Summary:
8 Conveyor System Design Mistake
Conveyor system design mistakes
How to avoid mistakes and solve them?
Are you considering a new conveyor system design but not sure if it’s the right decision? Before committing to a large investment, it’s important to make sure that all your bases are covered and understand the potential risks associated with any new project.
In this blog post, I will share insights into the common mistakes made in conveyor system design. It will help you avoid those same pitfalls.
Every design needs thorough analysis before implementation! After reading through this article, you will have increased confidence in making your final decision.
Conveyor system design mistakes
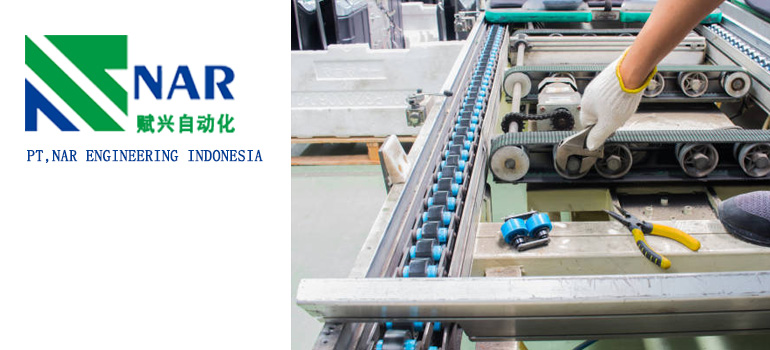
Some of the designed conveyor systems encounter the following mistakes:
Insufficient Load Capacity
Failing to accurately determine the maximum load capacity of the conveyor system can result in equipment failure, decreased efficiency, and potential safety hazards. It is crucial to consider all factors that could impact the load capacity, such as the type of material being conveyed, the conveyor speed, and the angle of inclination or decline.
Improper Belt Selection
Choosing the wrong type of conveyor belt for the intended application can lead to premature wear, belt slippage, and increased maintenance requirements. Proper belt selection is critical to the performance and lifespan of the conveyor system.
Inadequate Tracking Mechanisms
Failure to implement effective tracking mechanisms can result in belt misalignment, which can cause excessive wear, increased maintenance, and even conveyor system breakdown. Installing reliable tracking devices, such as sensors or rollers, can ensure the proper alignment of the conveyor belt.
Incorrect Incline/Decline Angle
Setting the incline or decline angle too steep or shallow can cause material spillage, reduced conveying efficiency, and potential product damage. Calculating and setting the optimal angle for efficient material flow is critical to the performance of the conveyor system.
Lack of Proper Maintenance Plan
Neglecting regular maintenance and inspections can lead to unexpected breakdowns, increased downtime, and costly repairs. Establishing a comprehensive maintenance plan that includes routine inspections, lubrication, belt tension adjustments, and component replacements is critical to the longevity and efficient operation of the conveyor system.
Inadequate Safety Measures
Failing to incorporate essential safety features, such as emergency stop buttons, guardrails, and safety interlocks, can compromise worker safety and increase the risk of accidents.
Ensuring compliance with relevant safety standards and implementing necessary safeguards should be a top priority during the design phase. Worker safety should always be the primary concern when designing and installing a conveyor system.
Insufficient Space Allocation
Not allocating enough space for the conveyor system can restrict material flow, hinder maintenance access, and compromise worker safety. It is essential to plan for sufficient space to accommodate the conveyor system, including loading and unloading areas, transfer points, and maintenance access points.
Poor Integration with Existing Equipment
Incompatibility and poor integration with existing equipment, such as packaging or sorting machinery, can lead to inefficiencies, bottlenecks, and increased downtime.
The conveyor system must be designed to seamlessly integrate with other equipment during the design phase. Compatibility with existing equipment should be carefully considered, and any necessary modifications made to ensure smooth and efficient operation.
Failure to integrate the conveyor system with other equipment can lead to significant issues during operation, causing delays and lost productivity.
How to avoid mistakes and solve them
Designed conveyor systems are crucial components that boost efficiency and productivity in manufacturing plants, distribution centers, and other industrial settings.
Conveyor system design mistakes can lead to increased downtime, reduced throughput, product damage, worker injuries, and ultimately, loss of revenue. Therefore, it is essential to prevent these errors from occurring and address them promptly if they arise.
Prevention Strategies
Conduct a detailed analysis of the anticipated load requirements
Before selecting a conveyor system, it is vital to determine the total weight and dimensions of the products or materials to be transported. A proper analysis can help identify the required conveyor load capacity. To accommodate changes in demand, it is recommended to select a system with a higher load capacity.
Consider material properties and environmental conditions
Material properties such as size, shape, weight, and temperature affect the conveyor belt selection.
Exposure to heat, moisture, chemicals, and abrasives can deteriorate the belt, leading to failure and downtime. Consulting with belt manufacturers and conveyor system experts can help determine the most appropriate belt type and design for a specific application.
Incorporate effective tracking mechanisms
The conveyor belt tracking mechanism is essential to prevent the belt from veering off-course and causing product damage, spillage, and premature wear.
Installing aligning rollers, adjustable belt tensioners, or automated tracking systems can maintain consistent belt alignment. Regular inspections and adjustments can detect and correct tracking issues to prevent further damage.
Determine optimal incline/decline angles
The slope angle determines how materials flow down the conveyor system. An incorrect slope can lead to spillage, jamming, or material damage.
It is essential to calculate the optimal angle based on material properties, flow characteristics, and conveyor system limitations. Testing and fine-tuning the angle during operation can help optimize the performance.
Create a comprehensive maintenance plan
Conveyor systems need regular maintenance to keep the components in good working condition. Establishing a maintenance plan that includes scheduled inspections, cleaning, lubrication, and replacement of worn components can prevent breakdowns.
Keeping detailed records of maintenance activities can assist in detecting issues early and tracking the overall system’s performance.
Ensure adequate safety measures
The designed conveyor systems pose risks to workers’ safety, such as entanglement, crushing, and falling. It is critical to incorporate essential safety features such as emergency stop buttons, guardrails, safety interlocks, and warning signs.
Furthermore, training employees on proper safety procedures and regular safety audits can prevent accidents and ensure compliance with safety regulations.
Consider available space when designing the layout
Space limitation can impact the conveyor system’s layout and the space required for material flow, equipment maintenance, and worker access.
Optimizing the layout and utilizing available space efficiently can improve the system’s performance and flexibility. Considering future expansion needs can prevent limitations in the future.
Possible Solutions
Upgrade the conveyor system capacity
If a conveyor system lacks sufficient load capacity, upgrading the system to handle anticipated loads can prevent failure and downtime. Exploring equipment options with a higher load capacity or adding additional equipment components may be a solution.
Replace the conveyor belt
Worn or damaged conveyor belts require replacement to prevent failure and avoid downtime. Ensuring the correct belt type and design for the application is essential to avoid future problems.
Install effective tracking mechanisms
To address tracking issues, installing aligning rollers, adjustable belt tensioners, or automated tracking systems can correct the problem.
Adjust the incline/ decline angle
Fine-tuning the slope angle can help correct material flow, prevent spillage, and avoid damage.
Perform maintenance tasks promptly
Addressing maintenance issues early and regularly can prevent further damage and extend the system’s lifespan.
Add safety features
Incorporating essential safety features can reduce workplace injuries and prevent accidents. Ensuring proper employee training and regular safety audits can identify potential hazards and ensure compliance.
Re-design the layout
If space is a limitation, optimization of the system layout and re-working of the existing space allocations can improve the performance and prevent future issues.
Take Away
Preventing and addressing conveyor system design mistakes requires proper planning, design, maintenance, and troubleshooting. Incorporating the above guidelines can help boost efficiency, productivity, and workplace safety.
Consultation with designed conveyor system experts, belt manufacturers, and equipment suppliers can provide further insights into the most appropriate conveyor system design for specific applications.
Ultimately, taking the time to review and address design mistakes will lead to a more reliable and efficient conveyor system.