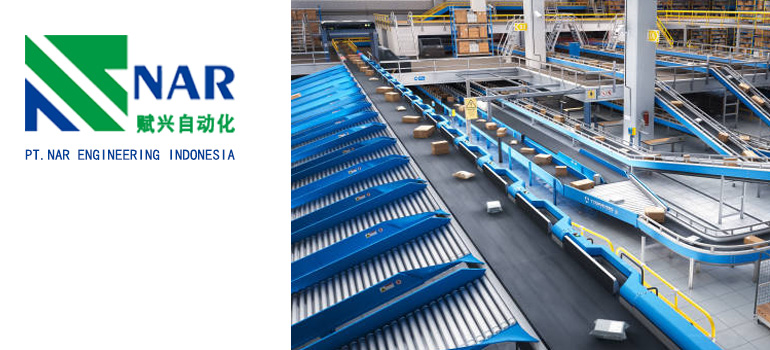
As industries continue to adopt automation, one of the most significant benefits of automated belt conveyors is their positive impact on workplace safety and the overall well-being of workers. Traditionally, manual material handling in warehouses, factories, and distribution centers involved physically demanding tasks that could lead to injuries and strain over time. By integrating automated belt conveyors into operations, businesses are not only boosting productivity but also creating safer, healthier work environments. In this section, we’ll explore how automated belt conveyors improve safety and enhance worker well-being.
Reducing Workplace Injuries with Automated Systems
Manual material handling—such as lifting, carrying, and moving heavy loads—is a major cause of workplace injuries, particularly musculoskeletal disorders (MSDs) and back strains. Automated belt conveyors significantly reduce the physical strain on workers by taking over these tasks, reducing the need for employees to lift or transport heavy items manually. With the conveyors handling the movement of goods across long distances or between stations, workers can focus on higher-level tasks that don’t involve heavy lifting.
By automating repetitive, physically demanding processes, companies can drastically reduce the risk of injuries related to fatigue, poor posture, and improper lifting techniques. This not only protects the physical health of workers but also lowers the number of work-related accidents, ultimately improving the overall safety record of a facility.
How Automation Frees Workers for Higher-Value Tasks
With the routine tasks of transporting and sorting goods automated, workers are freed up to focus on higher-value and more specialized jobs. Instead of spending their days manually moving items from one location to another, employees can engage in more strategic activities, such as quality control, inventory management, and process optimization. This shift not only reduces the physical toll on workers but also improves job satisfaction by offering more intellectually stimulating and rewarding tasks.
In fact, many workers appreciate the opportunity to engage in roles that require problem-solving and critical thinking, as opposed to the monotony of repetitive manual labor. The transition to automation allows for a more diverse and engaging work environment, which can positively impact morale and retention rates.
The Role of Automated Belt Conveyors in Creating Safer Work Environments
Automated belt conveyors contribute to safer work environments in several key ways:
Reduced Human Error: Automation minimizes the risk of mistakes caused by human fatigue, distractions, or inexperience. For example, automated systems consistently handle materials with precision, ensuring that items are placed in the right spots, sorted accurately, and transported on time. This reduces the likelihood of errors like misplaced goods, which could lead to accidents or further complications.
Improved Workplace Organization: Automated belt conveyors help organize the flow of materials, ensuring that products move efficiently and without interference. This organization reduces clutter and congestion in the workspace, preventing accidents such as trips, falls, and collisions. In many facilities, improved organization also means that workers can operate in a cleaner, more controlled environment, which further contributes to safety.
Advanced Safety Features: Many modern automated belt conveyors come equipped with advanced safety features, such as sensors, emergency stop buttons, and automatic shutdown systems. These features help prevent accidents caused by unexpected malfunctions or operator errors. Additionally, conveyor systems can be programmed to automatically slow down or stop if an obstacle is detected, reducing the risk of injury during maintenance or unexpected events.
Mental and Emotional Well-being of Workers
In addition to physical safety, automated belt conveyors contribute to the mental and emotional well-being of workers. By taking over the most physically demanding tasks, automation reduces stress and fatigue, allowing workers to feel less overwhelmed by the constant physical demands of their job. Workers who are less physically stressed are likely to experience fewer mental health issues related to workplace pressure, fatigue, or burnout.
Moreover, the implementation of automation often leads to better work-life balance for employees. As automation increases efficiency, companies may be able to reduce overtime and labor-intensive schedules, allowing workers more time for personal and family activities. This contributes to better overall well-being and higher employee satisfaction.
Automated belt conveyors are not only transforming the efficiency of supply chains and warehouse operations but are also playing a crucial role in improving workplace safety and worker well-being. By reducing the need for physical labor, automating repetitive tasks, and enhancing the organization of workspaces, these systems help create safer, more efficient, and healthier work environments. As industries continue to adopt automation, the focus on worker safety and mental well-being will only grow, making automated belt conveyors an essential part of the future of work.
The Future of Automated Belt Conveyors: Trends and Innovations
As automation continues to shape industries around the world, the future of automated belt conveyors looks increasingly promising. These systems, which have already revolutionized material handling in industries like manufacturing, warehousing, and logistics, are evolving rapidly with the integration of cutting-edge technologies. In this section, we’ll explore the latest trends and innovations that are poised to further enhance the capabilities of automated belt conveyors, making them smarter, more efficient, and more adaptable to the changing needs of businesses.
AI and Robotics in Automated Belt Conveyor Systems
One of the most exciting developments in the future of automated belt conveyors is the integration of artificial intelligence (AI) and robotics. These technologies are pushing the boundaries of what conveyor systems can do, making them more flexible and capable of handling complex tasks that were once considered out of reach.
AI-powered conveyor systems can analyze data in real-time, allowing them to optimize routing, adjust speeds, and anticipate maintenance needs based on predictive algorithms. For example, if a particular part of the conveyor is showing signs of wear, the system can automatically adjust or schedule preventive maintenance to avoid downtime. AI can also help conveyors “learn” and adapt to new workflows, improving efficiency as the system is used over time.
In addition to AI, robotic arms and automated guided vehicles (AGVs) can be integrated with conveyor systems to create highly sophisticated, fully automated production lines. These robots can handle tasks such as picking, sorting, and packaging items directly from the conveyor, reducing human intervention and speeding up the entire material handling process.
The Integration of IoT for Smarter Conveyor Operations
The Internet of Things (IoT) is another game-changing technology that is transforming automated belt conveyors. By embedding sensors and connected devices into conveyor systems, businesses can gather vast amounts of real-time data that provide deep insights into conveyor performance, product flow, and system health. This data can be analyzed to optimize operations and detect potential issues before they become problems.
For example, IoT-enabled conveyors can monitor belt speed, temperature, and load conditions, sending alerts to operators or maintenance teams when a part is functioning outside of normal parameters. This allows for predictive maintenance, meaning repairs or replacements can be done proactively before a failure occurs, minimizing downtime and improving system reliability.
Additionally, the ability to track goods via IoT-equipped conveyors can improve inventory management and provide full transparency of the supply chain. This data can be accessed remotely, enabling managers to make real-time decisions and ensuring that products are tracked and delivered with the highest level of accuracy.
Autonomous Belt Conveyors and Self-Driving Systems
As industries continue to pursue fully automated and autonomous operations, autonomous belt conveyors are becoming a key focus for the future. These conveyors go beyond traditional automation by incorporating self-driving technology and advanced navigation systems to move goods around a facility with minimal human input.
Self-driving conveyor systems can adapt to their environment, adjust to changing conditions, and navigate through complex layouts without human intervention. For example, using a combination of sensors, cameras, and AI, autonomous belt conveyors can change paths, avoid obstacles, and even merge with other conveyor lines as needed, all without direct control from operators.
These autonomous systems will be particularly beneficial in large warehouses and distribution centers, where they can work alongside automated vehicles, robots, and other automated machinery to move products quickly and efficiently across vast areas. The ability of autonomous conveyors to “think” and adjust on the fly means fewer manual interventions and a smoother flow of goods through the facility.
Sustainability and Energy-Efficient Conveyor Systems
Sustainability is another major trend shaping the future of automated belt conveyors. As companies look for ways to reduce their environmental footprint, energy-efficient conveyors and sustainable materials are becoming more important.
Next-generation automated conveyors will use less energy, relying on more efficient motors, energy-saving designs, and better utilization of regenerative braking technology. Regenerative braking captures energy produced during deceleration and stores it for later use, reducing overall energy consumption. Additionally, many manufacturers are now designing conveyors with lightweight, durable materials that reduce the overall energy required to operate them.
There is also an increasing emphasis on reducing waste in conveyor systems. For example, modular conveyor systems that can be easily reconfigured or repurposed help extend the lifespan of the equipment and reduce the need for frequent replacements. Using eco-friendly materials in the production of conveyor belts and components further supports the push for sustainability in material handling systems.
Smart and Modular Conveyor Systems for Greater Flexibility
In the future, conveyor systems will become even more flexible and adaptable, allowing businesses to reconfigure their operations with minimal downtime or cost. Modular conveyor systems, which can be easily expanded, contracted, or reconfigured, will provide companies with the flexibility they need to respond quickly to changing production demands or supply chain disruptions.
These smart conveyor systems will also feature more intuitive control interfaces, allowing operators to easily adjust parameters, reprogram tasks, and even remotely control the system. The integration of cloud-based platforms will allow businesses to monitor and manage multiple conveyor systems across different locations in real time, providing centralized control and increasing operational flexibility.
The future of automated belt conveyors is incredibly exciting, driven by innovations in AI, robotics, IoT, sustainability, and autonomous technology. As these systems become smarter, more efficient, and more adaptable, they will play an even more significant role in revolutionizing supply chains, manufacturing, and logistics. By embracing these trends and innovations, businesses can not only optimize their material handling operations but also position themselves at the forefront of the automation revolution. The next generation of automated belt conveyors will bring higher levels of productivity, greater operational flexibility, and more sustainable practices, making them indispensable to the future of industrial operations.